Art der Wärmebehandlung von Stahl, Metall und Legierung. Arten der Wärmebehandlung von Metallen
Metallwärmebehandlung
Für den weiteren Betrieb von Teilen und Komponenten von Geräten sind jedoch häufig sehr unterschiedliche Eigenschaften erforderlich - Festigkeit, Härte, Steifigkeit usw. Zu diesen Zwecken ist die Wärmebehandlung von Metallen vorgesehen.
Die Essenz von Wärmebehandlungsprozessen
Die Aufgaben verschiedener Wärmebehandlungstechnologien sind:
- Gewährleistung der günstigsten Mikrostruktur von Stählen und Legierungen;
- Erreichen des gewünschten Härtegrades: entweder in einer Zone mit dünner Oberfläche (oder unter der Oberfläche) oder entlang des gesamten Querschnitts des Werkstücks;
- Korrektur der chemischen Zusammensetzung in den Körnern der Makrostrukturen verschiedener Legierungen.
Im ersten Fall ist es notwendig, den maximalen Grad an Homogenität der Eigenschaften von Metallen sicherzustellen, was beispielsweise für die nachfolgende mechanische oder - insbesondere - verformende Verarbeitung wichtig ist. Infolgedessen sind die Bedingungen des Werkstücks, das sich auf allen drei Koordinatenachsen bildet, gleich, und die Zurückweisung des endgültigen Teils ist ausgeschlossen.
Darüber hinaus ist die Ausrichtung der Mikro- und Makrostrukturen für Umformprozesse erforderlich, um den Verformungsgrad von Halbzeugen zu erhöhen und die Form des Werkstücks näher an die Form des Endprodukts heranzuführen. Darüber hinaus für die geringste Anzahl von Übergängen und mit dem minimal erforderlichen Geräteaufwand.
Die Änderung der Härte (infolge der Wärmebehandlung) zielt darauf ab, die Leistung der Teile zu verbessern. Da die Betriebsbedingungen sehr unterschiedlich sein können, wird der Komplex der physikomechanischen Eigenschaften streng individuell ausgewählt: Es gibt keine universellen Verfahren zur Wärmebehandlung von Legierungen mit unterschiedlichen Zusammensetzungen.
Eine Änderung der chemischen Zusammensetzung in den Körnern der Mikrostruktur aufgrund der Bildung neuer Verbindungen erhöht in den meisten Fällen nicht nur die Härteindizes, sondern auch die Verschleißfestigkeit von Teilen, die unter erhöhter Reibung, Temperatur oder gegen normale spezifische Belastungen betrieben werden müssen.
Urlaub mildern
Die erste Gruppe von Wärmebehandlungstechnologien für verschiedene Legierungen, einschließlich Stahl, umfasst das Glühen und Anlassen. Die zweite - Härten, Normalisieren, Verbessern, Altern, Kältebehandlung. Im dritten - alle Arten der thermochemischen Behandlung.
Glühen
Die Essenz der Prozesse, die in der Struktur der meisten zu glühenden Legierungen ablaufen, besteht darin, die ausgeglichenste Struktur des Werkstücks sicherzustellen, bei der entweder keine inneren Spannungen vorliegen oder deren Gehalt recht niedrig ist und daher die spätere Bearbeitbarkeit von Metallen / Legierungen nicht beeinträchtigt.
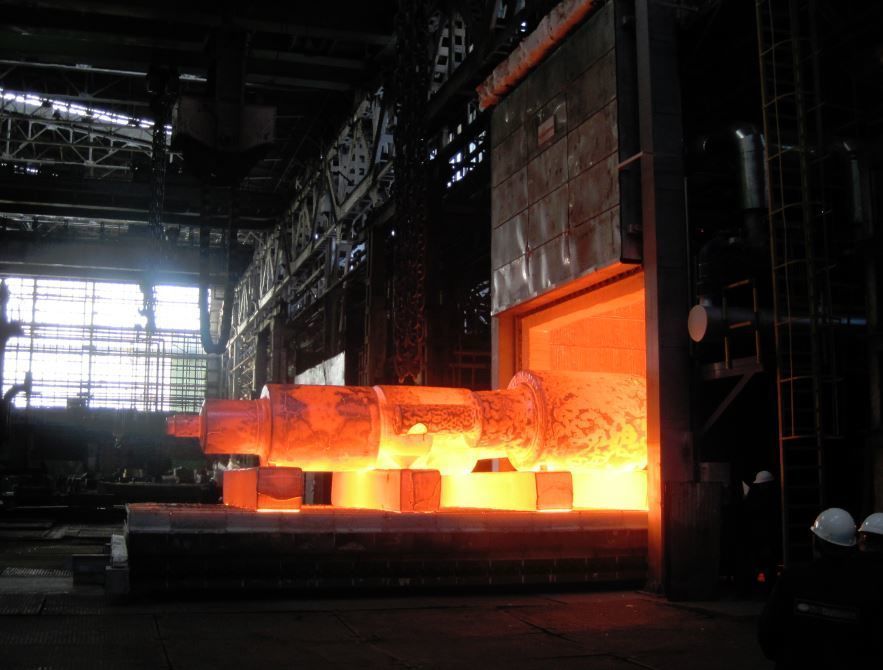
Die anfängliche Struktur fast aller Legierungen und Stähle besteht aus ziemlich großen Körnern, zwischen denen sich Einschlüsse und Verunreinigungen befinden, hauptsächlich Schwefel und Phosphor. Dies erhöht die Sprödigkeit des Metalls, was wichtig sein kann, wenn aus Block- (oder Draht-) Produkten komplexer Konfiguration geformt wird. Daher ist es notwendig, die Korngröße zu reduzieren und ihr eine optimale Ellipsoidform zu geben, bei der die mechanischen Eigenschaften entlang aller drei Koordinatenachsen ungefähr gleich sind.
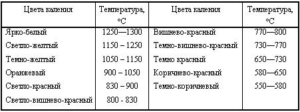
Zu diesem Zweck muss der anfängliche Knüppel auf eine Temperatur von 50 ... 70 0 C über der Temperatur des Beginns der austenitischen Umwandlung erhitzt werden. Das Ergebnis ist die Bildung kleiner und gut orientierter Austenitkörner zwischen den Körnern der Hauptstrukturkomponenten von Stahl - Ferrit und Zementit. Austenit wird aus Perlit gebildet - einer Struktur mit den größten Körnern, die zur erhöhten Zerbrechlichkeit eines Barrens beiträgt. Die austenitische Umwandlung verläuft für die meisten Legierungen ziemlich langsam, daher ist das Tempern ein langwieriger Vorgang, der mindestens eine Stunde dauern sollte.

Die zweite wichtige Aufgabe des Glühens besteht darin, die inneren Spannungen, die sich während der Verarbeitung im Werkstück bilden, durch Druck im kalten Zustand zu beseitigen. Tatsache ist, dass jede Verformung mit dem Zerkleinern von Körnern der Ausgangsstruktur von Stählen und Legierungen einhergeht. Infolgedessen werden die Körner größer, der Verformungswiderstand nimmt zu, was nicht nur eine erhöhte Verformungskraft erfordert, sondern auch die Zerstörung des Halbzeugs verursacht, dessen Verformungsgrad den kritischen Wert für dieses Metall überschreitet.
Dementsprechend wird für die Durchführung der ersten Aufgabe die Technologie des Hochtemperaturglühens verwendet (für Stähle variiert sie je nach Kohlenstoffgehalt zwischen 550 ... 750 0 С) und beim zweiten - Niedertemperaturglühen (180 ... 220 0 С).
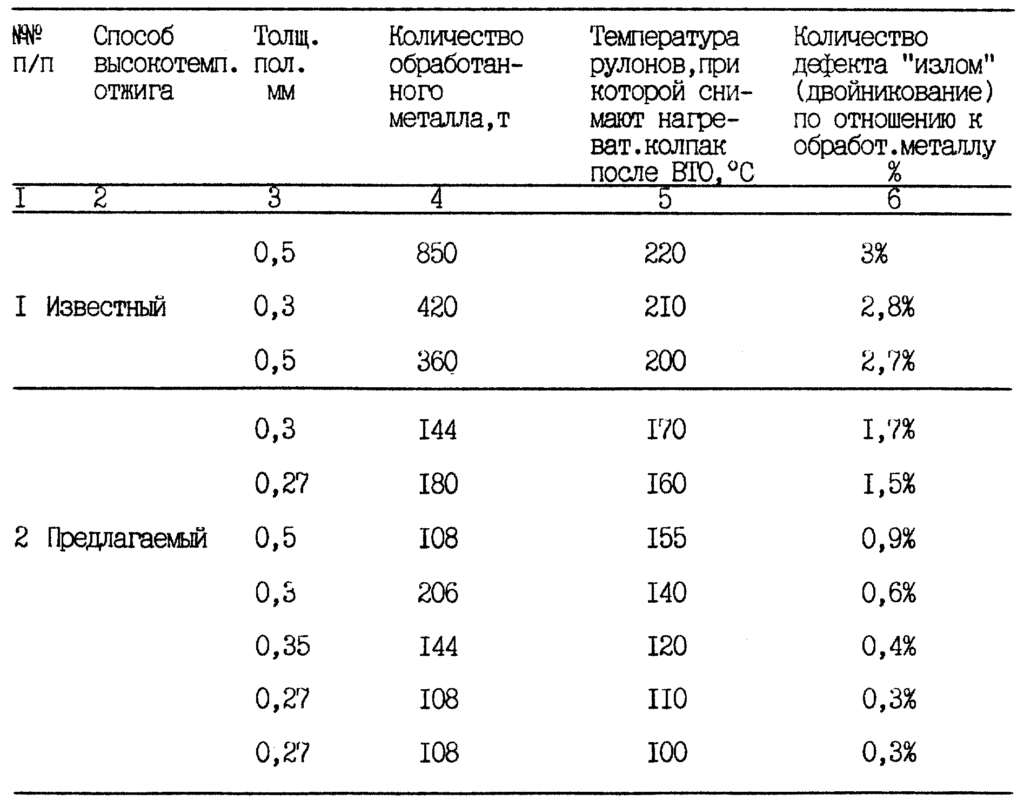
Das Erhitzen erfolgt langsam, gefolgt vom Aussetzen des Produkts bei einer bestimmten Temperatur, gefolgt von einem langsamen Abkühlen. Bei legierten Stählen und Legierungen wird eine solche Abkühlung mit einer besonders geringen Geschwindigkeit im Ofen selbst durchgeführt, in dem das Glühen stattfand.
Urlaub
Der Urlaub durch Technologie ähnelt dem Glühen, wird jedoch nicht mit einem Werkstück, sondern mit einem fertigen Produkt durchgeführt und hat daher andere Aufgaben - den Abbau innerer Spannungen nach der Wärmebehandlung, die zur Erhöhung der Härte des Teils durchgeführt wurde.
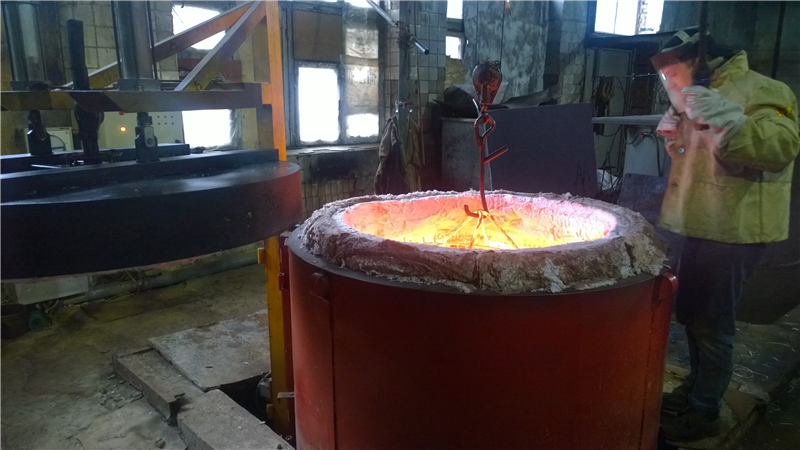
Urlaub ist kein eigenständiger Prozess der Wärmebehandlung. Im Gegensatz zum Glühen erfolgt das Tempern manchmal in mehreren Stufen: In den meisten Fällen gilt dies für Produkte, für deren Herstellung verschiedene Arten von hochlegiertem Stahl verwendet wurden.
Abschrecken
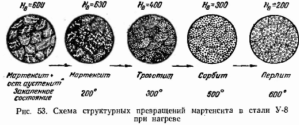
Das Abschrecken besteht aus dem schnellen Erhitzen des Vorformlings auf die Temperatur des Endes der austenitischen Umwandlung (900 ... 1100 0 С - für kohlenstoffarme Stähle, 750 ... 850 0 С - für kohlenstoffreiche Stähle) und dem anschließenden schnellen Abkühlen in speziellen Abschreckmedien. Als letzteres wird Wasser (für unkritische Produkte) oder Öl verwendet.
Die Härtungsmodi sind sehr unterschiedlich. Der Hauptfaktor für die Abschreckleistung ist die Intensität der Martensitbildung in der Struktur - eine Hochtemperaturkomponente, die dem Metall oder der Legierung eine erhöhte Härte verleiht.
Die Bedingungen für die Bildung von Martensit werden durch die folgenden Umstände bestimmt:
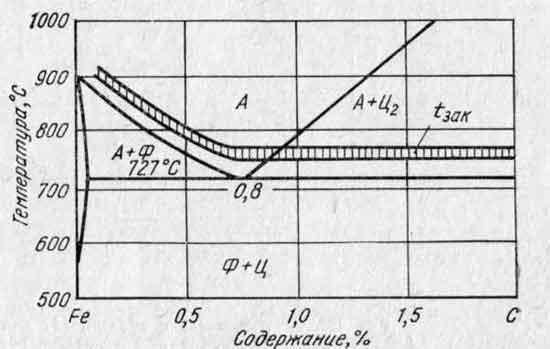
Dementsprechend werden für jede Stahlsorte oder Legierung individuelle Härtungsmodi entwickelt, die sich unterscheiden:
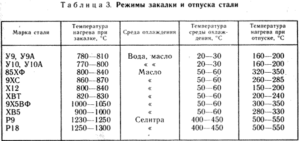
Das Härten von Stählen und Legierungen mit einer komplexen Zusammensetzung, einschließlich mehrerer Legierungselemente (insbesondere Kobalt, Molybdän), wird besonders sorgfältig durchgeführt. Diese Metalle bilden dabei intermetallische Verbindungen entlang der Korngrenzen der Hauptstruktur, die die Härte und Festigkeit von Stählen (insbesondere Werkzeugstahl) erheblich erhöhen. Die Form und Konzentration intermetallischer Verbindungen hängt nur von der Genauigkeit der Einhaltung der Abschrecktechnologie ab.
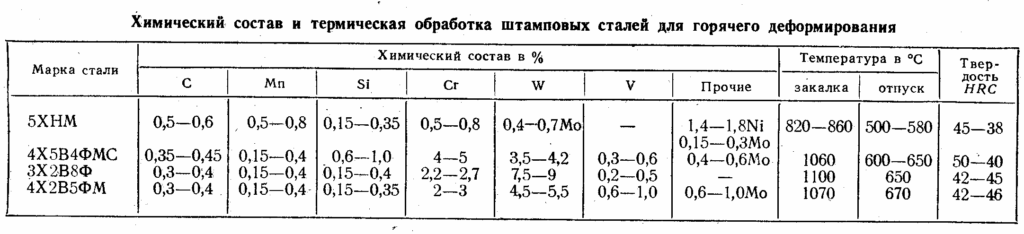
Die Arten der Härtung werden durch die Ausrüstung bestimmt, an der sie durchgeführt wird. Beispielsweise wird für Produkte wie Zahnräder, Wellen, Führungssäulen, bei denen eine optimale Kombination aus hoher Oberflächenhärte und einem relativ viskosen Kern erforderlich ist, eine Oberflächenhärtung durch hochfrequente Ströme verwendet.
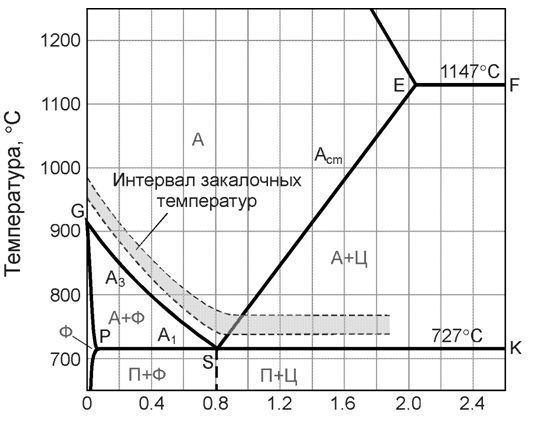
Dazu wird das Produkt in eine Induktionsspule gelegt, durch die ein hochfrequenter (bis zu 15000 ... 25000 Hz) Strom geleitet wird. Dieser Strom dringt bis zu einer begrenzten Tiefe ein und erhöht die Oberflächenfestigkeit von Stählen oder Legierungen. Infolgedessen nimmt die Dauerfestigkeit von Teilen, die unter zyklisch variierenden Zugdruckspannungen arbeiten, deutlich zu.
