Sejenis rawatan haba keluli, logam dan aloi. Jenis rawatan haba logam
Rawatan haba logam
Tetapi untuk operasi lanjut bahagian dan komponen peralatan, ciri-ciri yang sama sekali berbeza sering diperlukan - kekuatan, kekerasan, ketegaran, dll. Ia adalah untuk tujuan ini bahawa rawatan haba logam bertujuan.
Intipati proses rawatan haba
Objektif pelbagai teknologi rawatan haba adalah:
- Memastikan struktur mikro keluli dan aloi yang paling baik;
- Mendapatkan tahap kekerasan yang diperlukan: sama ada dalam zon permukaan (atau bawah permukaan) nipis, atau pada keseluruhan keratan rentas bahan kerja;
- Pembetulan komposisi kimia dalam butiran makrostruktur pelbagai aloi.
Dalam kes pertama, adalah perlu untuk memastikan tahap kehomogenan maksimum sifat-sifat logam, yang penting, sebagai contoh, untuk pemprosesan mekanikal atau - terutamanya - yang mengubah bentuknya. Akibatnya, syarat untuk menukar bentuk bahan kerja di sepanjang ketiga-tiga paksi koordinat adalah sama, dan penolakan bahagian akhir dihapuskan.
Di samping itu, penjajaran mikro dan makrostruktur untuk proses pembentukan logam adalah perlu untuk meningkatkan tahap ubah bentuk produk separuh siap, akhirnya membawa bentuk bahan kerja lebih dekat dengan bentuk produk siap. Lebih-lebih lagi, dalam bilangan peralihan terkecil, dan menggunakan usaha peralatan minimum yang diperlukan.
Perubahan dalam kekerasan (akibat rawatan haba) bertujuan untuk meningkatkan prestasi bahagian. Oleh kerana keadaan operasi boleh sangat berbeza, kompleks sifat fizikal dan mekanikal dipilih secara ketat secara individu: tiada proses rawatan haba universal untuk aloi dengan komposisi yang berbeza.
Perubahan dalam komposisi kimia dalam butiran mikrostruktur, disebabkan oleh pembentukan sebatian baru, dalam kebanyakan kes bukan sahaja meningkatkan penunjuk kekerasan, tetapi juga meningkatkan rintangan haus bahagian yang mesti dikendalikan pada peningkatan geseran, suhu, atau meningkatkan beban tertentu berbanding biasa.
Quenching-tempering
Kumpulan pertama teknologi rawatan haba untuk pelbagai aloi, termasuk keluli, termasuk penyepuhlindapan dan pembajaan. Yang kedua ialah pengerasan, normalisasi, peningkatan, penuaan, rawatan sejuk. Ketiga - semua jenis rawatan termokimia.
Penyepuhlindapan
Intipati proses yang berlaku dalam struktur kebanyakan aloi yang tertakluk kepada penyepuhlindapan adalah untuk menyediakan struktur yang paling seimbang bagi bahan kerja, di mana sama ada tiada tegasan dalaman, atau tahapnya cukup rendah, dan oleh itu tidak menjejaskan kebolehkerjaan berikutnya. daripada logam/aloi.
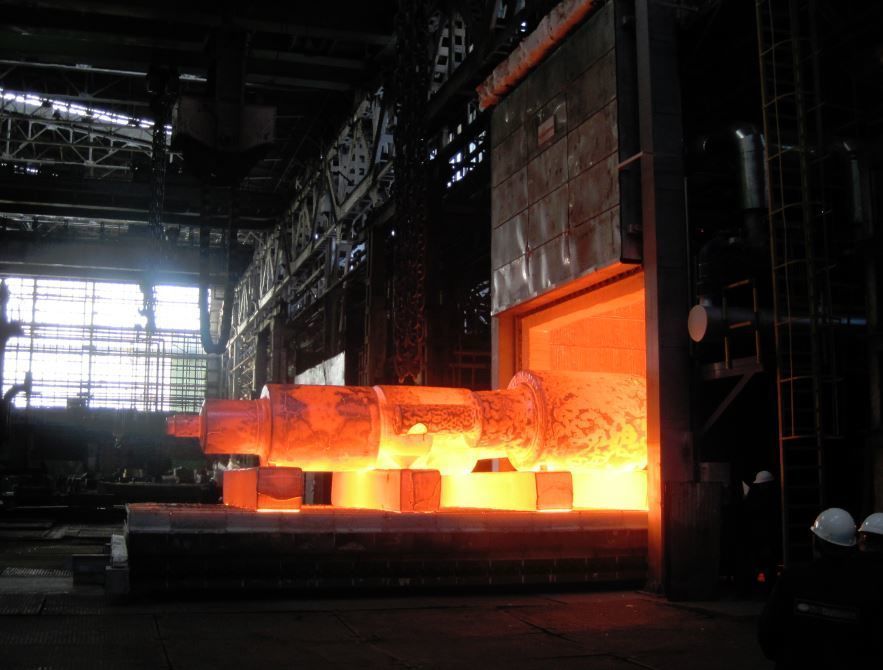
Struktur awal hampir semua aloi dan keluli terdiri daripada butiran yang agak besar, di antaranya terdapat kemasukan dan kekotoran, terutamanya sulfur dan fosforus. Ini meningkatkan kerapuhan logam, yang boleh menjadi penting apabila membentuk produk konfigurasi kompleks daripada jongkong (atau rod dawai). Oleh itu, adalah perlu untuk mengurangkan saiz butiran dan memberikannya bentuk ellipsoidal yang optimum, di mana sifat mekanikal akan lebih kurang sama di sepanjang ketiga-tiga paksi koordinat.
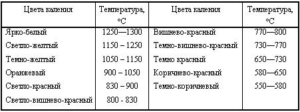
Untuk tujuan ini, bahan kerja awal mesti dipanaskan pada suhu 50...70 0 C di atas suhu di mana penjelmaan austenit bermula. Hasilnya ialah pembentukan butiran austenit yang kecil dan berorientasikan baik di antara butiran komponen struktur utama keluli - ferit dan simentit. Austenit terbentuk daripada pearlit, struktur yang mempunyai bijirin terbesar, yang menyumbang kepada peningkatan kerapuhan mana-mana jongkong. Transformasi austenit untuk kebanyakan aloi berjalan agak perlahan, jadi penyepuhlindapan adalah prosedur yang panjang yang harus berlangsung sekurang-kurangnya satu jam.