Eine intensivere Änderung der Härte der Oberfläche des Teils kann unter Verwendung energiereicher Wärmequellen - Funken- oder Lichtbogenentladung - zum Härten erzielt werden. Entladungen müssen in einem flüssigen Medium angeregt werden, in dem sich das Werkstück oder Werkstück befindet.
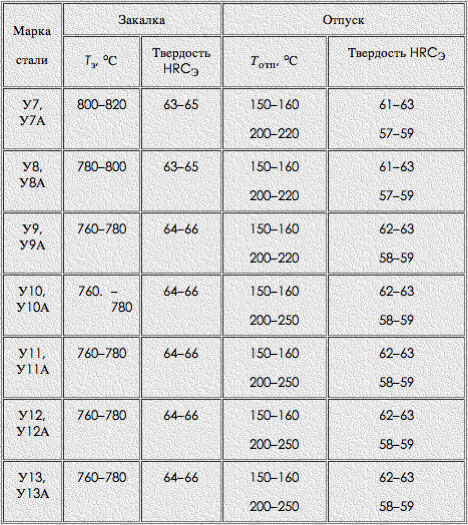
Nach dem Aushärten ist in den allermeisten Fällen ein Anlassen erforderlich, da sonst die übermäßige Endhärte des Teils unter Stoßbelastung zu einer erhöhten Sprödigkeit führt.
Verbesserung und Normalisierung
Als Wärmebehandlungsarten ähneln diese Prozesse dem Glühen, obwohl sie für andere Zwecke vorgesehen sind - um die Betriebsdauer kritischer Teile von Maschinen und Werkzeugen zu erhöhen.
Während der Normalisierung wird das Teil langsam erhitzt und auf einer bestimmten Temperatur gehalten, wonach es notwendigerweise mit dem Ofen gekühlt wird. Infolgedessen wird die Struktur des Teils ausgeglichener und das Niveau der inneren Spannungen nimmt ab.
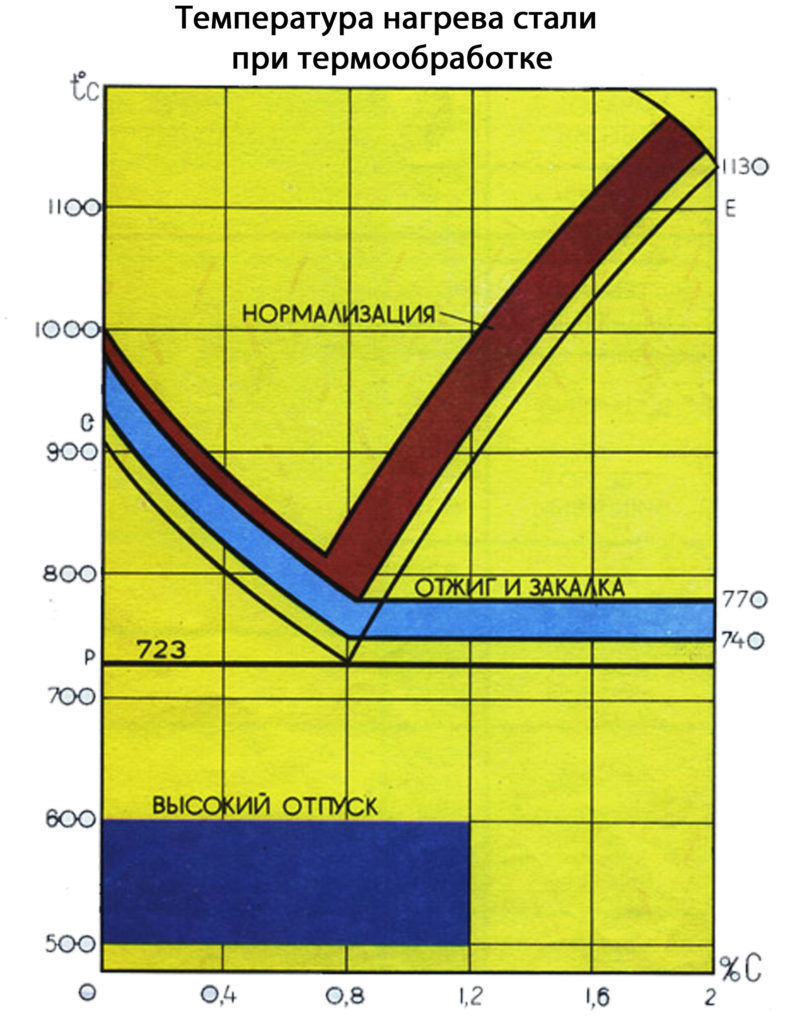
Ein wesentlicher Unterschied ist die Zusammensetzung der Atmosphäre, des Ofens, in dem diese Wärmebehandlungsvorgänge durchgeführt werden. Es sollte nicht oxidierend sein, da eine intensive Oxidation auf der Oberfläche des Produkts nicht nur seine Präsentation verschlechtert, sondern auch seine Größe ändert. Das Ausbrennen von Kohlenstoff, das auch mit der Wärmebehandlung in einem herkömmlichen Ofen einhergeht, verschlechtert die chemische Zusammensetzung von Stahl und verringert seine Festigkeit.
Die Verringerung des Sauerstoffzugangs zur Oberfläche des Teils während der Normalisierung wird auf verschiedene Arten durchgeführt:
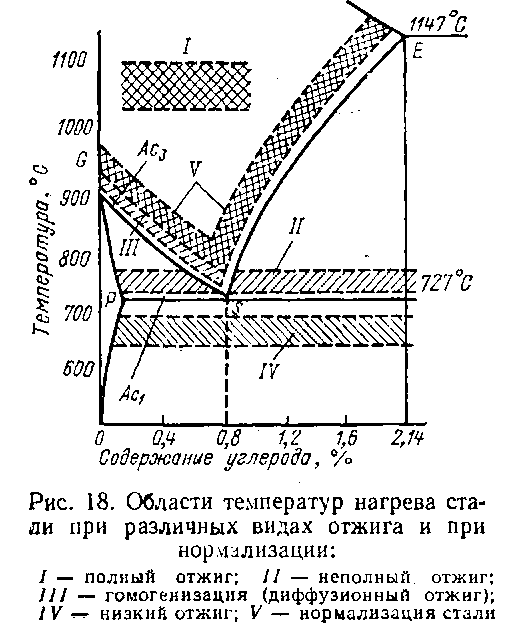
- Beheizt mit einem geplanten Sauerstoffmangel. In diesem Fall wird die Stabilität der Gasbrenner von Wärmebehandlungsöfen durch eine Erhöhung der Luftzufuhrrate zur Verbrennungszone kompensiert;
- Wärmebehandlung in einer Schutzgasumgebung. Für kritische Teile werden Lithiumdampf, Argon oder andere Edelgase verwendet, in anderen Fällen Kohlendioxid;
- Durch Aufbringen von Schutzbeschichtungen auf die Oberfläche des zu normalisierenden Produkts.
Nach der Normalisierung wird das Teil in ruhiger Luft abgekühlt, um ein Ausblasen zu verhindern. Dies kann zu einer heterogenen „fleckigen“ Mikrostruktur des Produkts führen.
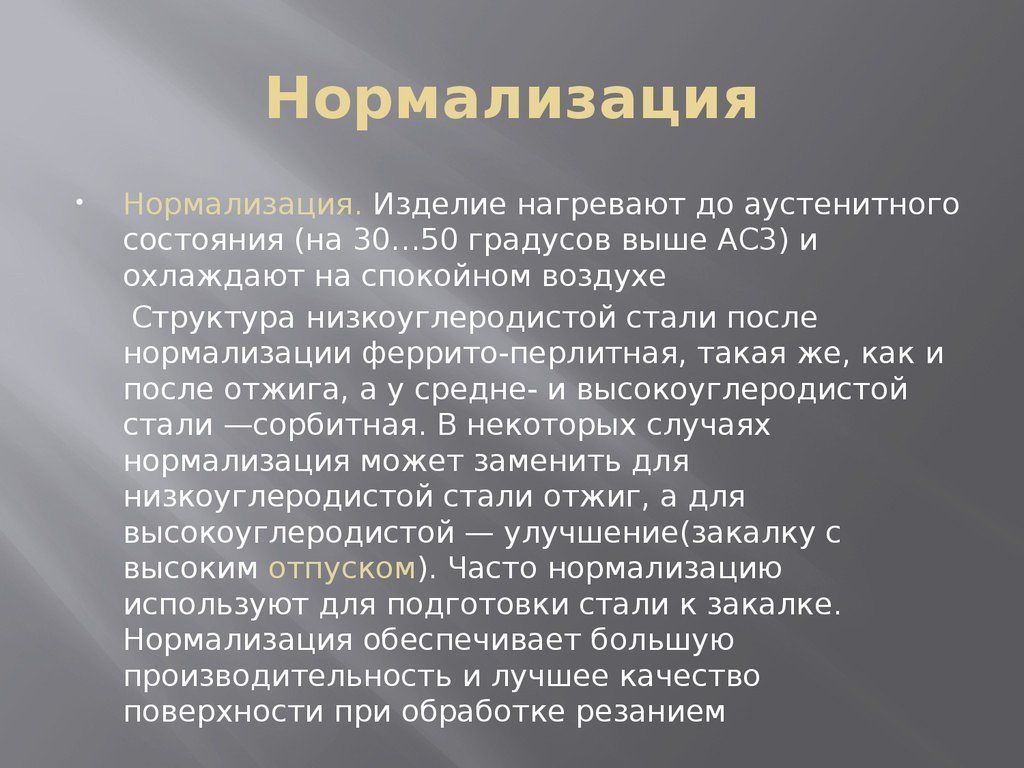
Die Verbesserung ist ein Wärmebehandlungsvorgang, bei dem die Bearbeitbarkeit von Stählen und Legierungen zunimmt und die Restspannungen in ihnen abnehmen. Dies geht mit einer gewissen Abnahme der Härte einher.
Die martensitische Komponente in der Struktur der meisten Stähle und Legierungen kann nicht nur bei erhöhten, sondern auch bei niedrigen Temperaturen auftreten. Die Kältebehandlungstechnologie ist im Vergleich zu herkömmlichen Wärmebehandlungstechnologien im Folgenden günstig:
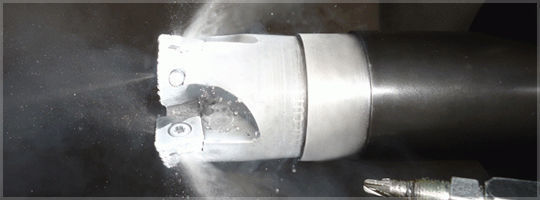
Kryogene Behandlungsschemata hängen von der Qualität der Stähle / Legierungen ab und schwanken im Bereich von -60 ... -140 0 С. Typischerweise wird die kryogene Behandlung mit einer zyklischen Kombination von Tiefkühlperioden mit Alterungsperioden durchgeführt - Halten bei niedrigeren Temperaturen. Durch eine Kombination von Heiz- und Kühlzyklen wird eine vollständige Zersetzung des Restaustenits in 4 ... 7 Stunden erreicht (große Werte - für hochlegierte Stähle).
Eine besondere Art der Wärmebehandlung sind die chemisch-thermischen Verfahren. Ihre Aufgabe ist es, Carbide und Nitride in der Oberflächenmikrostruktur zu bilden - Verbindungen, die die Mikrohärte von Teilen erheblich erhöhen und in ihnen Druckeigenspannungen erzeugen. Solche Produkte weisen eine besonders hohe Beständigkeit gegen Wechselbelastungen auf.
Video: Wie man eine Stahlsorte härtet
Autonome Einrichtung der NPO-Berufsschule Nr. 22 der Tschechischen Republik
Zusammenfassung
zum Thema " Materialwissenschaft »
zum Thema: " Wärmebehandlung von Metallen und Legierungen »
Hergestellt von:
schüler der Gruppe "DSM-01-11"
Morozov I.V.
Überprüft: Lehrer
Grigoreva E.V.
kanash 2011
Inhalt
Einleitung ………………………………………………………….
Zweck und Art der Wärmebehandlung .. …………………………………….… 4–9 Seiten
Zweck und Art der chemisch-thermischen Behandlung .............................. 10-15 SeitenWärmebehandlung von Nichteisenmetalllegierungen .............................. 15-18 Seiten
Schlussfolgerung ……………………………………………………………………………………………………………………………… ..19
Literatur ............................................................................
Einführung
Die Wärmebehandlung wird in verschiedenen Phasen der Herstellung von Maschinenteilen und Metallprodukten eingesetzt. In einigen Fällen kann es sich um einen Zwischenvorgang handeln, der dazu dient, die Bearbeitbarkeit von Legierungen durch Druck und Schneiden zu verbessern, in anderen Fällen ist es der Endvorgang, der die erforderlichen Indikatoren für die mechanischen, physikalischen und betrieblichen Eigenschaften von Produkten oder Halbzeugen liefert. Halbzeuge werden einer Wärmebehandlung unterzogen, um die Struktur zu verbessern, die Härte zu verringern (die Verarbeitbarkeit zu verbessern), und die Details werden verwendet, um ihnen spezifische, erforderliche Eigenschaften (Härte, Verschleißfestigkeit, Festigkeit und andere) zu verleihen.
Durch die Wärmebehandlung können die Eigenschaften von Legierungen über einen weiten Bereich verändert werden. Die Möglichkeit einer signifikanten Erhöhung der mechanischen Eigenschaften nach der Wärmebehandlung im Vergleich zum Ausgangszustand ermöglicht es, die zulässigen Spannungen zu erhöhen, die Größe und das Gewicht von Maschinen und Mechanismen zu verringern und die Zuverlässigkeit und Lebensdauer der Produkte zu erhöhen. Die Verbesserung der Eigenschaften infolge der Wärmebehandlung ermöglicht die Verwendung von Legierungen mit einfacheren Zusammensetzungen und daher billiger. Legierungen erwerben auch einige neue Eigenschaften, in deren Zusammenhang der Anwendungsbereich erweitert wird.
Zweck und Art der Wärmebehandlung
Die thermische (Wärme-) Verarbeitung wird als Prozesse bezeichnet, deren Kern darin besteht, Produkte in bestimmten Modi zu erhitzen und zu kühlen, was zu Änderungen der Struktur, der Phasenzusammensetzung sowie der mechanischen und physikalischen Eigenschaften des Materials führt, ohne die chemische Zusammensetzung zu ändern.
Der Zweck der Wärmebehandlung von Metallen besteht darin, die erforderliche Härte zu erhalten und die Festigkeitseigenschaften von Metallen und Legierungen zu verbessern. Die Wärmebehandlung ist in thermische, thermomechanische und chemisch-thermische unterteilt. Wärmebehandlung - nur thermische Exposition, thermomechanisch - eine Kombination aus thermischer Exposition und plastischer Verformung, chemisch-thermisch - eine Kombination aus thermischen und chemischen Effekten. Die Wärmebehandlung wird in Abhängigkeit von dem strukturellen Zustand, der als Ergebnis ihrer Anwendung erhalten wird, in Tempern (erste und zweite Art), Abschrecken und Anlassen unterteilt.
Glühen
Glühen - Wärmebehandlung, die darin besteht, das Metall auf bestimmte Temperaturen zu erhitzen, zu halten und anschließend mit dem Ofen sehr langsam abzukühlen. Es wird verwendet, um die Verarbeitung von Metallen durch Schneiden zu verbessern, die Härte zu verringern, eine körnige Struktur zu erhalten und um Spannungen abzubauen, alle Arten von Inhomogenitäten, die während früherer Vorgänge (Bearbeitung, Druckbehandlung, Gießen, Schweißen) in das Metall eingeführt wurden, teilweise oder vollständig zu beseitigen. verbessert die Struktur von Stahl.
Glühen der ersten Art. Dies ist ein Tempern, bei dem keine Phasentransformationen auftreten, und wenn sie stattfinden, haben sie keinen Einfluss auf die Endergebnisse, die durch den beabsichtigten Zweck bereitgestellt werden. Die folgenden Arten des Temperns der ersten Art werden unterschieden: Homogenisierung und Rekristallisation.
Die Homogenisierung wird bei längerer Exposition bei Temperaturen über 950 ° C (normalerweise 1100–1200 ° C) getempert, um die chemische Zusammensetzung auszugleichen.
Rekristallisation ist das Tempern von genietetem Stahl bei einer Temperatur, die die Temperatur des Beginns der Rekristallisation überschreitet, um das Aushärten zu vermeiden und eine bestimmte Korngröße zu erhalten.
Glühen der zweiten Art. Dies ist Tempern, in dem Phasenumwandlungen es bestimmen zweck. Folgende Typen werden unterschieden: vollständig, unvollständig, diffusionsbedingt, isotherm, leicht, normalisiert (Normalisierung), sphäroidisierend (für körniges Perlit).
Zum vollständigen Glühen wird Stahl 30–50 ° C über einen kritischen Punkt erhitzt, bei dieser Temperatur gehalten und langsam auf 400–500 ° C mit einer Geschwindigkeit von 200 ° C pro Stunde für Kohlenstoffstähle, 100 ° C pro Stunde für niedriglegierte Stähle und 50 ° C abgekühlt C pro Stunde für hochlegierte Stähle. Die Struktur des Stahls nach dem Tempern ist ausgeglichen, stabil.
Unvollständiges Glühen wird durchgeführt, indem Stahl auf eine der Temperaturen im Bereich von Umwandlungen, Halten und langsamer Abkühlung erhitzt wird. Unvollständiges Glühen wird verwendet, um innere Spannungen zu reduzieren, die Härte zu verringern und die Bearbeitbarkeit durch Schneiden zu verbessern.
Diffusionsglühen. Das Metall wird auf Temperaturen von 1100–1200 ° C erhitzt, da die Diffusionsprozesse, die zum Ausgleich der chemischen Zusammensetzung erforderlich sind, vollständiger ablaufen.
Das isotherme Glühen ist wie folgt: Der Stahl wird erhitzt und dann schnell abgekühlt (häufig durch Überführung in einen anderen Ofen) auf eine Temperatur unterhalb der kritischen Temperatur von 50–100 ° C. Es wird hauptsächlich für legierte Stähle verwendet. Es ist wirtschaftlich rentabel, da die Dauer des herkömmlichen Glühens (13 - 15) h und des isothermen Glühens (4 - 6) h beträgt
Das kugelförmige Glühen (für körniges Perlit) besteht darin, den Stahl über die kritische Temperatur um 20 - 30 ° C zu erhitzen, bei dieser Temperatur zu halten und langsam abzukühlen.
Das leichte Tempern wird gemäß dem Regime des vollständigen oder unvollständigen Temperns unter Verwendung von Schutzatmosphären von Schlamm in Öfen mit Teilvakuum durchgeführt. Es wird verwendet, um die Metalloberfläche vor Oxidation und Entkohlung zu schützen.
Normalisierung - besteht darin, das Metall auf eine Temperatur von (30-50) ° C über dem kritischen Punkt zu erhitzen und anschließend an der Luft abzukühlen. Der Zweck der Normalisierung ist je nach Zusammensetzung des Stahls unterschiedlich. Anstelle des Glühens werden kohlenstoffarme Stähle normalisiert. Bei Stählen mit mittlerem Kohlenstoffgehalt wird anstelle von Härten und Hochtemperieren eine Normalisierung verwendet. Stähle mit hohem Kohlenstoffgehalt werden einer Normalisierung unterzogen, um das zementartige Netz zu entfernen. Zur Fixierung der Struktur von legierten Stählen wird anstelle des Glühens eine Normalisierung gefolgt von einem hohen Tempern verwendet. Normalisierung im Vergleich zum Tempern ist ein wirtschaftlicherer Vorgang, da keine Kühlung mit dem Ofen erforderlich ist.
Abschrecken
Beim Abschrecken wird auf die optimale Temperatur erhitzt, gehalten und anschließend schnell abgekühlt, um eine Nichtgleichgewichtsstruktur zu erhalten.
Durch das Aushärten werden Festigkeit und Härte erhöht und die Duktilität von Stahl verringert. Die Hauptparameter beim Aushärten sind die Heiztemperatur und die Abkühlrate. Die kritische Abschreckrate wird als Abkühlrate bezeichnet, die eine Struktur liefert - Martensit oder Martensit und Restaustenit.
Abhängig von der Form des Teils, der Stahlsorte und den erforderlichen Eigenschaften werden verschiedene Abschreckmethoden angewendet.
Aushärten in einem Kühler. Das Teil wird auf eine Härtungstemperatur erhitzt und in einem Kühler (Wasser, Öl) gekühlt.
Das Abschrecken in zwei Umgebungen (intermittierendes Abschrecken) ist das Abschrecken, bei dem ein Teil in zwei Umgebungen nacheinander gekühlt wird: Das erste Medium ist Kühlflüssigkeit (Wasser), das zweite ist Luft oder Öl.
Stufenhärten. Das auf die Abschrecktemperatur erhitzte Teil wird in geschmolzenen Salzen abgekühlt, nachdem es für die Zeit gehalten wurde, die erforderlich ist, um die Temperatur über den gesamten Querschnitt auszugleichen, wird das Teil an Luft abgekühlt, was zur Verringerung der Abschreckspannungen beiträgt.
Das isotherme Härten sowie das Stufenhärten werden in zwei Kühlmedien durchgeführt. Die Temperatur des heißen Mediums (Salz-, Salpeter- oder Alkalibäder) ist unterschiedlich: Sie hängt von der chemischen Zusammensetzung des Stahls ab, liegt jedoch immer 20–100 ° C über dem Punkt der martensitischen Umwandlung für diesen Stahl. Die endgültige Abkühlung auf Raumtemperatur erfolgt an Luft. Die isotherme Härtung wird häufig für Teile hochlegierter Stähle eingesetzt. Nach dem isothermen Härten erhält der Stahl hochfeste Eigenschaften, dh eine Kombination aus hoher Viskosität und Festigkeit.
Selbsttemperieren ist in der Werkzeugherstellung weit verbreitet. Der Prozess besteht darin, dass die Teile nicht im Kühlmedium gehalten werden, bis sie vollständig abgekühlt sind, sondern zu einem bestimmten Zeitpunkt aus diesem entfernt werden, um eine bestimmte Wärmemenge im Kern des Teils zu erhalten, wodurch ein anschließendes Tempern durchgeführt wird.
Urlaub
Das Tempern von Stahl ist der letzte Vorgang der Wärmebehandlung, der die Struktur und folglich die Eigenschaften von Stahl bildet. Das Tempern besteht darin, den Stahl auf verschiedene Temperaturen zu erhitzen (abhängig von der Art des Temperierens, aber immer unter dem kritischen Punkt), bei dieser Temperatur zu halten und mit unterschiedlichen Geschwindigkeiten abzukühlen. Der Zweck des Anlassens besteht darin, innere Spannungen, die während des Härtungsprozesses entstehen, abzubauen und die erforderliche Struktur zu erhalten.
Je nach Erwärmungstemperatur des gehärteten Teils werden drei Arten des Anlassens unterschieden: hoch, mittel und niedrig.
Das Hochtemperieren wird bei Erwärmungstemperaturen über 350-600 ° C, jedoch unterhalb des kritischen Punktes durchgeführt; Dieses Anlassen wird auf Baustähle angewendet.
Das durchschnittliche Tempern wird bei Erwärmungstemperaturen von 350 - 500 ° C durchgeführt; Dieses Anlassen wird häufig für Federn und Federstähle verwendet.
Niedriges Tempern wird bei Temperaturen von 150–250 ° C durchgeführt. Die Härte des Teils nach dem Aushärten bleibt nahezu unverändert; Niedrigtemperieren wird für Werkzeugstähle aus Kohlenstoff und Legierungen verwendet, die eine hohe Härte und Verschleißfestigkeit erfordern.
Die Urlaubskontrolle wird gemäß den Farbtönen durchgeführt, die auf der Oberfläche des Teils erscheinen.
Altern
Beim Altern werden die Eigenschaften von Legierungen geändert, ohne dass sich die Mikrostruktur merklich ändert. Es sind zwei Arten der Alterung bekannt: thermische und Verformung.
Die thermische Alterung erfolgt aufgrund von Änderungen der Löslichkeit von Kohlenstoff in Eisen in Abhängigkeit von der Temperatur.
Wenn bei Raumtemperatur eine Änderung der Härte, Duktilität und Festigkeit auftritt, wird eine solche Alterung als natürlich bezeichnet.
Wenn der Prozess bei erhöhter Temperatur abläuft, wird Alterung als künstlich bezeichnet.
Dehnungsalterung (mechanisch) tritt nach kalter plastischer Verformung auf.
Kaltumformung
Eine neue Art der Wärmebehandlung zur Erhöhung der Härte von Stahl durch Umwandlung von Restaustenit aus gehärtetem Stahl in Martensit. Dies erfolgt durch Abkühlen des Stahls auf die Temperatur des unteren martensitischen Punktes.
Oberflächenhärtungsmethoden
Oberflächenhärtung bezieht sich auf den Wärmebehandlungsprozess, bei dem die Oberflächenschicht aus Stahl auf eine höhere Temperatur als kritisch erwärmt und anschließend abgekühlt wird, um Martensitstrukturen in der Oberflächenschicht zu erhalten.
Folgende Typen werden unterschieden: Induktionshärten; Abschrecken im Elektrolyten, Abschrecken während des Erhitzens durch Hochfrequenzströme (HDTV), Abschrecken mit Gasflammenerwärmung.
Die Induktionshärtung basiert auf einem physikalischen Phänomen, dessen Kern darin besteht, dass ein hochfrequenter elektrischer Strom, der durch einen Leiter fließt, ein elektromagnetisches Feld um ihn herum erzeugt. Auf der Oberfläche des in diesem Feld befindlichen Teils werden Wirbelströme induziert, wodurch sich das Metall auf hohe Temperaturen erwärmt. Dies bietet die Möglichkeit von Phasentransformationen.
Je nach Heizmethode wird die Induktionshärtung in drei Typen unterteilt:
gleichzeitiges Erhitzen und Aushärten der gesamten Oberfläche (für kleine Teile);
sequentielles Erhitzen und Härten einzelner Abschnitte (für Kurbelwellen und ähnliche Teile);
kontinuierliches Erhitzen und Abschrecken durch Bewegen (für lange Teile).
Gasflammenhärten. Der Gasflammenhärtungsprozess besteht darin, die Oberfläche des Teils schnell mit einer Acetylen-Sauerstoff-, Gas-Sauerstoff- oder Sauerstoff-Kerosin-Flamme auf eine Härtungstemperatur zu erwärmen, gefolgt von Abkühlen mit Wasser oder einer Emulsion.
Aushärten in einem Elektrolyten. Das Abschrecken in einem Elektrolyten erfolgt wie folgt: Ein abgeschreckter Teil wird mit einem Elektrolyten (5–10% ige Lösung von kalziniertem Salz) in ein Bad abgesenkt und ein Strom von 220–250 V wird geleitet. Dadurch wird der Teil auf hohe Temperaturen erhitzt. Die Teile werden entweder im gleichen Elektrolyten (nach Abschalten des Stroms) oder in einem speziellen Abschrecktank gekühlt.
Thermomechanische Behandlung
Die thermomechanische Verarbeitung (T.M.O.) ist eine neue Methode zum Härten von Metallen und Legierungen unter Beibehaltung einer ausreichenden Duktilität, bei der plastische Verformung und Härtewärmebehandlung (Härten und Anlassen) kombiniert werden. Es gibt drei Hauptmethoden der thermomechanischen Verarbeitung.
Die thermomechanische Behandlung bei niedriger Temperatur (N.TM.O.) basiert auf einer Stufenhärtung, d. H. Eine plastische Verformung von Stahl wird bei Temperaturen der relativen Stabilität von Austenit mit anschließendem Härten und Anlassen durchgeführt.
Eine thermomechanische Hochtemperaturbehandlung (V.T.M.O.) mit dieser plastischen Verformung wird bei Austenitstabilitätstemperaturen mit anschließendem Abschrecken und Tempern durchgeführt.
Die Verformung der vorläufigen thermomechanischen Behandlung (P.T.M.O.) kann bei den Temperaturen von N.T.M.O. und V.T.M.O. oder bei einer Temperatur von 20 ° C durchgeführt werden. Als nächstes wird die übliche Wärmebehandlung durchgeführt: Härten und Anlassen.
Zweck und Art der chemisch-thermischen Behandlung
Die chemisch-thermische Behandlung bezieht sich auf einen Prozess, der eine Kombination aus thermischer und chemischer Exposition darstellt, um die Zusammensetzung, Struktur und Eigenschaften der Oberflächenschicht aus Stahl zu ändern.
Der Zweck der chemisch-thermischen Behandlung: Erhöhung der Oberflächenhärte, Verschleißfestigkeit, Dauerfestigkeit, Korrosionsbeständigkeit, Wärmebeständigkeit (Ablagerungsbeständigkeit), Säurebeständigkeit.
Die in der Industrie am häufigsten verwendeten Arten der chemisch-thermischen Behandlung sind: Zementierung; Nitrocarburieren; Nitrieren; Cyanidierung; Diffusionsmetallisierung.
Das Zementieren ist ein Prozess der Oberflächensättigung mit Kohlenstoff, der mit dem Ziel der Oberflächenhärtung von Teilen durchgeführt wird.
Je nach verwendetem Aufkohler wird die Zementierung in drei Arten unterteilt: Zementierung durch einen festen Aufkohler; Gaszementierung (Methan, Propan, Erdgas).
Gaszementierung. Die Teile werden in speziellen hermetisch abgeschlossenen Öfen auf 900–950 ° C erhitzt, in die zementhaltiges kohlenstoffhaltiges Gas [natürlich (natürlich) oder künstlich] in einem kontinuierlichen Strom eingespeist wird.
Der Zementierungsprozess in einem Festvergaser ist wie folgt. Teile, die in einer Schachtel mit einem Aufkohler (einer Mischung aus Holzkohle und Aktivator) verpackt sind, werden auf eine bestimmte Temperatur erhitzt und lange auf dieser Temperatur gehalten, dann abgekühlt und einer Wärmebehandlung unterzogen.
Die Zementierung unter Verwendung eines der obigen Verfahren wird für Teile aus Kohlenstoff und legiertem Stahl mit einem Kohlenstoffgehalt von nicht mehr als 0,2% verwendet. Das Zementieren von legierten Stählen, die karbidbildende Elemente Cr, W, V enthalten, liefert besonders gute Ergebnisse: Neben der Erhöhung der Oberflächenhärte und der Verschleißfestigkeit erhöhen sie auch die Ermüdungsgrenze.
Nitrieren ist der Prozess der Sättigung der Oberflächenschicht verschiedener Metalle und Legierungen, Stahlprodukte oder Teile mit Stickstoff, wenn sie in einer geeigneten Umgebung erhitzt werden. Die Oberflächenhärte des Produkts, die Lebensdauer, die Verschleißfestigkeit und die Korrosionsbeständigkeit nehmen zu.
Cyanidierung ist die Sättigung der Oberflächenschicht von Produkten gleichzeitig mit Kohlenstoff und Stickstoff.
Je nach verwendetem Medium wird die Cyanidierung unterschieden: in festen Medien; in flüssigen Medien; in gasförmigen Medien.
Je nach Heiztemperatur wird die Cyanidierung in Niedertemperatur und Hochtemperatur unterteilt.
Die Cyanidierung in flüssigen Medien erfolgt in Bädern mit geschmolzenen Salzen.
Cyanid in gasförmigen Medien (Nitrocarburieren). Der Prozess der gleichzeitigen Sättigung der Oberfläche eines Teils mit Kohlenstoff und Stickstoff. Zu diesem Zweck werden die Teile in einer Umgebung erhitzt, die aus Zementiergas und Ammoniak besteht, dh das Nitrocarburieren kombiniert Gaszementierungs- und Nitrierprozesse.
Diffusionssättigung mit Metallen und Metalloiden
Es gibt und werden in der Industrie Verfahren zum Sättigen der Oberfläche von Teilen mit verschiedenen Metallen (Aluminium, Chrom usw.) und Metalloiden (Silizium, Bor usw.) angewendet. Der Zweck dieser Sättigung besteht darin, die Ablagerungsbeständigkeit, Korrosionsbeständigkeit, Säurebeständigkeit, Härte und Verschleißfestigkeit von Teilen zu erhöhen. Dadurch erhält die Oberflächenschicht spezielle Eigenschaften, mit denen Legierungselemente eingespart werden können.
Die Alifizierung ist der Prozess der Sättigung der Oberflächenschicht aus Stahl mit Aluminium, um die Wärmebeständigkeit (Ablagerungsbeständigkeit) und die Beständigkeit gegen atmosphärische Korrosion zu erhöhen.