Tugas penting kedua penyepuhlindapan adalah untuk melegakan tekanan dalaman yang terbentuk dalam bahan kerja semasa pemprosesan sejuk. Hakikatnya ialah sebarang ubah bentuk disertai dengan pemecahan butiran struktur asal keluli dan aloi. Akibatnya, terdapat lebih banyak bijirin, rintangan terhadap ubah bentuk meningkat, yang bukan sahaja memerlukan peningkatan daya ubah bentuk, tetapi juga menyebabkan kemusnahan produk separuh siap, tahap ubah bentuk yang telah melebihi nilai kritikal untuk logam tertentu. .
Oleh itu, untuk melaksanakan tugas pertama, teknologi penyepuhlindapan suhu tinggi digunakan (untuk keluli, bergantung pada kandungan karbon, ia berkisar antara 550...750 0 C), dan dalam kedua - penyepuhlindapan suhu rendah (180.. .220 0 C).
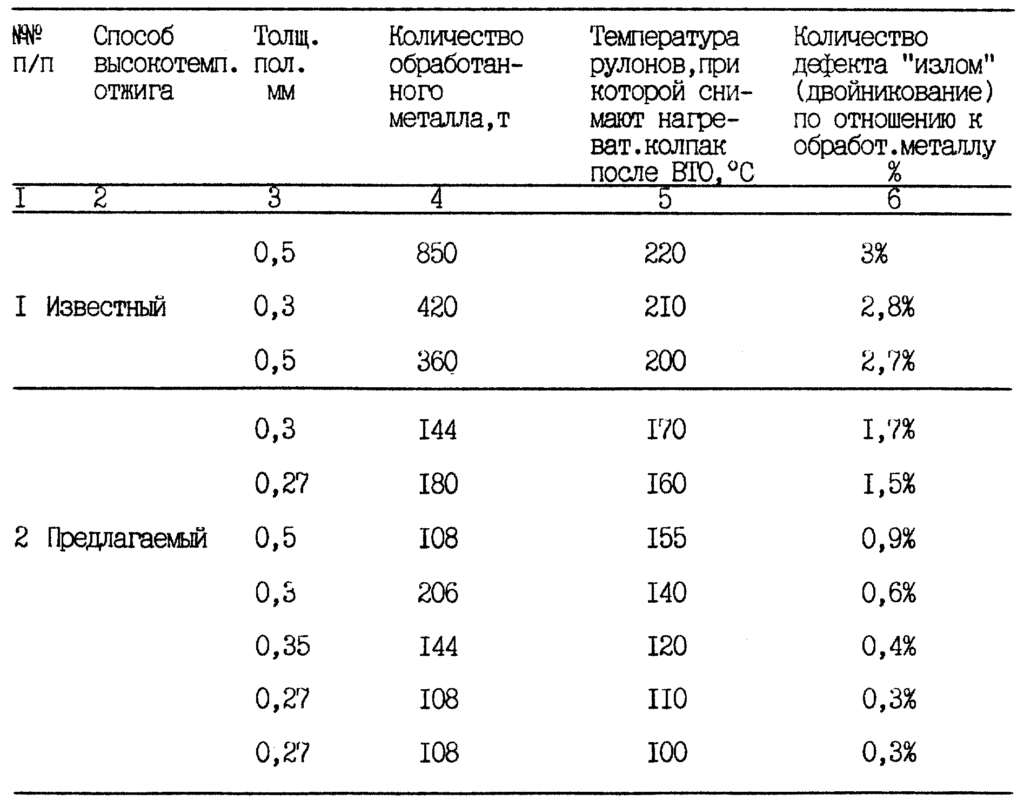
Pemanasan berlaku secara perlahan, diikuti dengan menahan produk pada suhu tertentu, diikuti dengan penyejukan perlahan. Untuk keluli aloi dan aloi, penyejukan sedemikian dilakukan pada kelajuan yang sangat rendah, di dalam relau itu sendiri di mana penyepuhlindapan berlaku.
bercuti
Teknologi pembajaan menyerupai penyepuhlindapan, tetapi dilakukan bukan dengan bahan kerja, tetapi dengan produk siap, dan oleh itu mempunyai matlamat lain - untuk melegakan tekanan dalaman selepas rawatan haba, yang dijalankan untuk meningkatkan kekerasan bahagian.
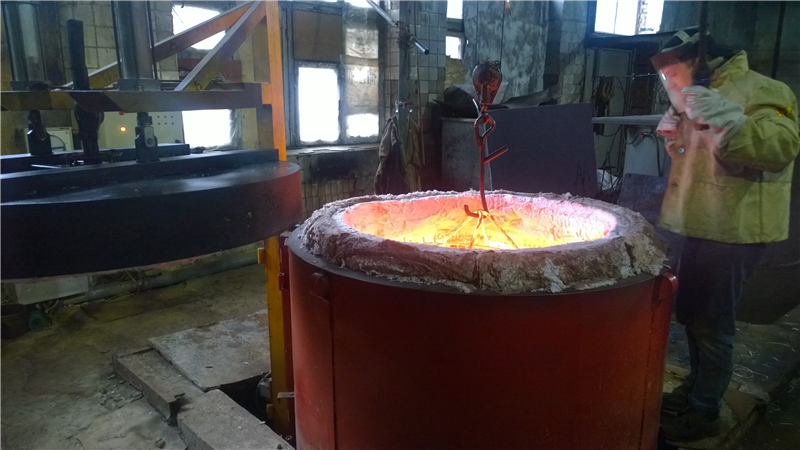
Pembajaan bukan proses rawatan haba bebas. Tidak seperti penyepuhlindapan, pembajaan kadang-kadang dilakukan dalam beberapa peringkat: dalam kebanyakan kes ini terpakai kepada produk untuk pengeluaran yang pelbagai jenis keluli aloi tinggi digunakan.
Pengerasan
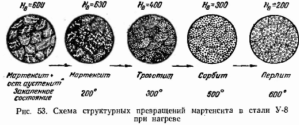
Pengerasan terdiri daripada memanaskan bahan kerja dengan cepat ke suhu akhir penjelmaan austenit (900...1100 0 C untuk keluli karbon rendah, 750...850 0 C untuk keluli karbon tinggi) dan penyejukan pantas seterusnya dalam media pelindapkejutan khas . Yang terakhir adalah air terpakai (untuk produk yang tidak penting) atau minyak.
Mod pengerasan dicirikan oleh kepelbagaian terbesar. Faktor utama yang menentukan keberkesanan pengerasan ialah keamatan pembentukan martensit dalam struktur - komponen suhu tinggi yang memberikan kekerasan logam atau aloi meningkat.