Die Alifizierung erfolgt in Pulvermischungen, in Bädern mit geschmolzenem Aluminium, in einer gasförmigen Umgebung und durch Sprühen von flüssigem Aluminium.
Beim Verchromen wird die Oberflächenschicht aus Stahl mit Chrom gesättigt, um die Korrosions- und Wärmebeständigkeit zu erhöhen, und beim Verchromen von Stählen mit hohem Kohlenstoffgehalt die Härte und Verschleißfestigkeit erhöht.
Die Siliziumisierung ist der Prozess der Sättigung der Oberflächenschicht eines Teils mit Silizium, um die Korrosionsbeständigkeit und Säurebeständigkeit zu erhöhen. Teile aus kohlenstoffarmen und mittelkohlenstoffhaltigen Stählen sowie aus formbaren und duktilen Gusseisen werden einer Siliziumisierung unterzogen.
Borierung ist der Prozess der Sättigung der Oberflächenschicht eines Teils mit Bor. Der Zweck der Borierung besteht darin, die Härte, die Beständigkeit gegen Abrieb und Korrosion in aggressiven Umgebungen, die Wärmebeständigkeit und die Wärmebeständigkeit von Stahlteilen zu erhöhen. Es gibt zwei Methoden der Borierung: Flüssigelektrolyse und Gasborierung.
Bei der Sulfidierung wird die Oberflächenschicht von Stahlteilen mit Schwefel gesättigt, um die Eigenschaften des extremen Drucks zu verbessern und die Verschleißfestigkeit der Teile zu erhöhen.
Die Sulfocyanierung ist der Prozess der Oberflächensättigung von Stahlteilen mit Schwefel, Kohlenstoff und Stickstoff. Die kombinierte Wirkung von Schwefel und Stickstoff in der Oberflächenschicht des Metalls bietet höhere Extremdruckeigenschaften und Verschleißfestigkeit im Vergleich zur Sättigung nur mit Schwefel.
Wärmebehandlung aus Gusseisen
Die Wärmebehandlung von Gusseisen wird durchgeführt, um innere Spannungen, die während des Gießens auftreten, abzubauen und Änderungen der Größe und Form des Gusses im Laufe der Zeit zu verursachen, die Härte zu verringern und die Bearbeitbarkeit durch Schneiden zu verbessern und die mechanischen Eigenschaften zu verbessern. Gusseisen wird geglüht, normalisiert, gehärtet und angelassen sowie bestimmten chemisch-thermischen Behandlungen (Nitrieren, Aluminieren, Verchromen) unterzogen.
Glühen zur Entlastung innerer Spannungen. Gusseisen wird bei den folgenden Temperaturen geglüht: Grauguss mit Lamellengraphit 500-570 ° C; hochfestes Gusseisen mit kugelförmigem Graphit 550 - 650 ° C; niedriglegiertes Gusseisen 570 - 600 ° C; hochlegiertes Gusseisen 620 - 650 ° C. Während dieses Temperns treten keine Phasenumwandlungen auf, aber innere Spannungen werden entfernt, Viskositätserhöhungen, Verformungen und Risse während des Betriebs werden ausgeschlossen.
Erweichungsglühen (Niedertemperatur-Graphitglühen). Durchgeführt, um die Bearbeitbarkeit durch Schneiden zu verbessern und die Duktilität zu erhöhen. Es wird durch längere Exposition bei 680 - 700 ° C oder durch langsames Abkühlen der Gussteile bei 760 - 700 ° C durchgeführt. Bei Teilen mit komplexer Konfiguration ist die Abkühlung langsam und bei Teilen mit einfacher Form beschleunigt.
Graphitierglühen, wodurch duktiles Eisen aus weißem Gusseisen gewonnen wird.
Die Normalisierung wird verwendet, um den gebundenen Kohlenstoff zu erhöhen, die Härte, Festigkeit und Verschleißfestigkeit von grauem, formbarem und duktilem Eisen zu erhöhen. Während der Normalisierung wird Gusseisen (Gussteile) über die Temperaturen des Umwandlungsintervalls von 850–950 ° C erhitzt und nach dem Aussetzen an der Luft abgekühlt.
Graues, formbares und duktiles Gusseisen wird gehärtet, um die Härte, Festigkeit und Verschleißfestigkeit zu erhöhen. Gemäß der Ausführungsmethode kann das Härten von Gusseisen kontinuierlich volumetrisch, isotherm und oberflächenbezogen sein.
Während des kontinuierlichen kontinuierlichen Härtens wird Gusseisen auf eine Temperatur von 850 bis 950 ° C erhitzt. Dann zum Erhitzen und vollständigen Auflösen von Kohlenstoff stehen. Die Kühlung erfolgt in Wasser oder Öl. Nach dem Abschrecken wird ein Urlaub bei einer Temperatur von 200 - 600 ° C durchgeführt. Das Ergebnis ist eine erhöhte Härte, Festigkeit und Verschleißfestigkeit von Gusseisen.
Beim isothermen Härten werden Gusseisen auf die gleiche Weise wie beim kontinuierlichen Härten erhitzt, 10 bis 90 Minuten gehalten und in geschmolzenem Salz auf 200 bis 400 ° C abgekühlt und nach dem Aussetzen an der Luft abgekühlt.
Oberflächenhärtung durch Erhitzen der Oberflächenschicht mit einer Sauerstoff-Acetylen-Flamme, Hochfrequenzströmen oder in einem Elektrolyten. Heiztemperatur 900 - 1000 ° C. Abkühlen in Wasser, Öl oder Ölemulsion.
Das Altern wird verwendet, um die Größe von Gusseisenteilen zu stabilisieren, Verwerfungen zu verhindern und innere Spannungen abzubauen. In der Regel erfolgt die Alterung nach der Grobbearbeitung. Es gibt zwei Arten des Alterns: natürliche und künstliche.
Die natürliche Alterung erfolgt im Freien oder in Innenräumen. Produkte nach dem Gießen werden 6 bis 15 Monate gealtert.
Künstliche Alterung tritt bei erhöhten Temperaturen auf; Dauer - einige Stunden. Während der künstlichen Alterung werden Eisengussteile in einen auf 100-200 ° C erhitzten Ofen geladen. C werden sie mit einer Geschwindigkeit von 30 bis 60 ° C pro Stunde auf eine Temperatur von 550 bis 570 ° C erhitzt, können 3 bis 5 Stunden standhalten und werden zusammen mit dem Ofen mit einer Geschwindigkeit von 20 bis 40 ° C pro Stunde auf eine Temperatur von 150 bis 200 ° C abgekühlt und dann abgekühlt in der Luft.
Chemische und Wärmebehandlung von Gusseisen
Um die Oberflächenhärte und die Verschleißfestigkeit zu erhöhen, werden Graugussteile einem Nitrieren unterzogen. Meistens nitrilgraues Perlitgusseisen, legiert mit Chrom, Molybdän, Aluminium. Nitriertemperatur 550 - 580 ° C, Haltezeit 30 - 70 Stunden. Zusätzlich zum Nitrieren kann bei einer Temperatur von 570 ° C eine Erhöhung der Oberflächenhärte und der Verschleißfestigkeit von legiertem grauem perlitischem Eisen, Gas und flüssiger Cyanidierung erreicht werden. Um die Wärmebeständigkeit zu erhöhen, können Gusseisengussteile alitisiert werden und um eine hohe Korrosionsbeständigkeit in Säuren zu erreichen, Verkieselung.
Wärmebehandlung von Nichteisenmetalllegierungen
Aluminiumlegierungen
Aluminiumlegierungen werden drei Arten von Wärmebehandlungen unterzogen: Glühen, Härten und Altern. Die Hauptglüharten sind: Diffusion, Rekristallisation und thermisch gehärtete Legierungen.
Die Homogenisierung wird verwendet, um die chemische Mikroinhomogenität der Körner der festen Lösung auszugleichen. Zur Durchführung der Homogenisierung werden Aluminiumlegierungen auf 450 bis 520ºC erhitzt und bei diesen Temperaturen von 4 bis 40 Stunden gehalten; nach dem Aussetzen - Abkühlen mit dem Ofen oder Luft. Infolgedessen wird die Struktur gleichmäßiger und die Duktilität nimmt zu.
Das Rekristallisationsglühen für Aluminium und seine Legierungen wird viel häufiger verwendet als für Stahl. Dies erklärt sich aus der Tatsache, dass Metalle wie Aluminium und Kupfer sowie viele darauf basierende Legierungen nicht durch Härten gehärtet werden und die Erhöhung der mechanischen Eigenschaften nur durch Kaltdruckbehandlung erreicht werden kann und das Rekristallisationsglühen ein Zwischenvorgang während einer solchen Verarbeitung ist. Die Temperatur des Rekristallisationsglühens von Aluminiumlegierungen beträgt 300 - 500 ° C, 0,5 bis 2 Stunden.
usw.................
zum Thema: „Wärmebehandlung von Metallen und Legierungen“
Einführung
Die Wärmebehandlung wird in verschiedenen Phasen der Herstellung von Maschinenteilen und Metallprodukten eingesetzt. In einigen Fällen kann es sich um einen Zwischenvorgang handeln, der dazu dient, die Bearbeitbarkeit von Legierungen durch Druck und Schneiden zu verbessern, in anderen Fällen ist es der Endvorgang, der die erforderlichen Indikatoren für die mechanischen, physikalischen und betrieblichen Eigenschaften von Produkten oder Halbzeugen liefert. Halbzeuge werden einer Wärmebehandlung unterzogen, um die Struktur zu verbessern, die Härte zu verringern (die Verarbeitbarkeit zu verbessern), und die Details werden verwendet, um ihnen spezifische, erforderliche Eigenschaften (Härte, Verschleißfestigkeit, Festigkeit und andere) zu verleihen.
Durch die Wärmebehandlung können die Eigenschaften von Legierungen über einen weiten Bereich verändert werden. Die Möglichkeit einer signifikanten Erhöhung der mechanischen Eigenschaften nach der Wärmebehandlung im Vergleich zum Ausgangszustand ermöglicht es, die zulässigen Spannungen zu erhöhen, die Größe und das Gewicht von Maschinen und Mechanismen zu verringern und die Zuverlässigkeit und Lebensdauer der Produkte zu erhöhen. Die Verbesserung der Eigenschaften infolge der Wärmebehandlung ermöglicht die Verwendung von Legierungen mit einfacheren Zusammensetzungen und daher billiger. Legierungen erwerben auch einige neue Eigenschaften, in deren Zusammenhang der Anwendungsbereich erweitert wird.
Zweck und Art der Wärmebehandlung
Die thermische (Wärme-) Verarbeitung wird als Prozesse bezeichnet, deren Kern darin besteht, Produkte in bestimmten Modi zu erhitzen und zu kühlen, was zu Änderungen der Struktur, der Phasenzusammensetzung sowie der mechanischen und physikalischen Eigenschaften des Materials führt, ohne die chemische Zusammensetzung zu ändern.
Der Zweck der Wärmebehandlung von Metallen besteht darin, die erforderliche Härte zu erhalten und die Festigkeitseigenschaften von Metallen und Legierungen zu verbessern. Die Wärmebehandlung ist in thermische, thermomechanische und chemisch-thermische unterteilt. Wärmebehandlung - nur thermische Exposition, thermomechanisch - eine Kombination aus thermischer Exposition und plastischer Verformung, chemisch-thermisch - eine Kombination aus thermischen und chemischen Effekten. Die Wärmebehandlung wird in Abhängigkeit von dem strukturellen Zustand, der als Ergebnis ihrer Anwendung erhalten wird, in Tempern (erste und zweite Art), Abschrecken und Anlassen unterteilt.
Glühen
Glühen - Wärmebehandlung, bestehend aus Erhitzen des Metalls auf bestimmte Temperaturen, Aussetzen und anschließendes sehr langsames Abkühlen mit dem Ofen. Es wird verwendet, um die Verarbeitung von Metallen durch Schneiden zu verbessern, die Härte zu verringern, eine körnige Struktur zu erhalten und um Spannungen abzubauen, alle Arten von Inhomogenitäten, die während früherer Vorgänge (Bearbeitung, Druckbehandlung, Gießen, Schweißen) in das Metall eingeführt wurden, teilweise oder vollständig zu beseitigen. verbessert die Struktur von Stahl.
Glühen der ersten Art . Dies ist ein Tempern, bei dem keine Phasentransformationen auftreten, und wenn sie stattfinden, haben sie keinen Einfluss auf die Endergebnisse, die durch den beabsichtigten Zweck bereitgestellt werden. Die folgenden Arten des Temperns der ersten Art werden unterschieden: Homogenisierung und Rekristallisation.
Homogenisierung - Dies ist ein Tempern mit langer Einwirkung bei Temperaturen über 950 ° C (normalerweise 1100–1200 ° C), um die chemische Zusammensetzung auszugleichen.
Rekristallisation - Dies ist das Tempern von genietetem Stahl bei einer Temperatur, die die Temperatur des Beginns der Rekristallisation überschreitet, um das Aushärten zu vermeiden und eine bestimmte Korngröße zu erhalten.
Glühen der zweiten Art . Dies ist ein Tempern, bei dem Phasentransformationen den Zweck bestimmen. Folgende Typen werden unterschieden: vollständig, unvollständig, diffusionsbedingt, isotherm, leicht, normalisiert (Normalisierung), sphäroidisierend (für körniges Perlit).
Volles Glühen hergestellt durch Erhitzen von Stahl 30–50 ° C über einen kritischen Punkt, Halten bei dieser Temperatur und langsames Abkühlen auf 400–500 ° C mit einer Geschwindigkeit von 200 ° C pro Stunde Kohlenstoffstähle, 100 ° C pro Stunde für niedriglegierte Stähle und 50 ° C. Stunde für hochlegierte Stähle. Die Struktur des Stahls nach dem Tempern ist ausgeglichen, stabil.
Unvollständiges Glühen Es wird durch Erhitzen von Stahl auf eine der Temperaturen im Bereich von Umwandlung, Belichtung und langsamer Abkühlung hergestellt. Unvollständiges Glühen wird verwendet, um innere Spannungen zu reduzieren, die Härte zu verringern und die Bearbeitbarkeit durch Schneiden zu verbessern.
Diffusionsglühen . Das Metall wird auf Temperaturen von 1100–1200 ° C erhitzt, da in diesem Fall Diffusionsprozesse, die zum Nivellieren der chemischen Zusammensetzung erforderlich sind, vollständiger ablaufen.
Isothermes Glühen besteht aus Folgendem: Stahl wird erhitzt und dann schnell (häufig durch Überführung in einen anderen Ofen) auf eine Temperatur abgekühlt, die um 50–100 ° C unter der kritischen Temperatur liegt. Es wird hauptsächlich für legierte Stähle verwendet. Es ist wirtschaftlich rentabel, da die Dauer des herkömmlichen Glühens (13 - 15) h und des isothermen Glühens (4 - 6) h beträgt
Sphäroidisches Glühen (für körniges Perlit) besteht darin, den Stahl über die kritische Temperatur um 20 - 30 ° C zu erhitzen, bei dieser Temperatur zu halten und langsam abzukühlen.
Leichtes Glühen Es wird gemäß den Modi des vollständigen oder unvollständigen Temperns unter Verwendung von Schutzatmosphären von Schlamm in Öfen mit Teilvakuum durchgeführt. Es wird verwendet, um die Metalloberfläche vor Oxidation und Entkohlung zu schützen.
Normalisierung - besteht darin, das Metall auf eine Temperatur von (30–50) ºС über dem kritischen Punkt zu erhitzen und anschließend an der Luft abzukühlen. Der Zweck der Normalisierung ist je nach Zusammensetzung des Stahls unterschiedlich. Anstelle des Glühens werden kohlenstoffarme Stähle normalisiert. Bei Stählen mit mittlerem Kohlenstoffgehalt wird anstelle von Härten und Hochtemperieren eine Normalisierung verwendet. Stähle mit hohem Kohlenstoffgehalt werden einer Normalisierung unterzogen, um das zementartige Netz zu entfernen. Zur Fixierung der Struktur von legierten Stählen wird anstelle des Glühens eine Normalisierung gefolgt von einem hohen Tempern verwendet. Normalisierung im Vergleich zum Tempern ist ein wirtschaftlicherer Vorgang, da keine Kühlung mit dem Ofen erforderlich ist.
Abschrecken
Abschrecken - Dies ist das Erhitzen auf die optimale Temperatur, Belichtung und anschließendes schnelles Abkühlen, um eine Nichtgleichgewichtsstruktur zu erhalten.
Durch das Aushärten werden Festigkeit und Härte erhöht und die Duktilität von Stahl verringert. Die Hauptparameter beim Aushärten sind die Heiztemperatur und die Abkühlrate. Die kritische Abschreckrate wird als Abkühlrate bezeichnet, die eine Struktur liefert - Martensit oder Martensit und Restaustenit.
Abhängig von der Form des Teils, der Stahlsorte und den erforderlichen Eigenschaften werden verschiedene Abschreckmethoden angewendet.
Abschrecken in einem Kühler . Das Teil wird auf eine Härtungstemperatur erhitzt und in einem Kühler (Wasser, Öl) gekühlt.
Härten in zwei Umgebungen (intermittierendes Härten) - Dies ist eine Härtung, bei der das Teil in zwei Umgebungen nacheinander gekühlt wird: Das erste Medium ist Kühlflüssigkeit (Wasser), das zweite ist Luft oder Öl.
Stufenhärten . Das auf die Abschrecktemperatur erhitzte Teil wird in geschmolzenen Salzen abgekühlt, nachdem es für die Zeit gehalten wurde, die erforderlich ist, um die Temperatur über den gesamten Querschnitt auszugleichen, wird das Teil an Luft abgekühlt, was zur Verringerung der Abschreckspannungen beiträgt.
Isotherme Härtung Neben Schritt wird es in zwei Kühlumgebungen hergestellt. Die Temperatur des heißen Mediums (Salz-, Salpeter- oder Alkalibäder) ist unterschiedlich: Sie hängt von der chemischen Zusammensetzung des Stahls ab, liegt jedoch immer 20–100 ° C über dem Punkt der martensitischen Umwandlung für diesen Stahl. Die endgültige Abkühlung auf Raumtemperatur erfolgt an Luft. Die isotherme Härtung wird häufig für Teile hochlegierter Stähle eingesetzt. Nach dem isothermen Härten erhält der Stahl hochfeste Eigenschaften, dh eine Kombination aus hoher Viskosität und Festigkeit.
Selbsttemperieren Es ist im Werkzeugbau weit verbreitet. Der Prozess besteht darin, dass die Teile nicht im Kühlmedium gehalten werden, bis sie vollständig abgekühlt sind, sondern zu einem bestimmten Zeitpunkt aus diesem entfernt werden, um eine bestimmte Wärmemenge im Kern des Teils zu erhalten, wodurch ein anschließendes Tempern durchgeführt wird.
Urlaub
Urlaub Stahl ist der letzte Vorgang der Wärmebehandlung, der die Struktur und folglich die Eigenschaften von Stahl bildet. Das Tempern besteht darin, den Stahl auf verschiedene Temperaturen zu erhitzen (abhängig von der Art des Temperierens, aber immer unter dem kritischen Punkt), bei dieser Temperatur zu halten und mit unterschiedlichen Geschwindigkeiten abzukühlen. Der Zweck des Anlassens besteht darin, innere Spannungen, die während des Härtungsprozesses entstehen, abzubauen und die erforderliche Struktur zu erhalten.
Je nach Erwärmungstemperatur des gehärteten Teils werden drei Arten des Anlassens unterschieden: hoch, mittel und niedrig.
Hoher Urlaub hergestellt bei Erwärmungstemperaturen über 350-600 ° C, jedoch unterhalb eines kritischen Punktes; Dieses Anlassen wird auf Baustähle angewendet.
Durchschnittlicher Urlaub hergestellt bei Erwärmungstemperaturen von 350 - 500 ° C; Dieses Anlassen wird häufig für Federn und Federstähle verwendet.
Niedriger Urlaub Es wird bei Temperaturen von 150–250 ° C hergestellt. Die Härte des Teils nach dem Aushärten bleibt nahezu unverändert; Niedrigtemperieren wird für Werkzeugstähle aus Kohlenstoff und Legierungen verwendet, die eine hohe Härte und Verschleißfestigkeit erfordern.
Die Urlaubskontrolle wird gemäß den Farbtönen durchgeführt, die auf der Oberfläche des Teils erscheinen.
Altern
Altern Ist ein Prozess zum Ändern der Eigenschaften von Legierungen ohne merkliche Änderungen in der Mikrostruktur. Es sind zwei Arten der Alterung bekannt: thermische und Verformung.
Thermische Alterung geht infolge von Änderungen der Löslichkeit von Kohlenstoff in Eisen in Abhängigkeit von der Temperatur vor.
Wenn bei Raumtemperatur eine Änderung der Härte, Duktilität und Festigkeit auftritt, spricht man von einer solchen Alterung natürlich.
Wenn der Prozess bei erhöhter Temperatur abläuft, spricht man von Alterung künstlich.
Verformungsalterung (mechanisch) tritt nach kalter plastischer Verformung auf.
Kaltumformung
Eine neue Art der Wärmebehandlung zur Erhöhung der Härte von Stahl durch Umwandlung von Restaustenit aus gehärtetem Stahl in Martensit. Dies erfolgt durch Abkühlen des Stahls auf die Temperatur des unteren martensitischen Punktes.
Oberflächenhärtungsmethoden
Oberflächengehärtet Sie nennen den Wärmebehandlungsprozess, bei dem die Oberflächenschicht aus Stahl auf eine Temperatur über dem kritischen Niveau erhitzt und anschließend abgekühlt wird, um Martensitstrukturen in der Oberflächenschicht zu erhalten.
Folgende Typen werden unterschieden: Induktionshärten; Abschrecken im Elektrolyten, Abschrecken während des Erhitzens durch Hochfrequenzströme (HDTV), Abschrecken mit Gasflammenerwärmung.
Induktionshärten basierend auf einem physikalischen Phänomen, dessen Wesen darin besteht, dass ein elektrischer Strom hoher Frequenz, der durch einen Leiter fließt, ein elektromagnetisches Feld um ihn herum erzeugt. Auf der Oberfläche des in diesem Feld befindlichen Teils werden Wirbelströme induziert, wodurch sich das Metall auf hohe Temperaturen erwärmt. Dies bietet die Möglichkeit von Phasentransformationen.
Je nach Heizmethode wird die Induktionshärtung in drei Typen unterteilt:
gleichzeitiges Erhitzen und Aushärten der gesamten Oberfläche (für kleine Teile);
sequentielles Erhitzen und Härten einzelner Abschnitte (für Kurbelwellen und ähnliche Teile);
kontinuierliches sequentielles Erhitzen und Härten durch Bewegen (für lange Teile).
Gasflammenhärten. Der Gasflammenhärtungsprozess besteht darin, die Oberfläche des Teils schnell mit einer Acetylen-Sauerstoff-, Gas-Sauerstoff- oder Sauerstoff-Kerosin-Flamme auf eine Härtungstemperatur zu erwärmen, gefolgt von Abkühlen mit Wasser oder einer Emulsion.
Aushärten in einem Elektrolyten. Das Abschrecken in einem Elektrolyten erfolgt wie folgt: Ein abgeschreckter Teil wird mit einem Elektrolyten (5–10% ige Lösung von kalziniertem Salz) in ein Bad abgesenkt und ein Strom von 220–250 V wird geleitet. Dadurch wird der Teil auf hohe Temperaturen erhitzt. Die Teile werden entweder im gleichen Elektrolyten (nach Abschalten des Stroms) oder in einem speziellen Abschrecktank gekühlt.
Thermomechanische Behandlung
Die thermomechanische Verarbeitung (TMO) ist eine neue Methode zum Härten von Metallen und Legierungen unter Beibehaltung einer ausreichenden Duktilität, bei der plastische Verformung und Härtewärmebehandlung (Härten und Anlassen) kombiniert werden. Es gibt drei Hauptmethoden der thermomechanischen Verarbeitung.
Thermomechanische Niedertemperaturverarbeitung (N.T.M.O.) basierend auf stufenweisem Härten, dh plastischer Verformung von Stahl wird bei Temperaturen der relativen Stabilität von Austenit mit anschließendem Härten und Anlassen durchgeführt.
Thermomechanische Hochtemperaturverarbeitung (V.T.M.O.) Die plastische Verformung wird bei Austenitstabilitätstemperaturen mit anschließendem Abschrecken und Anlassen durchgeführt.
Vorläufige thermomechanische Behandlung (P.T.M.O.) Die Verformung kann bei den Temperaturen von N.T.M.O. und V.T.M.O. oder bei einer Temperatur von 20 ° C durchgeführt werden. Als nächstes wird die übliche Wärmebehandlung durchgeführt: Härten und Anlassen.
Zweck und Art der chemisch-thermischen Behandlung
Die chemisch-thermische Behandlung bezieht sich auf einen Prozess, der eine Kombination aus thermischer und chemischer Exposition darstellt, um die Zusammensetzung, Struktur und Eigenschaften der Oberflächenschicht aus Stahl zu ändern.
Der Zweck der chemisch-thermischen Behandlung: Erhöhung der Oberflächenhärte, Verschleißfestigkeit, Dauerfestigkeit, Korrosionsbeständigkeit, Wärmebeständigkeit (Ablagerungsbeständigkeit), Säurebeständigkeit.
Die in der Industrie am häufigsten verwendeten Arten der chemisch-thermischen Behandlung sind: Zementierung; Nitrocarburieren; Nitrieren; Cyanidierung; Diffusionsmetallisierung.
Zementieren - ein Prozess der Oberflächensättigung mit Kohlenstoff mit dem Ziel der Oberflächenhärtung von Teilen.
Je nach verwendetem Aufkohler wird die Zementierung in drei Arten unterteilt: Zementierung durch einen festen Aufkohler; Gaszementierung (Methan, Propan, Erdgas).
Gaszementierung . Die Teile werden in speziellen hermetisch abgeschlossenen Öfen auf 900–950 ° C erhitzt, in die zementhaltiges kohlenstoffhaltiges Gas [natürlich (natürlich) oder künstlich] in einem kontinuierlichen Strom eingespeist wird.
Der Prozess zementierung in einem Festvergaser besteht im folgenden. Teile, die in einer Schachtel mit einem Aufkohler (einer Mischung aus Holzkohle und Aktivator) verpackt sind, werden auf eine bestimmte Temperatur erhitzt und lange auf dieser Temperatur gehalten, dann abgekühlt und einer Wärmebehandlung unterzogen.
Die Zementierung unter Verwendung eines der obigen Verfahren wird für Teile aus Kohlenstoff und legiertem Stahl mit einem Kohlenstoffgehalt von nicht mehr als 0,2% verwendet. Das Zementieren von legierten Stählen, die karbidbildende Elemente Cr, W, V enthalten, liefert besonders gute Ergebnisse: Neben der Erhöhung der Oberflächenhärte und der Verschleißfestigkeit erhöhen sie auch die Ermüdungsgrenze.
Nitrieren - Dies ist der Prozess der Sättigung der Oberflächenschicht verschiedener Metalle und Legierungen, Stahlprodukte oder Teile mit Stickstoff, wenn diese in einer geeigneten Umgebung erhitzt wird. Die Oberflächenhärte des Produkts, die Lebensdauer, die Verschleißfestigkeit und die Korrosionsbeständigkeit nehmen zu.
Cyanid - Sättigung der Oberflächenschicht von Produkten gleichzeitig mit Kohlenstoff und Stickstoff.
Je nach verwendetem Medium wird die Cyanidierung unterschieden: in festen Medien; in flüssigen Medien; in gasförmigen Medien.
Je nach Heiztemperatur wird die Cyanidierung in Niedertemperatur und Hochtemperatur unterteilt.
Cyanidierung in flüssigen Medien hergestellt in Bädern mit geschmolzenen Salzen.
Cyanid in gasförmigen Medien (Nitrocarburieren)) Der Prozess der gleichzeitigen Sättigung der Oberfläche eines Teils mit Kohlenstoff und Stickstoff. Zu diesem Zweck werden die Teile in einer Umgebung erhitzt, die aus Zementiergas und Ammoniak besteht, dh das Nitrocarburieren kombiniert Gaszementierungs- und Nitrierprozesse.
Diffusionssättigung mit Metallen und Metalloiden
Es gibt und werden in der Industrie Verfahren zum Sättigen der Oberfläche von Teilen mit verschiedenen Metallen (Aluminium, Chrom usw.) und Metalloiden (Silizium, Bor usw.) angewendet. Der Zweck dieser Sättigung besteht darin, die Ablagerungsbeständigkeit, Korrosionsbeständigkeit, Säurebeständigkeit, Härte und Verschleißfestigkeit von Teilen zu erhöhen. Dadurch erhält die Oberflächenschicht spezielle Eigenschaften, mit denen Legierungselemente eingespart werden können.
Aliting - der Prozess der Sättigung der Oberflächenschicht aus Stahl mit Aluminium zur Erhöhung der Wärmebeständigkeit (Ablagerungsbeständigkeit) und der Beständigkeit gegen atmosphärische Korrosion.
Die Alifizierung erfolgt in Pulvermischungen, in Bädern mit geschmolzenem Aluminium, in einer gasförmigen Umgebung und durch Sprühen von flüssigem Aluminium.
Verchromung - der Prozess der Sättigung der Oberflächenschicht aus Stahl mit Chrom zur Erhöhung der Korrosions- und Wärmebeständigkeit und beim Verchromen von kohlenstoffreichen Stählen - zur Erhöhung der Härte und Verschleißfestigkeit.
Siliziumisierung - der Prozess der Sättigung der Oberflächenschicht eines Teils mit Silizium zur Erhöhung der Korrosions- und Säurebeständigkeit. Teile aus kohlenstoffarmen und mittelkohlenstoffhaltigen Stählen sowie aus formbaren und duktilen Gusseisen werden einer Siliziumisierung unterzogen.
Langweilig - der Prozess der Sättigung der Oberflächenschicht des Teils mit Bor. Der Zweck der Borierung besteht darin, die Härte, die Beständigkeit gegen Abrieb und Korrosion in aggressiven Umgebungen, die Wärmebeständigkeit und die Wärmebeständigkeit von Stahlteilen zu erhöhen. Es gibt zwei Methoden der Borierung: Flüssigelektrolyse und Gasborierung.
Sulfidierung - der Prozess der Sättigung der Oberflächenschicht von Stahlteilen mit Schwefel, um die extremen Druckeigenschaften zu verbessern und die Verschleißfestigkeit von Teilen zu erhöhen.
Sulfocyanierung - der Prozess der Oberflächensättigung von Stahlteilen mit Schwefel, Kohlenstoff und Stickstoff. Die kombinierte Wirkung von Schwefel und Stickstoff in der Oberflächenschicht des Metalls bietet höhere Extremdruckeigenschaften und Verschleißfestigkeit im Vergleich zur Sättigung nur mit Schwefel.
Wärmebehandlung aus Gusseisen
Die Wärmebehandlung von Gusseisen wird durchgeführt, um innere Spannungen, die während des Gießens auftreten, abzubauen und Änderungen der Größe und Form des Gusses im Laufe der Zeit zu verursachen, die Härte zu verringern und die Bearbeitbarkeit durch Schneiden zu verbessern und die mechanischen Eigenschaften zu verbessern. Gusseisen wird geglüht, normalisiert, gehärtet und angelassen sowie bestimmten chemisch-thermischen Behandlungen (Nitrieren, Aluminieren, Verchromen) unterzogen.
Glühen zur Entlastung innerer Spannungen . Gusseisen wird bei den folgenden Temperaturen geglüht: Grauguss mit Lamellengraphit 500 - 570ºС; hochfestes Gusseisen mit kugelförmigem Graphit 550 - 650ºС; niedriglegiertes Gusseisen 570 - 600ºС; hochlegiertes Gusseisen 620 - 650ºС. Während dieses Temperns treten keine Phasenumwandlungen auf, aber innere Spannungen werden entfernt, Viskositätserhöhungen, Verformungen und Risse während des Betriebs werden ausgeschlossen.
Erweichungsglühen (Niedertemperatur-Graphitglühen ). Durchgeführt, um die Bearbeitbarkeit durch Schneiden zu verbessern und die Duktilität zu erhöhen. Es wird durch längere Exposition bei 680 - 700 ° C oder durch langsames Abkühlen der Gussteile bei 760 - 700 ° C durchgeführt. Bei Teilen mit komplexer Konfiguration ist die Abkühlung langsam und bei Teilen mit einfacher Form beschleunigt.
Graphitglühen wodurch duktiles Eisen aus weißem Gusseisen gewonnen wird.
Normalisierung Wird verwendet, um gebundenen Kohlenstoff zu erhöhen, die Härte, Festigkeit und Verschleißfestigkeit von grauen, formbaren und hochfesten Gusseisen zu erhöhen. Während der Normalisierung wird Gusseisen (Gussteile) über die Temperaturen des Umwandlungsintervalls von 850 - 950 ° C erhitzt und nach dem Aussetzen an der Luft abgekühlt.
Abschrecken grauem, formbarem und duktilem Gusseisen ausgesetzt, um die Härte, Festigkeit und Verschleißfestigkeit zu erhöhen. Gemäß der Ausführungsmethode kann das Härten von Gusseisen kontinuierlich volumetrisch, isotherm und oberflächenbezogen sein.