Keadaan untuk pembentukan martensit ditentukan oleh keadaan berikut:
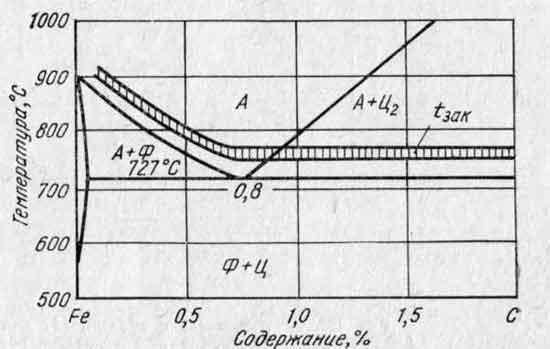
Oleh itu, untuk setiap gred keluli atau aloi, mod pengerasan individu telah dibangunkan, yang berbeza:
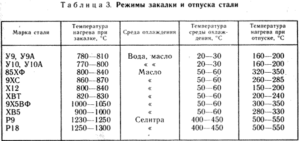
Penjagaan khusus diambil untuk mengeras keluli dan aloi dengan komposisi kompleks, termasuk beberapa unsur pengaloian (khususnya, kobalt, molibdenum). Dalam prosesnya, logam ini membentuk sebatian antara logam di sepanjang sempadan butiran struktur utama, yang meningkatkan kekerasan dan kekuatan keluli dengan ketara (khususnya, keluli alat). Bentuk dan kepekatan sebatian antara logam hanya bergantung pada ketepatan teknologi pengerasan.
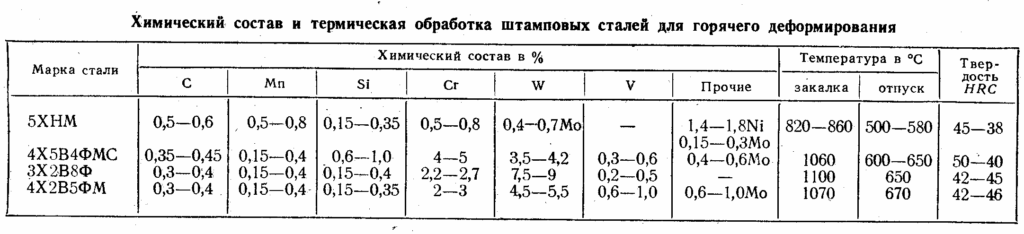
Jenis pengerasan ditentukan oleh peralatan di mana ia dilakukan. Contohnya, untuk produk seperti gear, aci, lajur panduan, di mana kombinasi optimum kekerasan permukaan yang tinggi dan teras yang agak likat diperlukan, pengerasan permukaan dengan arus frekuensi tinggi digunakan.
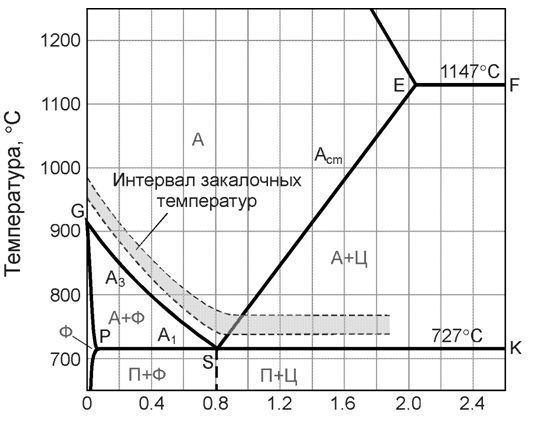
Untuk melakukan ini, produk diletakkan dalam gegelung aruhan yang melaluinya arus frekuensi tinggi (sehingga 15,000...25,000 Hz) dilalui. Menembusi kedalaman yang terhad, arus ini membantu meningkatkan kekuatan permukaan keluli atau aloi. Akibatnya, kekuatan kelesuan bahagian yang beroperasi di bawah tekanan tegangan-tegangan yang berbeza-beza secara kitaran meningkat dengan ketara.
Perubahan yang lebih sengit dalam kekerasan permukaan bahagian boleh diperolehi dengan menggunakan sumber haba tenaga tinggi untuk pengerasan - percikan api atau nyahcas arka. Pelepasan mesti diuja dalam medium cecair di mana bahan kerja atau bahagian yang sedang diproses diletakkan.
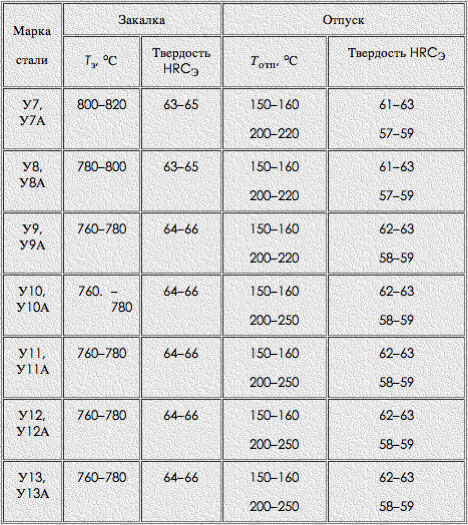
Selepas pengerasan, dalam kebanyakan kes, pembajaan adalah perlu, jika tidak kekerasan akhir bahagian yang berlebihan menjadi punca peningkatan kerapuhan di bawah beban hentaman.
Penambahbaikan dan normalisasi
Sebagai jenis rawatan haba, proses ini serupa dengan penyepuhlindapan, walaupun ia bertujuan untuk tujuan lain - meningkatkan ketahanan operasi bahagian dan alatan mesin kritikal.
Semasa normalisasi, bahagian itu tertakluk kepada pemanasan perlahan, dikekalkan pada suhu tertentu, dan kemudian semestinya disejukkan bersama dengan relau. Akibatnya, struktur bahagian menjadi lebih seimbang, dan tahap tekanan dalaman berkurangan.