Bei volumetrische kontinuierliche Härtung Gusseisen wird auf eine Temperatur von 850 - 950 ° C erhitzt. Dann zum Erhitzen und vollständigen Auflösen von Kohlenstoff stehen. Die Kühlung erfolgt in Wasser oder Öl. Nach dem Abschrecken wird ein Urlaub bei einer Temperatur von 200 - 600 ° C durchgeführt. Das Ergebnis ist eine erhöhte Härte, Festigkeit und Verschleißfestigkeit von Gusseisen.
Bei isotherme Härtung Gusseisen wird wie bei kontinuierlichem Eisen erhitzt th Abschrecken, 10 bis 90 Minuten inkubiert und in geschmolzenem Salz auf 200 - 400 ° C abgekühlt und nach Alterung an der Luft abgekühlt.
Oberflächenhärtung durch Erhitzen der Oberflächenschicht mit einer Sauerstoff-Acetylen-Flamme, Hochfrequenzströmen oder in einem Elektrolyten. Heiztemperatur 900 - 1000ºС. Abkühlen in Wasser, Öl oder Ölemulsion.
Altern Wird verwendet, um die Größe von Gusseisenteilen zu stabilisieren, Verwerfungen zu verhindern und innere Spannungen abzubauen. In der Regel erfolgt die Alterung nach der Grobbearbeitung. Es gibt zwei Arten des Alterns: natürliche und künstliche.
Natürliches Altern im Freien oder drinnen durchgeführt. Produkte nach dem Gießen werden 6 bis 15 Monate gealtert.
Künstliches Altern bei erhöhten Temperaturen durchgeführt; Dauer - einige Stunden. Während der künstlichen Alterung werden Eisengussteile in einen auf 100 bis 200 ° C erhitzten Ofen geladen, mit einer Geschwindigkeit von 30 bis 60 ° C pro Stunde auf eine Temperatur von 550 bis 570 ° C erhitzt, 3 bis 5 Stunden gealtert und zusammen mit dem Ofen mit einer Geschwindigkeit von 20 bis 40 ° C pro Stunde auf eine Temperatur von 150 abgekühlt - 200ºС und dann an der Luft abgekühlt.
Chemische und Wärmebehandlung von Gusseisen
Um die Oberflächenhärte und die Verschleißfestigkeit zu erhöhen, werden Graugussteile einem Nitrieren unterzogen. Meistens nitrilgraues Perlitgusseisen, legiert mit Chrom, Molybdän, Aluminium. Nitriertemperatur 550 - 580ºС, Haltezeit 30 - 70 Stunden. Zusätzlich zum Nitrieren kann bei einer Temperatur von 570 ° C eine Erhöhung der Oberflächenhärte und der Verschleißfestigkeit von legiertem grauem perlitischem Eisen, Gas und flüssiger Cyanidierung erreicht werden. Um die Wärmebeständigkeit zu erhöhen, können Gusseisengussteile alitisiert werden und um eine hohe Korrosionsbeständigkeit in Säuren zu erreichen, Verkieselung.
Wärmebehandlung von Nichteisenmetalllegierungen
Aluminiumlegierungen
Aluminiumlegierungen werden drei Arten von Wärmebehandlungen unterzogen: Glühen, Härten und Altern. Haupttypen glühen sind: Diffusion, Rekristallisation und thermisch gehärtete Legierungen.
Homogenisierung wird verwendet, um die chemische Mikroinhomogenität von Körnern einer festen Lösung auszugleichen. Zur Durchführung der Homogenisierung werden Aluminiumlegierungen auf 450 bis 520 ° C erhitzt und bei diesen Temperaturen von 4 bis 40 Stunden gehalten; nach dem Aussetzen - Abkühlen mit dem Ofen oder Luft. Infolgedessen wird die Struktur gleichmäßiger und die Duktilität nimmt zu.
Rekristallisationsglühen Für Aluminium und seine Legierungen wird es viel breiter als für Stahl verwendet. Dies erklärt sich aus der Tatsache, dass Metalle wie Aluminium und Kupfer sowie viele darauf basierende Legierungen nicht durch Härten gehärtet werden und die Erhöhung der mechanischen Eigenschaften nur durch Kaltdruckbehandlung erreicht werden kann und das Rekristallisationsglühen ein Zwischenvorgang während einer solchen Verarbeitung ist. Die Temperatur des Rekristallisationsglühens von Aluminiumlegierungen 300 - 500ºС Belichtung 0,5 - 2 Stunden.
Glühen von thermisch gehärteten Legierungen Wird verwendet, um das Aushärten vollständig zu entfernen. Es wird bei Temperaturen von 350 bis 450 ° C durchgeführt, wobei 1 bis 2 Stunden gehalten und anschließend ziemlich langsam abgekühlt wird.
Nachher härten Die Festigkeit der Legierung wird leicht erhöht und die Duktilität ändert sich nicht. Nach dem Abschrecken werden Aluminiumlegierungen ausgesetzt altern bei dem die Zersetzung der übersättigten festen Lösung erfolgt.
Aluminiumknetlegierungen
Im gehärteten Zustand ist Duraluminium plastisch und verformt sich leicht. Nach dem Aushärten und der natürlichen oder künstlichen Alterung nimmt die Festigkeit von Duraluminium stark zu.
Gießerei Aluminiumlegierungen
Bei Aluminiumgusslegierungen werden je nach chemischer Zusammensetzung verschiedene Arten der Wärmebehandlung angewendet. Zum Härten werden Aluminiumgusslegierungen abgeschreckt, um eine übersättigte feste Lösung und künstliche Alterung zu erhalten, und nur ohne Alterung abgeschreckt, um eine stabile feste Lösung im abgeschreckten Zustand zu erhalten.
Magnesiumlegierungen
Magnesiumlegierungen werden wie Aluminiumlegierungen geglüht, abgeschreckt und gealtert. Um die chemische Mikroinhomogenität der Körner der festen Lösung durch Diffusion auszugleichen, werden Barren aus Magnesiumlegierungen ausgesetzt homogenisierung bei Temperaturen von 350 - 400ºС mit einer Exposition von 18 - 24 Stunden. Halbzeuge aus Magnesium-Knetlegierungen werden unterworfen rekristallisationsglühen bei einer Temperatur von ≈ 350ºС sowie bei niedrigeren Temperaturen von 150 - 250ºС Glühen, um Restspannungen abzubauen.
Magnesiumlegierungen unterliegen abschrecken oder abschrecken und künstliches Altern . Bei einer Temperatur von 20 ° C in abgeschreckten Magnesiumlegierungen treten keine Änderungen auf, dh sie unterliegen keiner natürlichen Alterung.
Kupfer und Kupferlegierungen
Kupferwärmebehandlung . Die Verformung von Kupfer geht mit einer Zunahme seiner Festigkeit und einer Abnahme der Duktilität einher. Um die Duktilität zu erhöhen, wird Kupfer bei 500 bis 600 ° C einem Rekristallisationsglühen unterzogen, wodurch die Duktilität stark erhöht und die Festigkeit verringert wird.
Wärmebehandlung aus Messing . Sie werden nur bei 600 - 700 ° C einem Rekristallisationsglühen unterzogen (um das Aushärten zu entfernen). Messing wird beim Tempern an Luft oder zur Beschleunigung des Abkühlens und zur besseren Abscheidung von Zunder in Wasser gekühlt. Für Messingteile, die nach der Verformung Restspannungen aufweisen, ist in einer feuchten Atmosphäre ein spontanes Rissphänomen typisch. Um dies zu vermeiden, werden die Messingteile bei 200 - 300 ° C bei niedriger Temperatur geglüht, wodurch die Restspannungen beseitigt werden und die Aushärtung erhalten bleibt. Es ist besonders notwendig, Aluminiummessing einem Niedertemperaturglühen auszusetzen, das zu spontanen Rissen neigt.
Wärmebehandlung von Bronzen . Um die chemische Zusammensetzung der Bronze auszugleichen, werden sie bei 700 - 750 ° C homogenisiert und anschließend schnell abgekühlt. Um innere Spannungen abzubauen, werden Gussteile bei 550 ° C geglüht. Um die Plastizität zwischen den Kaltumformvorgängen wiederherzustellen, wird es einem Rekristallisationsglühen bei 600 bis 700 ° C unterzogen.
Aluminiumbronze Bei einem Aluminiumgehalt von 8 bis 11% kann es beim Erhitzen und Abkühlen zu einer Phasenrekristallisation kommen härten. Infolge des Aushärtens nehmen Festigkeit und Härte zu, aber die Duktilität nimmt ab. Nach dem Aushärten sollte urlaub bei 400 - 650º С abhängig von den erforderlichen Eigenschaften. Auch Betreff homogenisierung und verformbare Halbzeuge - rekristallisationsglühen bei 650 - 800ºС.
Berylliumbronze temperament in Wasser von einer Temperatur von 760 - 780ºС; In diesem Fall hat die überschüssige Phase keine Zeit zum Trennen, und nach dem Abschrecken besteht die Legierung aus einer übersättigten festen Lösung und weist eine geringe Härte und Festigkeit sowie eine hohe Duktilität auf. Nach dem Aushärten erfolgt urlaub (Alterung) bei 300 - 350ºC bei einer Exposition von 2 Stunden. Um die Stabilität der übersättigten festen Lösung zu erhöhen und das Aushärten zu erleichtern, werden zusätzlich Berylliumbronzen verwendet mit Nickel legiert .
Titanlegierungen
Titanlegierungen werden einem Rekristallisationsglühen und Glühen mit Phasenrekristallisation sowie einem Härten durch Wärmebehandlung - Abschrecken und Altern - unterzogen. Zur Erhöhung der Verschleißfestigkeit und Ritzbeständigkeit werden Titanlegierungen Nitrieren, Zementieren oder Oxidieren unterzogen.
Rekristallisationsglühen wird für Titan und Legierungen zum Aushärten nach Kaltumformung verwendet. Die Temperatur des Rekristallisationsglühens beträgt 520 - 850ºC, abhängig von der chemischen Zusammensetzung der Legierung und der Art des Halbzeugs.
Phasenrekristallisationsglühen Wird verwendet, um die Härte zu verringern, die Duktilität zu erhöhen, das Korn zu schleifen und strukturelle Heterogenität zu beseitigen. Einfaches, isothermes und doppeltes Tempern anwenden; Erwärmungstemperatur beim Glühen 750 - 950º50 je nach Legierung.
Bei isothermes Glühen Nach dem Aussetzen der Glühtemperatur werden die Teile im selben Ofen auf 500 - 650 ° C (abhängig von der Legierung) abgekühlt, gehen, in einen anderen Ofen überführt und für eine bestimmte Zeit gehalten und an der Luft abgekühlt. Beim isothermen Tempern wird die Glühzeit reduziert und die Duktilität ist höher.
Bei doppelglühen Die Teile werden auf die Glühtemperatur erwärmt, an Luft gehalten und gekühlt. Dann auf 500 - 650ºС erwärmen, an der Luft halten und abkühlen lassen. Doppelglühen im Vergleich zu Isotherme erhöht die Zugfestigkeit bei leichter Abnahme der Duktilität und verkürzt die Verarbeitungszeit.
Von allen Arten der chemisch-thermischen Behandlung von Titanlegierungen wird am häufigsten das Nitrieren verwendet, das in einem Stickstoffmedium oder in einem Gemisch aus Stickstoff und Argon bei Temperaturen von 850 bis 950 ° C für 10 bis 50 Stunden durchgeführt wird. Teile aus Titanlegierungen nach dem Nitrieren haben gute Gleitfähigkeitseigenschaften.
Fazit
Die Wärmebehandlung ist einer der wichtigsten Vorgänge des gesamten technologischen Verarbeitungszyklus. Die Qualität (mechanische und physikalisch-chemische Eigenschaften) der hergestellten Teile von Maschinen und Mechanismen, Werkzeugen und anderen Produkten hängt von der ordnungsgemäßen Ausführung ab. Verfahren zur Wärmebehandlung von Grau- und Weißgusseisen sowie Nichteisenlegierungen wurden entwickelt und optimiert
Eine vielversprechende Richtung zur Verbesserung der Wärmebehandlungstechnologie ist die Installation von Wärmebehandlungsanlagen in Werkstätten, die Schaffung automatischer Leitungen unter Einbeziehung von Wärmebehandlungsprozessen sowie die Entwicklung von Methoden zur Verbesserung der Festigkeitseigenschaften von Teilen, ihrer Zuverlässigkeit und Haltbarkeit.
Literatur
1. B.V. Zakharov. V.N. Berseneva "Fortgeschrittene technologische Prozesse und Geräte für die Wärmebehandlung von Metallen" M. Higher School 1988
2. V.M. Zuev "Thermische Verarbeitung von Metallen" M. Higher School 1986
3. B.A. Kuzmin "Technologie von Metallen und Strukturmaterialien" M. "Engineering" 1981
4. V.M. Nikiforov "Technologie von Metallen und Baustoffen" M. "Higher School" 1968
5. A.I. Samokhotsky N.G. Parfyonovskaya "Technologie der Wärmebehandlung von Metallen" M. Mechanical Engineering 1976
INTEGRIERTE METALLBEHANDLUNG
Wärmebehandlung (wärmebehandlung ) Stahllegierungen Es gibt folgende Typen: glühen, normalisierung, härten, urlaub.
- Glühen - Wärmebehandlung (Wärmebehandlung) des Metalls, bei dem das Metall erhitzt wird, und anschließendes langsames Abkühlen. Diese Wärmebehandlung (d. H. Glühen) kann von verschiedenen Arten sein (die Art des Glühens hängt von der Erwärmungstemperatur, der Abkühlgeschwindigkeit des Metalls ab).
- Abschrecken - Wärmebehandlung (Wärmebehandlung) von Stahl, Legierungen, basierend auf der Rekristallisation von Stahl (Legierungen) beim Erhitzen auf eine Temperatur über dem kritischen Wert; Nach ausreichender Exposition bei einer kritischen Temperatur folgt eine schnelle Abkühlung, um die Wärmebehandlung abzuschließen. Gehärteter Stahl (Legierung) hat eine Nichtgleichgewichtsstruktur, daher ist eine andere Art der Wärmebehandlung anwendbar - das Tempern.
- Urlaub - Wärmebehandlung (Wärmebehandlung) von Stahl, Legierungen, die nach dem Abschrecken durchgeführt wird, um Restspannungen in Stahl und Legierungen zu verringern oder zu entfernen, die Viskosität zu erhöhen, die Härte und Sprödigkeit des Metalls zu verringern.
- Normalisierung - Wärmebehandlung (Wärmebehandlung), ähnlich dem Glühen. Die Unterschiede zwischen diesen Wärmebehandlungen (Normalisierung und Glühen) bestehen darin, dass der Stahl während der Normalisierung an Luft gekühlt wird (während des Glühens - im Ofen).
STAHL ANNEALING
Das Tempern ist ein Metallwärmebehandlungsprozess, bei dem erhitzt wird und das Metall dann langsam abgekühlt wird. Der Übergang der Struktur von einem Nichtgleichgewichtszustand zu einem Gleichgewichtszustand. Glühen der ersten Art , seine Typen: zurück (auch bekannt als Metallauflage) rekristallisationsglühen (Es heißt rekristallisation), entspannungsglühen , diffusionsglühen (auch genannt homogenisierung). Glühen der zweiten Art - Ändern der Struktur der Legierung durch Rekristallisation in der Nähe kritischer Punkte, um Gleichgewichtsstrukturen zu erhalten. Glühen der zweiten Art, seiner Arten: voll , unvollständig , isotherm glühen. Unten ist das Glühen seiner Typen, wie es auf Stahl angewendet wird.
- Zurück (Rest-) Stahl - Erhitzen auf 200 - 400 ° C, Glühen, um die Aushärtung zu verringern oder zu entfernen. Entsprechend den Glühergebnissen wird eine Abnahme der Kristallgitterverzerrungen in Kristalliten und eine teilweise Wiederherstellung der physikochemischen Eigenschaften von Stahl beobachtet.
- Rekristallisationsstahlglühen (Rekristallisation) - Erhitzen auf Temperaturen von 500 - 550 ° C; Glühen zur Entlastung innerer Spannungen - Erwärmung auf Temperaturen von 600 - 700 ° C. Diese Arten des Glühens entlasten die inneren Spannungen von Metallgussteilen von ungleichmäßiger Abkühlung ihrer Teile, auch bei Werkstücken, die durch Druck (Walzen, Ziehen, Stanzen) bei Temperaturen unter kritischen Werten behandelt werden. Aufgrund des Rekristallisationsglühens wachsen neue Kristalle aus den verformten Körnern heraus, näher am Gleichgewicht, daher nimmt die Härte des Stahls ab und die Duktilität und Zähigkeit nehmen zu. Um die inneren Spannungen von Stahl vollständig zu beseitigen, ist eine Temperatur von mindestens 600 ° C erforderlich. Das Abkühlen nach dem Halten bei einer bestimmten Temperatur sollte ziemlich langsam sein: Aufgrund der beschleunigten Abkühlung des Metalls treten wieder innere Spannungen auf.