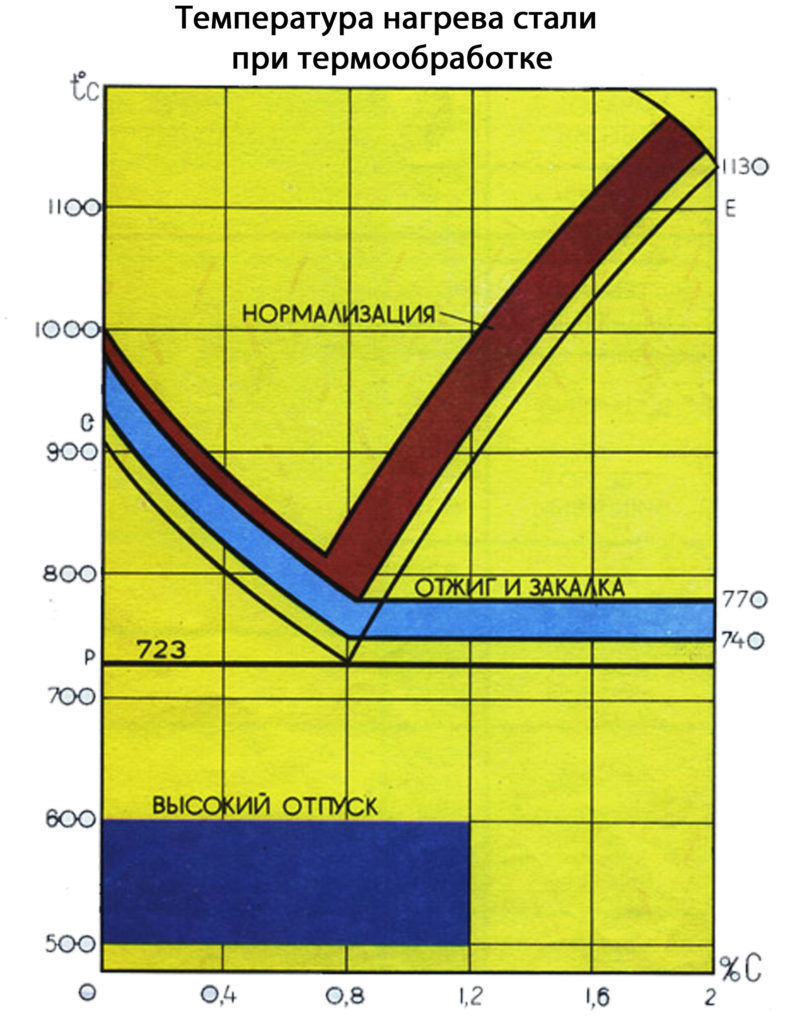
Perbezaan yang ketara ialah komposisi atmosfera, relau di mana operasi rawatan haba ini dijalankan. Ia mestilah tidak mengoksida, kerana pembentukan oksida yang kuat pada permukaan produk bukan sahaja merosot persembahannya, tetapi juga mengubah dimensinya. Pembakaran karbon, yang turut mengiringi rawatan haba dalam relau konvensional, merosot komposisi kimia keluli dan mengurangkan kekuatannya.
Mengurangkan akses oksigen ke permukaan bahagian semasa normalisasi dilakukan dengan beberapa cara:
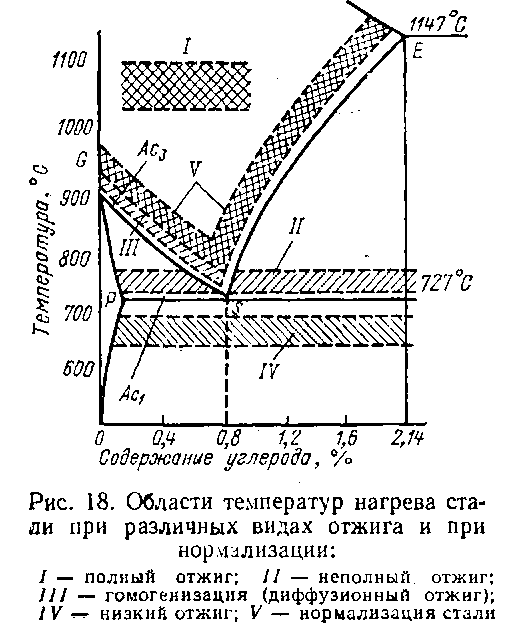
- Dengan pemanasan semasa kekurangan oksigen yang dirancang. Dalam kes ini, kestabilan pembakar gas relau rawatan haba diberi pampasan dengan meningkatkan kelajuan bekalan udara ke zon pembakaran;
- Rawatan haba dalam persekitaran gas pelindung. Untuk bahagian kritikal, wap litium, argon atau gas mulia lain digunakan, dalam kes lain - karbon dioksida;
- Dengan menggunakan salutan pelindung pada permukaan produk yang akan dinormalisasi.
Selepas normalisasi, bahagian itu disejukkan dalam udara pegun, menghalangnya daripada bertiup: ini boleh menyebabkan struktur mikro produk yang tidak seragam dan "berbintik-bintik".
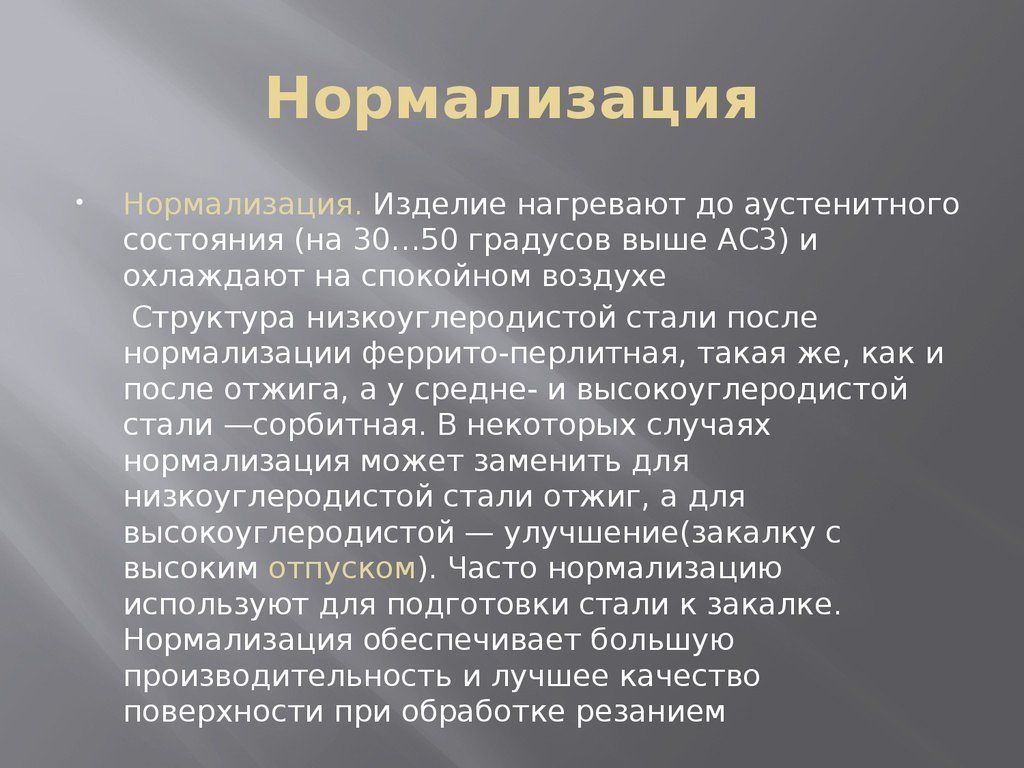
Penambahbaikan ialah operasi rawatan haba, akibatnya kebolehkerjaan mekanikal keluli dan aloi meningkat dan tahap tegasan baki di dalamnya berkurangan. Ini disertai dengan sedikit penurunan kekerasan.
Komponen martensit dalam struktur kebanyakan keluli dan aloi boleh muncul bukan sahaja pada suhu tinggi, tetapi juga pada suhu rendah. Teknologi rawatan sejuk membandingkan dengan baik dengan teknologi rawatan haba tradisional dengan cara berikut:
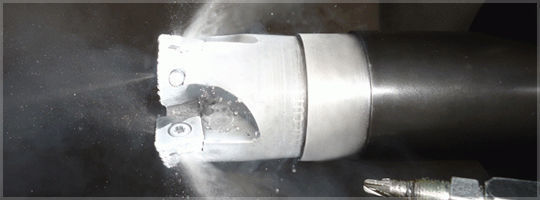
Mod pemprosesan kriogenik bergantung pada gred keluli/aloi, dan berjulat dari -60...-140 0 C. Biasanya, pemprosesan kriogenik dijalankan dengan gabungan kitaran tempoh penyejukan dalam dengan tempoh penuaan - pendedahan pada suhu yang lebih rendah . Dengan gabungan kitaran pemanasan dan penyejukan, penguraian lengkap austenit tertahan dicapai dalam 4...7 jam (nilai yang lebih tinggi untuk keluli aloi tinggi).
Jenis rawatan haba khas diwakili oleh proses rawatan kimia-terma. Tugas mereka adalah untuk membentuk karbida dan nitrida dalam struktur mikro permukaan - sebatian yang meningkatkan kekerasan mikro bahagian dengan ketara dan mewujudkan tegasan mampatan sisa di dalamnya. Produk sedemikian menunjukkan rintangan yang tinggi terutamanya di bawah beban berselang-seli.
Video: Bagaimana untuk mengeras mana-mana gred keluli
AU CR NPO “Sekolah Vokasional No. 22”
Esei
atas perkara " Sains Bahan »
mengenai topik: " Rawatan haba logam dan aloi »
Selesai:
pelajar kumpulan "DSM-01-11"
Morozov I.V.
Disemak oleh: cikgu
Grigoreva E.V.
Kanash 2011
Kandungan
Pendahuluan…………………………………………………………………………………………….3 muka surat
Tujuan dan jenis rawatan haba..…………………………………….…4-9 muka surat
Tujuan dan jenis rawatan kimia-terma……………………..…10-15 muka suratRawatan haba bagi aloi logam bukan ferus……………………...15-18 muka surat
Kesimpulan……………………………………………………………………………..muka surat 19
Kesusasteraan……………………………………………………………………………..muka surat 20
pengenalan
Rawatan haba digunakan pada pelbagai peringkat pengeluaran bahagian mesin dan produk logam. Dalam sesetengah kes, ia boleh menjadi operasi perantaraan yang berfungsi untuk meningkatkan kebolehmesinan aloi dengan tekanan dan pemotongan; dalam yang lain, operasi akhir yang menyediakan set penunjuk yang diperlukan bagi sifat mekanikal, fizikal dan operasi produk atau separa. -produk akhir. Produk separuh siap dikenakan rawatan haba untuk memperbaiki struktur, mengurangkan kekerasan (kebolehkerjaan yang lebih baik), dan bahagian - untuk memberikan sifat tertentu yang diperlukan (kekerasan, rintangan haus, kekuatan, dan lain-lain).
Hasil daripada rawatan haba, sifat aloi boleh diubah dalam had yang luas. Kemungkinan meningkatkan sifat mekanikal dengan ketara selepas rawatan haba berbanding dengan keadaan awal memungkinkan untuk meningkatkan tegasan yang dibenarkan, mengurangkan saiz dan berat mesin dan mekanisme, dan meningkatkan kebolehpercayaan dan hayat perkhidmatan produk. Memperbaiki sifat akibat rawatan haba membolehkan penggunaan aloi komposisi yang lebih mudah, dan oleh itu lebih murah. Aloi juga memperoleh beberapa sifat baru, dan oleh itu skop penggunaannya berkembang.
Tujuan dan jenis rawatan haba
Rawatan terma (haba) ialah satu proses yang intipatinya terletak pada pemanasan dan penyejukan produk mengikut mod tertentu, mengakibatkan perubahan dalam struktur, komposisi fasa, mekanikal dan ciri-ciri fizikal bahan, tanpa mengubah komposisi kimia.
Tujuan rawatan haba logam adalah untuk mendapatkan kekerasan yang diperlukan dan meningkatkan ciri kekuatan logam dan aloi. Rawatan haba dibahagikan kepada terma, termomekanikal dan kimia-terma. Rawatan haba hanya pendedahan haba, termomekanikal adalah gabungan pendedahan haba dan ubah bentuk plastik, kimia-terma adalah gabungan pendedahan haba dan kimia. Rawatan haba, bergantung kepada keadaan struktur yang diperoleh hasil daripada penggunaannya, dibahagikan kepada penyepuhlindapan (jenis pertama dan kedua), pengerasan dan pembajaan.
Penyepuhlindapan
Penyepuhlindapan ialah rawatan haba yang terdiri daripada memanaskan logam pada suhu tertentu, menahannya dan kemudian menyejukkannya dengan sangat perlahan bersama dengan relau. Digunakan untuk memperbaiki pemotongan logam, mengurangkan kekerasan, mendapatkan struktur bijian, dan juga untuk melegakan tekanan, menghapuskan sebahagian (atau sepenuhnya) semua jenis ketidakhomogenan yang dimasukkan ke dalam logam semasa operasi sebelumnya (pemesinan, rawatan tekanan, tuangan, kimpalan), memperbaiki struktur keluli.
Penyepuhlindapan jenis pertama. Ini adalah penyepuhlindapan di mana tiada transformasi fasa berlaku, dan jika ia berlaku, ia tidak menjejaskan keputusan akhir yang dimaksudkan untuk tujuan yang dimaksudkan. Jenis penyepuhlindapan jenis pertama berikut dibezakan: homogenisasi dan penghabluran semula.
Homogenisasi adalah penyepuhlindapan dengan pendedahan yang lama pada suhu melebihi 950°C (biasanya 1100–1200°C) untuk menyamakan komposisi kimia.
Penghabluran semula ialah penyepuhlindapan keluli yang dikeraskan pada suhu melebihi suhu di mana penghabluran semula bermula, untuk menghapuskan pengerasan dan mendapatkan saiz butiran tertentu.