- Diffusionsstahlglühen (Homogenisierung) wird angewendet, wenn der Stahl eine intrakristalline Entmischung aufweist. Die Ausrichtung der Zusammensetzung in Austenitkörnern wird durch Diffusion von Kohlenstoff und anderen Verunreinigungen im festen Zustand zusammen mit Selbstdiffusion von Eisen erreicht. Entsprechend den Glühergebnissen wird Stahl in seiner Zusammensetzung homogen (homogen), daher wird auch Diffusionsglühen genannt homogenisierung. Die Homogenisierungstemperatur sollte hoch genug sein, es sollte jedoch nicht erlaubt sein, brennende Körner zu verbrennen. Wenn Ausbrennen erlaubt ist, oxidiert Luftsauerstoff Eisen und dringt in seine Dicke ein. Es bilden sich Kristallite, die durch Oxidschalen getrennt sind. Die Verbrennung kann nicht beseitigt werden, daher sind die verbrannten Rohlinge die endgültige Ehe. Das Diffusionsglühen von Stahl führt normalerweise zu einer zu starken Kornvergrößerung, die durch anschließendes vollständiges Glühen (zu feinkörnigem Korn) korrigiert werden sollte.
- Vollstahlglühen verbunden mit Phasenrekristallisation, Kornmahlen bei Punkttemperaturen AC1 und AC2. Ziel ist es, die Struktur des Stahls zu verbessern, um die anschließende Verarbeitung durch Schneiden, Stanzen oder Härten zu erleichtern und eine feinkörnige Gleichgewichtsperlitstruktur des fertigen Teils zu erhalten. Für ein vollständiges Glühen wird der Stahl 30-50 ° C über die Temperatur der GSK-Leitung erhitzt und langsam abgekühlt. Nach dem Tempern haben überschüssiger Zementit (in hypereutektoiden Stählen) und eutektoider Zementit die Form von Platten, daher wird Perlit als Lamellen bezeichnet
- Beim Glühen von Stahl auf Plattenperlit knüppel bleiben bis zum Abkühlen im Ofen, meistens bei teilweiser Erwärmung des Ofens mit Brennstoff, so dass die Abkühlrate nicht mehr als 10-20 ° C pro Stunde beträgt. Das Glühen wird auch beim Mahlen von Korn erreicht. Eine grobkörnige Struktur, beispielsweise aus übereutektoidem Stahl, wird während der Verfestigung aufgrund des freien Kornwachstums (wenn die Gussteile langsam abgekühlt werden) sowie infolge einer Überhitzung des Stahls erhalten. Diese Struktur heißt Widmannstett (nach dem Namen des österreichischen Astronomen A. Widmanstetten, der 1808 eine solche Struktur auf Meteoreisen entdeckte). Diese Struktur verleiht dem Werkstück eine geringe Festigkeit. Die Struktur zeichnet sich dadurch aus, dass Einschlüsse von Ferrit (helle Bereiche) und Perlit (dunkle Bereiche) in Form von länglichen Platten in unterschiedlichen Winkeln zueinander angeordnet sind. Bei den hypereutektoiden Stählen ist die Widmanshtet-Struktur durch eine gestrichelte Anordnung von überschüssigem Zementit gekennzeichnet. Das Mahlen von Getreide ist mit der Rekristallisation von Alpha-Eisen zu Gamma-Eisen verbunden. Durch die Abkühlung und den umgekehrten Übergang von Gamma-Eisen zu Alpha-Eisen bleibt die feinkörnige Struktur erhalten. Eines der Ergebnisse des Temperns auf lamellarem Perlit ist daher eine feinkörnige Struktur.
- Unvollständiges Stahlglühen verbunden mit Phasenrekristallisation nur bei einer Punkttemperatur A C1;; Nach der Heißdruckbehandlung wird ein unvollständiges Glühen angewendet, wenn das Werkstück eine feinkörnige Struktur aufweist.
- Glühen von Stahl auf körnigem Perlit Wird normalerweise für eutektoide, übereutektoide Stähle verwendet, um die Duktilität und Zähigkeit des Stahls zu erhöhen und seine Härte zu verringern. Um körniges Perlit zu erhalten, wird Stahl über einen Punkt erhitzt AC1, dann kurz inkubiert, damit sich Zementit nicht vollständig in Austenit löst. Dann wird der Stahl auf eine etwas niedrigere Temperatur abgekühlt Ar1 mehrere Stunden bei dieser Temperatur gehalten. In diesem Fall dienen die Partikel des verbleibenden Zementits als Kristallisationskerne für den gesamten freigesetzten Zementit, der mit in Ferrit dispergierten runden (kugelförmigen) Kristalliten wächst. Die Eigenschaften von körnigem Perlit unterscheiden sich signifikant von den Eigenschaften von Lamellen in Richtung geringerer Härte, aber größerer Lamellen und Viskosität. Dies gilt insbesondere für hypereutektoiden Stahl, bei dem der gesamte Zementit (sowohl eutektoid als auch überschüssig) in Form von Kügelchen erhalten wird.
- Isothermes Glühen - Nach dem Erhitzen und Altern wird der Stahl schnell auf eine Temperatur abgekühlt, die etwas unter dem Punkt liegt A 1, dann bis zur vollständigen Zersetzung von Austenit zu Perlit auf dieser Temperatur gehalten und dann an der Luft abgekühlt. Die Verwendung von isothermem Tempern reduziert die Zeit erheblich und verbessert auch die Produktivität. Beispielsweise dauert das normale Glühen von legiertem Stahl 13 bis 15 Stunden und das isotherme Glühen nur 4 bis 7 Stunden.
Stahl härten
Es gibt eine Härtung mit polymorpher Umwandlung für Stähle und eine Härtung ohne polymorphe Umwandlung für die meisten Nichteisenmetalle. Das gehärtete Material erhält eine größere Härte, wird jedoch spröde, weniger duktil und viskos, wenn mehr Heiz-Kühl-Wiederholungen durchgeführt werden. Um die Sprödigkeit zu verringern und die Duktilität und Viskosität zu erhöhen, wird nach dem Abschrecken mit polymorpher Umwandlung eine Temperierung angewendet. Nach dem Abschrecken ohne polymorphe Umwandlung wird Alterung verwendet. Beim Tempern nimmt die Härte und Festigkeit des Materials leicht ab.
Abhängig von der Erwärmungstemperatur wird das Abschrecken in vollständig und unvollständig unterteilt. Bei vollständiger Aushärtung wird das Material 30 - 50 ° C über der GS-Linie für den hypereutektoiden Stahl und die eutektoide, hypereutektoide Linie PSK erhitzt. In diesem Fall erhält der Stahl eine Austenit- und Austenit + Zementit-Struktur. Bei unvollständiger Aushärtung wird oberhalb der PSK-Linie des Diagramms erhitzt, was zur Bildung überschüssiger Phasen am Ende der Aushärtung führt. Eine unvollständige Härtung wird im Allgemeinen für Werkzeugstähle verwendet. Das Anlassen wird durch Anlassen entfernt. Einige Produkte werden teilweise gehärtet, beispielsweise bei der Herstellung japanischer Katanas, nur die Schneide des Schwertes wird gehärtet.
Medien härten
Beim Abschrecken erfordert die Unterkühlung des Austenits auf die Temperatur der martensitischen Umwandlung eine schnelle Abkühlung, jedoch nicht im gesamten Temperaturbereich, sondern nur im Bereich von 650 bis 400 ° C, dh in dem Temperaturbereich, in dem Austenit am wenigsten stabil ist, und wird am schnellsten zu Ferrit-Zementit die Mischung. Oberhalb von 650 ° C ist die Austenitumwandlungsrate niedrig, und daher kann das Gemisch während des Abschreckens in diesem Temperaturbereich langsam abgekühlt werden, aber natürlich nicht so sehr, dass die Ausfällung von Ferrit oder die Umwandlung von Austenit zu Perlit beginnt.
Der Wirkungsmechanismus von Abschreckmedien (Wasser, Öl, Wasser-Polymer-Abschreckmedium (Term) sowie Kühlteile in Salzlösungen) ist wie folgt. Wenn das Produkt in das Abschreckmedium eingetaucht wird, bildet sich um ihn herum ein Film aus überhitztem Dampf, und die Abkühlung erfolgt durch die Schicht dieses Dampfmantels, dh relativ langsam. Wenn die Oberflächentemperatur einen bestimmten Wert erreicht (bestimmt durch die Zusammensetzung der Abschreckflüssigkeit), bei dem der Dampfmantel bricht, beginnt die Flüssigkeit auf der Oberfläche des Teils zu kochen, und das Abkühlen erfolgt schnell.
Die erste Stufe des relativ langsamen Kochens wird als Filmsiedestufe bezeichnet, die zweite Stufe des schnellen Abkühlens wird als Blasensiedestufe bezeichnet. Wenn die Oberflächentemperatur des Metalls niedriger als der Siedepunkt der Flüssigkeit ist, kann die Flüssigkeit nicht mehr kochen und die Abkühlung verlangsamt sich. Diese Stufe wird als konvektive Wärmeübertragung bezeichnet.
Härtungsmethoden
- Abschrecken in einem Kühler - Ein auf eine bestimmte Temperatur erhitzter Teil wird in eine Abschreckflüssigkeit getaucht, wo er bis zur vollständigen Abkühlung verbleibt. Diese Methode dient zum Härten von einfachen Teilen aus Kohlenstoff- und legierten Stählen.
- Intermittierendes Härten in zwei Umgebungen- Diese Methode wird beim Härten von Stählen mit hohem Kohlenstoffgehalt angewendet. Das Teil wird zuerst in einem schnell abkühlenden Medium (z. B. Wasser) und dann in einem langsam abkühlenden Medium (Öl) schnell abgekühlt.
- Strahlhärten besteht darin, das Teil mit einem intensiven Wasserstrahl zu besprühen und wird normalerweise verwendet, wenn es notwendig ist, einen Teil des Teils zu härten. Bei diesem Verfahren wird kein Dampfmantel gebildet, der eine tiefere Härtbarkeit bietet als das einfache Abschrecken in Wasser. Ein solches Härten wird üblicherweise in Induktivitäten in Hochfrequenzeinheiten durchgeführt.
- Stufenhärten - Abschrecken, bei dem das Teil in einem Abschreckmedium mit einer Temperatur über dem martensitischen Punkt für einen bestimmten Stahl gekühlt wird. Beim Abkühlen und Halten in dieser Umgebung muss der gehärtete Teil an allen Punkten des Querschnitts die Temperatur des Abschreckbades erreichen. Dann kommt die endgültige, normalerweise langsame Abkühlung, während der das Abschrecken auftritt, dh die Umwandlung von Austenit in Martensit.
- Isotherme Härtung. Anders als beim isothermen Härten ist es erforderlich, Stahl im Härtungsmedium so lange zu widerstehen, dass die isotherme Umwandlung von Austenit bereits beendet ist.
STAHLURLAUB
Stahl anlassen mildert den Härtungseffekt, reduziert oder beseitigt Restspannungen, erhöht die Viskosität, verringert die Härte und Sprödigkeit von Stahl. Der Urlaub wird durch Erhitzen von auf Martensit gehärteten Teilen auf eine Temperatur unterhalb der kritischen Temperatur hergestellt. Darüber hinaus können abhängig von der Erwärmungstemperatur die Zustände von Martensit, Troostit oder Temperiersorbit erhalten werden. Diese Zustände unterscheiden sich geringfügig von den entsprechenden Abschreckzuständen in Struktur und Eigenschaften: Während des Abschreckens wird Zementit (in Troostit und Sorbit) in Form von länglichen Platten wie in Plattenperlit erhalten. Und im Urlaub stellt sich heraus, dass es körnig oder spitz ist, wie bei körnigem Perlit.
Der Vorteil der Punktstruktur ist eine günstigere Kombination von Festigkeit und Duktilität. Bei gleicher chemischer Zusammensetzung und gleicher Härte weist der Stahl mit Punktstruktur eine deutlich höhere relative Verengung und Schlagfestigkeit auf aber nerhöhte Dehnung d und Streckgrenze s t im Vergleich zu Stahl mit einer Plattenstruktur.
Das Löschen von Martensit hat ein instabiles tetragonales Gitter, und das Tempern von Martensit hat ein stabil zentriertes kubisches Alpha-Eisengitter.
Die Feiertage werden je nach Heiztemperatur in niedrig, mittel und hoch unterteilt.
Zur Bestimmung der Temperatur bei Verwendung des Produkts verfärbung Farbkarte . Ein dünner Film aus Eisenoxiden, der dem Metall verschiedene sich schnell ändernde Farben verleiht - von hellgelb bis grau. Ein solcher Film entsteht, wenn das zunderfreie Stahlprodukt auf 220 ° C erhitzt wird; Mit zunehmender Erwärmungszeit oder steigender Temperatur verdickt sich der Oxidfilm und seine Farbe ändert sich. Die Farben der Tönung sind sowohl auf rohem als auch auf gehärtetem Stahl gleichermaßen erkennbar.
Bei niedriger Urlaub (Erhitzen auf eine Temperatur von 200-300 ° C) in der Struktur des Stahls bleibt hauptsächlich Martensit, der jedoch das Gitter verändert. Zusätzlich beginnt die Ausfällung von Eisencarbiden aus einer festen Kohlenstofflösung in Alpha-Eisen und deren anfängliche Anreicherung in kleinen Gruppen. Dies führt zu einer leichten Abnahme der Härte und einer Zunahme der plastischen und viskosen Eigenschaften von Stahl sowie zu einer Abnahme der inneren Spannungen in den Teilen. Bei niedrigen Temperaturen werden Teile für eine bestimmte Zeit aufbewahrt, normalerweise in Öl- oder Salzbädern. Wenn die Teile zum Tempern an Luft erwärmt werden, verwenden sie zur Temperaturregelung häufig Farbtöne, die auf der Oberfläche des Teils erscheinen. Das Auftreten dieser Farben ist mit der Interferenz von weißem Licht in Eisenoxidfilmen verbunden, die beim Erhitzen auf der Oberfläche eines Teils auftreten. Im Temperaturbereich von 220 bis 330 ° C ändert sich die Farbe je nach Filmdicke von hellgelb nach grau. Niedrigtemperieren wird zum Schneiden, Messen von Werkzeugen und Zahnrädern verwendet.
Bei durchschnitt (Erhitzen innerhalb von 300-500 ° C) und hoch (500-700 ° C) Wenn der Stahl aus dem Martensitzustand freigesetzt wird, geht er in den Zustand von Troostit bzw. Sorbit über. Je höher das Anlassen, desto geringer die Härte des angelassenen Stahls und desto größer seine Duktilität und Zähigkeit. Beim Hochtemperieren erhält Stahl die beste Kombination von mechanischen Eigenschaften, wodurch Indikatoren wie Festigkeit, Duktilität und Zähigkeit erhöht werden. Daher wird das Hochtemperieren von Stahl nach dem Abschrecken auf Martensit zur Wärmebehandlung von Schmiedewerkzeugen, Federn, Federn und Hoch für viele Teile verwendet, die hohen Belastungen ausgesetzt sind Spannungen (z. B. Automobilachsen, Motorstangen).
Bei einigen Stahlsorten wird nach dem Normalisieren getempert. Dies bezieht sich auf einen feinkörnigen legierten doeutektoiden Stahl (insbesondere Nickel) mit einer hohen Viskosität und daher einer schlechten Bearbeitbarkeit mit einem Schneidwerkzeug. Um die Bearbeitbarkeit zu verbessern, wird Stahl bei erhöhter Temperatur (bis zu 950-970 ° C) normalisiert, wodurch er eine große Struktur erhält (was eine bessere Bearbeitbarkeit bestimmt) und gleichzeitig die Härte erhöht (aufgrund der geringen kritischen Rate des Abschreckens von Nickelstahl). Um die Härte zu verringern, wird ein hohes Anlassen dieses Stahls durchgeführt.
STAHLNORMALISIERUNG
Normalisierung bezieht sich auf diese Art der Wärmebehandlung, wenn Stahl 30–50 ° C über die oberen kritischen Temperaturen Ac3 oder Ast erhitzt und nach dem Aussetzen bei diesen Temperaturen in ruhiger Luft abgekühlt wird. Somit unterscheidet sich die Normalisierung vom Tempern durch schnelleres Abkühlen des Produkts (etwa zweimal).