Penyepuhlindapan jenis kedua. Ini adalah penyepuhlindapan, di mana transformasi fasa menentukannya tujuan khas. Jenis berikut dibezakan: lengkap, tidak lengkap, resapan, isoterma, ringan, normal (normalisasi), spheroidizing (untuk perlit berbutir).
Penyepuhlindapan penuh dilakukan dengan memanaskan keluli 30–50 °C di atas titik kritikal, menahan pada suhu ini dan perlahan-lahan menyejukkan kepada 400–500 °C pada kadar 200 °C sejam untuk keluli karbon, 100 °C sejam untuk keluli aloi rendah dan 50 °C sejam untuk keluli aloi tinggi. Struktur keluli selepas penyepuhlindapan adalah keseimbangan dan stabil.
Penyepuhlindapan separa dijalankan dengan memanaskan keluli kepada salah satu suhu yang terletak dalam julat transformasi, memegang dan menyejukkan perlahan. Penyepuhlindapan separa digunakan untuk mengurangkan tekanan dalaman, mengurangkan kekerasan dan meningkatkan kebolehmesinan.
Penyepuhlindapan resapan. Logam dipanaskan pada suhu 1100–1200°C, kerana dalam kes ini proses resapan yang diperlukan untuk menyamakan komposisi kimia berlaku dengan lebih lengkap.
Penyepuhlindapan isoterma terdiri daripada yang berikut: keluli dipanaskan dan kemudian disejukkan dengan cepat (biasanya dengan memindahkannya ke relau lain) ke suhu di bawah suhu kritikal sebanyak 50–100? C. Terutamanya digunakan untuk keluli aloi. Berfaedah dari segi ekonomi, kerana tempoh penyepuhlindapan konvensional ialah (13 – 15) jam, dan penyepuhlindapan isoterma (4 – 6) jam
Penyepuhlindapan spheroidizing (untuk pearlit berbutir) melibatkan pemanasan keluli di atas suhu kritikal sebanyak 20–30 °C, menahannya pada suhu ini dan menyejukkannya perlahan-lahan.
Penyepuhlindapan terang dilakukan mengikut mod penyepuhlindapan lengkap atau tidak lengkap menggunakan atmosfera pelindung atau dalam relau dengan vakum separa. Ia digunakan untuk melindungi permukaan logam daripada pengoksidaan dan penyahkarbonan.
Normalisasi melibatkan pemanasan logam pada suhu (30–50) °C di atas takat kritikal dan kemudian menyejukkannya di udara. Tujuan normalisasi berbeza-beza bergantung pada komposisi keluli. Daripada penyepuhlindapan, keluli karbon rendah dinormalisasi. Untuk keluli karbon sederhana, normalisasi digunakan dan bukannya pengerasan dan pembajaan tinggi. Keluli karbon tinggi tertakluk kepada normalisasi untuk menghapuskan rangkaian simentit. Normalisasi diikuti dengan pembajaan tinggi digunakan dan bukannya penyepuhlindapan untuk membetulkan struktur keluli aloi. Normalisasi, berbanding dengan penyepuhlindapan, adalah operasi yang lebih menjimatkan, kerana ia tidak memerlukan penyejukan dengan relau.
Pengerasan
Pengerasan ialah pemanasan kepada suhu optimum, pegangan dan penyejukan pantas seterusnya untuk mendapatkan struktur tidak seimbang.
Hasil daripada pengerasan, kekuatan dan kekerasan keluli meningkat dan kemuluran keluli berkurangan. Parameter utama semasa pengerasan adalah suhu pemanasan dan kadar penyejukan. Kadar pelindapkejutan kritikal ialah kadar penyejukan yang memastikan pembentukan struktur - martensit atau martensit dan austenit tertahan.
Bergantung pada bentuk bahagian, gred keluli dan set sifat yang diperlukan, ia digunakan pelbagai cara pengerasan
Pelindapkejutan dalam satu penyejuk. Bahagian itu dipanaskan pada suhu pengerasan dan disejukkan dalam satu penyejuk (air, minyak).
Pelindapkejutan dalam dua persekitaran (pelindapkejutan sekejap) ialah pelindapkejutan di mana bahagian itu disejukkan secara berurutan dalam dua persekitaran: medium pertama ialah penyejuk (air), yang kedua ialah udara atau minyak.
Langkah pengerasan. Bahagian yang dipanaskan kepada suhu pelindapkejutan disejukkan dalam garam cair; selepas menahan masa yang diperlukan untuk menyamakan suhu ke atas keseluruhan keratan rentas, bahagian itu disejukkan di udara, yang membantu mengurangkan tegasan pelindapkejutan.
Pengerasan isoterma, seperti pengerasan langkah, dijalankan dalam dua persekitaran penyejukan. Suhu medium panas (mandi garam, nitrat atau alkali) adalah berbeza: ia bergantung pada komposisi kimia keluli, tetapi sentiasa 20-100 °C di atas titik transformasi martensit untuk keluli tertentu. Penyejukan akhir kepada suhu bilik dijalankan di udara. Pengerasan isoterma digunakan secara meluas untuk bahagian yang diperbuat daripada keluli aloi tinggi. Selepas pengerasan isoterma, keluli memperoleh sifat kekuatan tinggi, iaitu gabungan keliatan dan kekuatan tinggi.
Pengerasan pembajaan diri digunakan secara meluas dalam pengeluaran alat. Proses ini terdiri daripada fakta bahawa bahagian-bahagian itu disimpan dalam medium penyejukan bukan sehingga ia disejukkan sepenuhnya, tetapi pada masa tertentu ia dikeluarkan daripadanya untuk mengekalkan sejumlah haba dalam teras bahagian, disebabkan oleh yang mana pembajaan seterusnya dijalankan.
bercuti
Pembajaan keluli ialah operasi rawatan haba terakhir yang membentuk struktur dan, akibatnya, sifat keluli. Pembajaan terdiri daripada pemanasan keluli kepada suhu yang berbeza (bergantung pada jenis pembajaan, tetapi sentiasa di bawah titik kritikal), menahannya pada suhu ini dan menyejukkan pada kadar yang berbeza. Tujuan pembajaan adalah untuk melegakan tegasan dalaman yang timbul semasa proses pengerasan dan mendapatkan struktur yang diperlukan.
Bergantung pada suhu pemanasan bahagian yang keras, tiga jenis pembajaan dibezakan: tinggi, sederhana dan rendah.
Pembajaan tinggi dilakukan pada suhu pemanasan melebihi 350–600 °C, tetapi di bawah titik kritikal; pembajaan tersebut digunakan untuk keluli struktur.
Pembajaan purata dijalankan pada suhu pemanasan 350 – 500 °C; Pembajaan sedemikian digunakan secara meluas untuk keluli musim bunga dan musim bunga.
Pembajaan rendah dilakukan pada suhu 150–250 °C. Kekerasan bahagian selepas pengerasan kekal hampir tidak berubah; pembajaan rendah digunakan untuk keluli alat karbon dan aloi, yang memerlukan kekerasan tinggi dan rintangan haus.
Kawalan tempering dilakukan dengan warna-warna kotor yang muncul pada permukaan bahagian.
Penuaan
Penuaan ialah proses menukar sifat aloi tanpa perubahan ketara dalam struktur mikro. Dua jenis penuaan diketahui: terma dan ubah bentuk.
Penuaan terma berlaku akibat perubahan dalam keterlarutan karbon dalam besi bergantung kepada suhu.
Sekiranya perubahan dalam kekerasan, kemuluran dan kekuatan berlaku pada suhu bilik, maka penuaan sedemikian dipanggil semula jadi.
Sekiranya proses itu berlaku pada suhu tinggi, maka penuaan dipanggil buatan.
Penuaan terikan (mekanikal) berlaku selepas ubah bentuk plastik sejuk.
Rawatan selsema
Satu jenis rawatan haba baharu untuk meningkatkan kekerasan keluli dengan menukar austenit tertahan keluli keras kepada martensit. Ini dilakukan dengan menyejukkan keluli ke suhu titik martensit yang lebih rendah.
Kaedah pengerasan permukaan
Pengerasan permukaan ialah proses rawatan haba yang melibatkan pemanasan lapisan permukaan keluli kepada suhu melebihi kritikal dan penyejukan seterusnya untuk mendapatkan struktur martensit dalam lapisan permukaan.
Jenis berikut dibezakan: pengerasan aruhan; pengerasan dalam elektrolit, pengerasan apabila dipanaskan dengan arus frekuensi tinggi (HF), pengerasan dengan pemanasan api gas.
Pengerasan induksi adalah berdasarkan fenomena fizikal, intipatinya adalah itu elektrik frekuensi tinggi, melalui konduktor, mencipta medan elektromagnet di sekelilingnya. Arus pusar teraruh pada permukaan bahagian yang diletakkan di medan ini, menyebabkan logam itu panas ke suhu tinggi. Ini membolehkan transformasi fasa berlaku.
Bergantung kepada kaedah pemanasan, pengerasan aruhan dibahagikan kepada tiga jenis:
pemanasan serentak dan pengerasan seluruh permukaan (digunakan untuk bahagian kecil);
pemanasan berurutan dan pengerasan bahagian individu (digunakan untuk aci engkol dan bahagian yang serupa);
pemanasan berurutan berterusan dan pengerasan melalui pergerakan (digunakan untuk bahagian yang panjang).
Pengerasan api gas. Proses pengerasan nyalaan gas terdiri daripada memanaskan dengan cepat permukaan bahagian dengan nyalaan asetilena-oksigen, gas-oksigen atau oksigen-minyak tanah kepada suhu pengerasan, diikuti dengan penyejukan dengan air atau emulsi.
Pelindapkejutan dalam elektrolit. Proses pengerasan dalam elektrolit adalah seperti berikut: bahagian yang akan dikeraskan diturunkan ke dalam tab elektrolit (larutan 5–10% garam terkalsin) dan arus 220–250 V dilalui. Akibatnya, bahagian dipanaskan pada suhu tinggi. Bahagian itu disejukkan sama ada dalam elektrolit yang sama (selepas mematikan arus) atau dalam tangki pelindapkejutan khas.
Rawatan termo-mekanikal
Pemprosesan termomekanikal (T.M.O.) ialah kaedah baharu untuk mengukuhkan logam dan aloi sambil mengekalkan kemuluran yang mencukupi, menggabungkan ubah bentuk plastik dan mengukuhkan rawatan haba (pengerasan dan pembajaan). Terdapat tiga kaedah utama pemprosesan termomekanikal.
Pemprosesan termomekanikal suhu rendah (L.T.M.T.) adalah berdasarkan pengerasan langkah, iaitu, ubah bentuk plastik keluli dilakukan pada suhu kestabilan relatif austenit, diikuti dengan pengerasan dan pembajaan.
Rawatan termomekanikal suhu tinggi (H.T.M.T.), di mana ubah bentuk plastik dilakukan pada suhu kestabilan austenit, diikuti dengan pelindapkejutan dan pembajaan.
Ubah bentuk rawatan termomekanikal awal (P.T.M.O) boleh dilakukan pada suhu N.T.M.O dan V.T.M.O atau pada suhu 20? C. Seterusnya, rawatan haba biasa dijalankan: pengerasan dan pembajaan.
Tujuan dan jenis rawatan kimia-terma
Rawatan kimia-terma ialah proses yang merupakan gabungan kesan haba dan kimia untuk mengubah komposisi, struktur dan sifat lapisan permukaan keluli.
Tujuan rawatan kimia-terma: meningkatkan kekerasan permukaan, rintangan haus, had ketahanan, rintangan kakisan, rintangan haba (rintangan skala), rintangan asid.
Jenis rawatan kimia-terma berikut paling banyak digunakan dalam industri: penyimenan; nitrokarburisasi; nitriding; sianidasi; pemetaan resapan.
Penyimenan ialah proses ketepuan permukaan dengan karbon, dijalankan untuk tujuan pengerasan permukaan bahagian.
Bergantung pada carburizer yang digunakan, carburization terbahagi kepada tiga jenis: carburization with solid carburizer; penyimenan gas (metana, propana, gas asli).
Penyimenan gas. Bahagian dipanaskan hingga 900–950°C dalam relau khas tertutup rapat, di mana penyimenan gas yang mengandungi karbon [semula jadi (semula jadi) atau tiruan] dibekalkan dalam aliran berterusan.
Proses pengkarbonan dalam karburizer pepejal adalah seperti berikut. Bahagian-bahagian, dibungkus dalam kotak bersama-sama dengan karburizer (campuran arang dengan pengaktif), dipanaskan pada suhu tertentu dan disimpan pada suhu ini untuk masa yang lama, kemudian disejukkan dan tertakluk kepada rawatan haba.
Bahagian yang diperbuat daripada keluli karbon dan aloi dengan kandungan karbon tidak lebih daripada 0.2% tertakluk kepada penyimenan oleh mana-mana kaedah yang dibincangkan di atas. Penyimenan keluli aloi yang mengandungi unsur pembentuk karbida Cr, W, V memberi terutamanya keputusan baik: selain meningkatkan kekerasan permukaan dan rintangan haus, had keletihannya juga meningkat.