Die Normalisierung ist billiger als das Tempern, da Öfen nur zum Erhitzen und Halten des Produkts auf einer Erwärmungstemperatur verwendet werden und das Abkühlen außerhalb des Ofens durchgeführt wird. Darüber hinaus beschleunigt die Normalisierung den Wärmebehandlungsprozess. Somit wird das Tempern vorteilhafterweise durch Normalisierung ersetzt. Dies ist jedoch nicht immer möglich, da bei einigen Stählen die Härte nach der Normalisierung stärker zunimmt als beim Glühen. Es wird empfohlen, kohlenstoffarme Stähle einer Normalisierung zu unterziehen, da sie nach dem Tempern und Normalisieren praktisch keinen Unterschied in den Eigenschaften aufweisen.
Stähle mit mehr als 0,4% Kohlenstoff erhalten nach der Normalisierung eine erhöhte Härte. Diese sind besser geglüht. In der Praxis werden solche Stähle häufig einer Normalisierung anstelle eines Glühens und anschließend einem Hochtemperieren bei Temperaturen von 650 bis 700 ° C unterzogen, um die Härte zu verringern. Die Normalisierung wird verwendet, um eine feinkörnige Struktur in Gussteilen und Schmiedeteilen zu erhalten, innere Spannungen und Aushärtungen zu beseitigen und die Stahlstruktur für das Aushärten vorzubereiten.
Bei einigen Produkten ist die Normalisierung keine vorläufige, sondern eine abschließende Wärmebehandlung. In diesem Fall wird das Produkt nach der Normalisierung einer hohen Temperierung unterzogen, um innere Spannungen abzubauen, die durch Abkühlen des Produkts an Luft erzeugt werden.
Die Wärmebehandlung von Legierungen ist ein wesentlicher Bestandteil des Herstellungsprozesses der Eisen- und Nichteisenmetallurgie. Durch dieses Verfahren können Metalle ihre Eigenschaften auf die erforderlichen Werte ändern. In diesem Artikel werden die wichtigsten Arten der Wärmebehandlung in der modernen Industrie betrachtet.
Die Essenz der Wärmebehandlung
Bei der Herstellung werden Halbzeuge und Metallteile einer Wärmebehandlung unterzogen, um ihnen die gewünschten Eigenschaften (Festigkeit, Korrosions- und Verschleißfestigkeit usw.) zu verleihen. Die Wärmebehandlung von Legierungen ist eine Reihe künstlich erzeugter Prozesse, bei denen strukturelle und physikalisch-mechanische Veränderungen in Legierungen unter dem Einfluss hoher Temperaturen auftreten, wobei jedoch die chemische Zusammensetzung des Stoffes erhalten bleibt.
Zweck der Wärmebehandlung
Metallprodukte, die täglich in allen Bereichen der Volkswirtschaft verwendet werden, müssen die hohen Anforderungen an die Verschleißfestigkeit erfüllen. Metall als Rohstoff muss durch die erforderlichen Betriebseigenschaften verstärkt werden, die durch Einwirkung hoher Temperaturen erreicht werden können. Die Wärmebehandlung von Legierungen verändert die Ausgangsstruktur eines Stoffes, verteilt seine Bestandteile neu und verändert die Größe und Form von Kristallen. All dies führt zu einer Minimierung der inneren Spannung des Metalls und erhöht somit seine physikalischen und mechanischen Eigenschaften.
Arten der Wärmebehandlung
Die Wärmebehandlung von Metalllegierungen besteht aus drei einfachen Prozessen: Erhitzen des Rohmaterials (Halbzeug) auf die gewünschte Temperatur, Halten unter bestimmten Bedingungen für die erforderliche Zeit und schnelles Abkühlen. In der modernen Produktion werden verschiedene Arten der Wärmebehandlung verwendet, die sich in einigen technologischen Merkmalen unterscheiden, aber der Prozessalgorithmus bleibt im Allgemeinen überall gleich.
Durch das Verfahren zur Herstellung der Wärmebehandlung werden von den folgenden Arten:
- Thermisch (Härten, Anlassen, Tempern, Altern, Kryobehandlung).
- Thermomechanisch umfasst eine Hochtemperaturbehandlung in Kombination mit einer mechanischen Wirkung auf die Legierung.
- Chemisch-thermisch beinhaltet die Wärmebehandlung von Metall mit anschließender Anreicherung der Oberfläche des Produkts mit chemischen Elementen (Kohlenstoff, Stickstoff, Chrom usw.).
Glühen
Das Tempern ist ein Produktionsprozess, bei dem Metalle und Legierungen auf eine vorbestimmte Temperatur erhitzt werden und dann zusammen mit dem Ofen, in dem das Verfahren stattgefunden hat, auf natürliche Weise sehr natürlich abkühlen. Durch das Tempern ist es möglich, Inhomogenitäten in der chemischen Zusammensetzung des Stoffes zu beseitigen, innere Spannungen abzubauen, eine körnige Struktur zu erreichen und diese als solche zu verbessern sowie die Härte der Legierung zu verringern, um ihre weitere Verarbeitung zu erleichtern. Es gibt zwei Arten der ersten und zweiten Art.
Das Tempern der ersten Art beinhaltet eine Wärmebehandlung, wodurch Änderungen im Phasenzustand der Legierung unbedeutend sind oder überhaupt nicht vorhanden sind. Es hat auch seine eigenen Sorten: homogenisiert - die Glühtemperatur beträgt 1100-1200, unter solchen Bedingungen können die Legierungen 8-15 Stunden standhalten, das Rekristallisationsglühen (bei t 100-200) wird für genieteten Stahl verwendet, dh verformt, der bereits kalt ist.
Das Tempern der zweiten Art führt zu signifikanten Phasenänderungen in der Legierung. Es hat auch mehrere Sorten:
- Vollglühen - Erhitzen der Legierung 30-50 über die kritische Temperaturkennlinie für einen bestimmten Stoff und Abkühlen mit einer bestimmten Geschwindigkeit (200 / Stunde - Kohlenstoffstähle, 100 / Stunde und 50 / Stunde - niedriglegierte bzw. hochlegierte Stähle).
- Unvollständig - Erwärmen auf einen kritischen Punkt und langsames Abkühlen.
- Diffusionsglühtemperatur 1100-1200.
- Die isotherme Erwärmung erfolgt auf die gleiche Weise wie beim vollständigen Tempern. Danach wird jedoch schnell auf eine Temperatur abgekühlt, die etwas unter dem kritischen Wert liegt, und an der Luft abkühlen gelassen.
- Normalisiert - vollständiges Tempern, gefolgt von Abkühlen des Metalls an der Luft und nicht in einem Ofen.
Abschrecken
Das Abschrecken ist die Manipulation einer Legierung, deren Zweck darin besteht, eine martensitische Umwandlung eines Metalls zu erreichen, wodurch eine Verringerung der Duktilität des Produkts und eine Erhöhung seiner Festigkeit sichergestellt wird. Beim Abschrecken und Tempern wird das Metall im Ofen über die kritische Temperatur auf die Abschrecktemperatur erhitzt. Der Unterschied ist die größere Abkühlrate, die im Bad mit der Flüssigkeit auftritt. Je nach Metall und sogar seiner Form werden verschiedene Arten der Härtung angewendet:
- Abschrecken in einem Medium, dh im selben Bad mit Flüssigkeit (Wasser - für große Teile, Öl - für kleine Teile).
- Das intermittierende Abschrecken erfolgt in zwei aufeinander folgenden Schritten: zuerst in einer Flüssigkeit (schärferer Kühler) auf eine Temperatur von etwa 300 ° C, dann an der Luft oder in einem anderen Bad mit Öl.
- Schrittweise - Wenn das Produkt die Abschrecktemperatur erreicht, wird es einige Zeit in geschmolzenen Salzen abgekühlt und anschließend an der Luft abgekühlt.
- Isotherm - laut Technologie ist es der Stufenhärtung sehr ähnlich, es unterscheidet sich nur in der Einwirkzeit des Produkts bei der Temperatur der martensitischen Umwandlung.
- Das Härten mit Selbsttemperation unterscheidet sich von anderen Typen dadurch, dass das erhitzte Metall nicht vollständig abgekühlt ist und ein warmer Abschnitt in der Mitte des Teils verbleibt. Infolge einer solchen Manipulation erhält das Produkt die Eigenschaften einer erhöhten Festigkeit auf der Oberfläche und einer hohen Viskosität in der Mitte. Diese Kombination ist für Schlaginstrumente (Hämmer, Meißel usw.) unerlässlich.)
Urlaub
Der Urlaub ist die letzte Stufe der Wärmebehandlung von Legierungen, die die endgültige Struktur des Metalls bestimmt. Der Hauptzweck des Temperns besteht darin, die Zerbrechlichkeit eines Metallprodukts zu verringern. Das Prinzip besteht darin, das Teil auf eine Temperatur unter kritisch und kühl zu erwärmen. Da die Arten der Wärmebehandlung und die Abkühlgeschwindigkeit von Metallprodukten für verschiedene Zwecke unterschiedlich sein können, gibt es drei Arten des Anlassens:
- Hohe Heiztemperatur von 350-600 bis zu einem Wert unter kritisch. Dieses Verfahren wird am häufigsten für Metallstrukturen verwendet.
- Mittlere Wärmebehandlung bei t 350-500, üblich für Federprodukte und Federn.
- Niedrig - Die Temperatur des Produkts, die nicht höher als 250 ° C ist, ermöglicht eine hohe Festigkeit und Verschleißfestigkeit der Teile.
Altern
Altern ist die Wärmebehandlung von Legierungen, die nach dem Abschrecken die Zersetzung eines übersättigten Metalls bewirkt. Das Ergebnis der Alterung ist eine Erhöhung der Härte, Streckgrenze und Festigkeit des Endprodukts. Nicht nur Gusseisen ist Alterung ausgesetzt, sondern auch leicht verformbare Aluminiumlegierungen. Wenn das zu härtende Metallprodukt auf normaler Temperatur gehalten wird, treten darin Prozesse auf, die zu einer spontanen Zunahme der Festigkeit und einer Abnahme der Duktilität führen. Dies wird als natürliche Alterung des Metalls bezeichnet. Wenn die gleiche Manipulation unter Bedingungen erhöhter Temperatur durchgeführt wird, spricht man von künstlicher Alterung.
Kryogene Behandlung
Änderungen in der Struktur von Legierungen und damit ihren Eigenschaften können nicht nur hoch, sondern auch extrem erreicht werden niedrige Temperaturen. Die Wärmebehandlung von Legierungen bei t unter Null wird als kryogen bezeichnet. Diese Technologie wird in verschiedenen Bereichen der Volkswirtschaft häufig als Ergänzung zu Wärmebehandlungen mit hohen Temperaturen eingesetzt, da sie die Kosten für wärmehärtende Produkte erheblich senken kann.
Die kryogene Verarbeitung von Legierungen wird bei t -196 in einem speziellen kryogenen Prozessor durchgeführt. Diese Technologie kann die Lebensdauer des bearbeiteten Teils und die Korrosionsschutzeigenschaften erheblich erhöhen und die Notwendigkeit wiederholter Behandlungen beseitigen.
Thermomechanische Behandlung
Ein neues Verfahren zur Verarbeitung von Legierungen kombiniert die Verarbeitung von Metallen bei hohen Temperaturen mit der mechanischen Verformung von Produkten in plastischem Zustand. Es gibt drei Arten der thermomechanischen Verarbeitung (TMT) nach der Inbetriebnahmemethode:
- Niedertemperatur-TMT besteht aus zwei Stufen: plastische Verformung mit anschließendem Härten und Anlassen des Teils. Der Hauptunterschied zu anderen TMT-Typen ist die Erwärmungstemperatur auf den austenitischen Zustand der Legierung.
- Bei Hochtemperatur-TMT wird die Legierung in Kombination mit plastischer Verformung auf einen martensitischen Zustand erhitzt.
- Vorverformung wird bei t 20 mit anschließendem Abschrecken und Anlassen des Metalls durchgeführt.
Chemische Wärmebehandlung
Mit Hilfe einer chemisch-thermischen Behandlung, bei der thermische und chemische Effekte auf Metalle kombiniert werden, können Struktur und Eigenschaften von Legierungen verändert werden. Das ultimative Ziel dieses Verfahrens besteht nicht nur darin, dem Produkt eine erhöhte Festigkeit, Zähigkeit und Verschleißfestigkeit zu verleihen, sondern auch darin, dem Teil Säure- und Feuerbeständigkeit zu verleihen. Diese Gruppe umfasst die folgenden Arten der Wärmebehandlung:
- Die Zementierung wird durchgeführt, um der Oberfläche des Produkts zusätzliche Festigkeit zu verleihen. Die Essenz des Verfahrens besteht darin, das Metall mit Kohlenstoff zu sättigen. Die Zementierung kann auf zwei Arten durchgeführt werden: Fest- und Gaszementierung. Im ersten Fall wird das verarbeitete Material zusammen mit Kohle und seinem Aktivator in einen Ofen gegeben und auf eine bestimmte Temperatur erhitzt, gefolgt von seiner Einwirkung dieses Mediums und Abkühlen. Bei der Gaszementierung wird das Produkt im Ofen unter einem kontinuierlichen Strom kohlenstoffhaltigen Gases auf 900 ° C erhitzt.
- Nitrieren ist die chemisch-thermische Behandlung von Metallprodukten durch Sättigung ihrer Oberfläche in Stickstoffmedien. Das Ergebnis dieses Verfahrens ist die Erhöhung der Zugfestigkeit des Teils und die Erhöhung seiner Korrosionsbeständigkeit.
- Cyanidierung - gleichzeitige Sättigung eines Metalls mit Stickstoff und Kohlenstoff. Das Medium kann flüssig (geschmolzene Kohlenstoff- und Stickstoffsalze) und gasförmig sein.
- Die Diffusionsmetallisierung ist eine moderne Methode, um Metallprodukten Wärmebeständigkeit, Säurebeständigkeit und Verschleißfestigkeit zu verleihen. Die Oberfläche solcher Legierungen ist mit verschiedenen Metallen (Aluminium, Chrom) und Metalloiden (Silizium, Bor) gesättigt.
Merkmale der Wärmebehandlung von Gusseisen
Gusseisenlegierungen werden mit einer etwas anderen Technologie als Nichteisenmetalllegierungen wärmebehandelt. Gusseisen (grau, hochfest, legiert) wird folgenden Wärmebehandlungen unterzogen: Glühen (bei t 500-650 -), Normalisieren, Härten (kontinuierlich, isotherm, Oberfläche), Anlassen, Nitrieren (Grauguss), Aluminieren (perlitisches Gusseisen), Verchromen. Alle diese Verfahren verbessern infolgedessen die Eigenschaften der endgültigen Gusseisenprodukte erheblich: Erhöhen Sie die Lebensdauer, beseitigen Sie die Wahrscheinlichkeit von Rissen bei der Verwendung des Produkts und erhöhen Sie die Festigkeit und Wärmebeständigkeit von Gusseisen.
Wärmebehandlung von Nichteisenlegierungen
Nichteisenmetalle und Legierungen haben hervorragende Eigenschaften und werden daher nach unterschiedlichen Methoden verarbeitet. Daher werden Kupferlegierungen einem Rekristallisationsglühen unterzogen, um die chemische Zusammensetzung auszugleichen. Die Technologie des Niedertemperaturglühens (200-300) ist für Messing vorgesehen, da diese Legierung in feuchter Umgebung zu spontanen Rissen neigt. Bronze wird bei t bis zu 550 homogenisiert und getempert. Magnesium wird geglüht, gehärtet und künstlich gealtert (natürliches Altern tritt bei gehärtetem Magnesium nicht auf). Aluminium wird wie Magnesium drei Wärmebehandlungsmethoden unterzogen: Glühen, Härten und Altern, wonach geschmiedete Aluminiumlegierungen ihre Festigkeit erheblich erhöhen. Die Verarbeitung von Titanlegierungen umfasst: Abschrecken, Altern, Nitrieren und Zementieren.
Zusammenfassung
Die Wärmebehandlung von Metallen und Legierungen ist das wichtigste technologische Verfahren sowohl in der Eisen- als auch in der Nichteisenmetallurgie. Moderne Technologien verfügen über viele Wärmebehandlungsmethoden, mit denen Sie die gewünschten Eigenschaften für jede Art von verarbeiteten Legierungen erzielen können. Jedes Metall hat seine eigene kritische Temperatur, was bedeutet, dass eine Wärmebehandlung unter Berücksichtigung der strukturellen und physikalisch-chemischen Eigenschaften des Stoffes durchgeführt werden sollte. Dies führt letztendlich nicht nur zu den gewünschten Ergebnissen, sondern rationalisiert auch die Produktionsprozesse erheblich.