Nitriding ialah proses penepuan lapisan permukaan pelbagai logam dan aloi, produk keluli atau bahagian dengan nitrogen apabila dipanaskan dalam persekitaran yang sesuai. Kekerasan permukaan produk, ketahanan, rintangan haus, dan rintangan kakisan meningkat.
Sianidasi ialah ketepuan lapisan permukaan produk dengan kedua-dua karbon dan nitrogen.
Bergantung pada medium yang digunakan, sianidasi dibezakan: dalam media pepejal; dalam media cecair; dalam persekitaran gas.
Bergantung pada suhu pemanasan, sianidasi dibahagikan kepada suhu rendah dan suhu tinggi.
Sianidasi dalam media cecair dijalankan dalam mandian garam cair.
Sianidasi dalam media gas (nitrokarburisasi). Proses menepu permukaan bahagian secara serentak dengan karbon dan nitrogen. Untuk melakukan ini, bahagian dipanaskan dalam persekitaran yang terdiri daripada gas penyimenan dan ammonia, iaitu, nitrokarburisasi menggabungkan proses pengkarbonan gas dan nitriding.
Ketepuan resapan dengan logam dan metaloid
Terdapat dan digunakan dalam kaedah industri untuk menepu permukaan bahagian dengan pelbagai logam (aluminium, kromium, dll.) dan metaloid (silikon, boron, dll.). Tujuan ketepuan tersebut adalah untuk meningkatkan rintangan skala, rintangan kakisan , rintangan asid, kekerasan dan rintangan haus bahagian. Akibatnya, lapisan permukaan memperoleh sifat khas, yang membolehkan penjimatan unsur pengaloian.
Aluminizing ialah proses penepuan lapisan permukaan keluli dengan aluminium untuk meningkatkan rintangan haba (rintangan skala) dan ketahanan terhadap kakisan atmosfera.
Aluminisasi dilakukan dalam campuran serbuk, dalam tab mandi dengan aluminium cair, dalam persekitaran gas dan dengan menyembur aluminium cair.
Penyaduran krom ialah proses penepuan lapisan permukaan keluli dengan kromium untuk meningkatkan rintangan kakisan dan rintangan haba, dan apabila penyaduran krom keluli karbon tinggi, untuk meningkatkan kekerasan dan rintangan haus.
Silikonisasi ialah proses penepuan lapisan permukaan bahagian dengan silikon untuk meningkatkan rintangan kakisan dan rintangan asid. Bahagian yang diperbuat daripada keluli karbon rendah dan sederhana, serta besi tuang mulur dan berkekuatan tinggi tertakluk kepada silikonisasi.
Boriding ialah proses menepu lapisan permukaan bahagian dengan boron. Tujuan membosankan adalah untuk meningkatkan kekerasan, ketahanan terhadap haus kasar dan kakisan dalam persekitaran yang agresif, rintangan haba dan rintangan haba bahagian keluli. Terdapat dua kaedah membosankan: elektrolisis cecair dan membosankan gas.
Sulfidasi ialah proses penepuan lapisan permukaan bahagian keluli dengan sulfur untuk memperbaiki sifat tekanan melampau dan meningkatkan rintangan haus bahagian.
Sulfosianasi ialah proses ketepuan permukaan bahagian keluli dengan sulfur, karbon dan nitrogen. Pengaruh gabungan sulfur dan nitrogen dalam lapisan permukaan logam memberikan sifat tekanan ekstrem yang lebih tinggi dan rintangan haus berbanding tepu dengan sulfur sahaja.
Rawatan haba besi tuang
Rawatan haba besi tuang dijalankan untuk melegakan tekanan dalaman yang timbul semasa tuangan dan menyebabkan perubahan dalam saiz dan bentuk tuangan dari semasa ke semasa, mengurangkan kekerasan dan meningkatkan kebolehmesinan, dan meningkatkan sifat mekanikal. Besi tuang tertakluk kepada penyepuhlindapan, penormalan, pelindapkejutan dan pembajaan, serta beberapa jenis rawatan kimia dan haba (nitriding, aluminisasi, penyaduran krom).
Penyepuhlindapan untuk melegakan tekanan dalaman. Besi tuang tertakluk kepada penyepuhlindapan ini pada suhu berikut: besi tuang kelabu dengan grafit kepingan 500 – 570? C; besi tuang berkekuatan tinggi dengan grafit nodular 550 – 650?C; besi tuang aloi rendah 570 – 600?C; besi tuang aloi tinggi 620 – 650?C. Semasa penyepuhlindapan ini transformasi fasa tidak berlaku, tetapi tekanan dalaman dilegakan, kelikatan meningkat, meleding dan retak semasa operasi dihapuskan.
Penyepuhlindapan melembutkan (penyelidikan grafit suhu rendah). Lakukan untuk meningkatkan kebolehmesinan dan meningkatkan kemuluran. Ia dijalankan dengan pendedahan berpanjangan pada 680 - 700? C atau penyejukan perlahan tuangan pada 760 - 700? C. Untuk bahagian dengan konfigurasi kompleks, penyejukan adalah perlahan, dan untuk bahagian dengan bentuk mudah, penyejukan dipercepatkan.
Penyepuhlindapan grafit, yang menghasilkan besi tuang mudah ditempa daripada besi tuang putih.
Normalisasi digunakan untuk meningkatkan karbon tetap, meningkatkan kekerasan, kekuatan dan rintangan haus besi tuang kelabu, mulur dan berkekuatan tinggi. Apabila menormalkan, besi tuang (tuangan) dipanaskan di atas suhu julat transformasi 850 - 950? C dan selepas dipegang, disejukkan di udara.
Besi tuang kelabu, mulur dan mulur dipadamkan untuk meningkatkan kekerasan, kekuatan dan rintangan haus. Mengikut kaedah pelaksanaan, pengerasan besi tuang boleh menjadi isipadu berterusan, isoterma dan permukaan.
Semasa pengerasan berterusan isipadu, besi tuang dipanaskan pada suhu 850 - 950? C. Kemudian ia disimpan untuk memanaskan badan dan melarutkan karbon sepenuhnya. Penyejukan dilakukan dalam air atau minyak. Selepas pengerasan, pembajaan dijalankan pada suhu 200 - 600? C. Akibatnya, kekerasan, kekuatan dan rintangan haus besi tuang meningkat.
Semasa pengerasan isoterma, besi tuang dipanaskan dengan cara yang sama seperti semasa pengerasan berterusan isipadu, dipegang selama 10 hingga 90 minit dan disejukkan dalam garam cair pada suhu 200–400°C, dan selepas dipegang, disejukkan di udara.
Pengerasan permukaan dengan pemanasan lapisan permukaan dengan nyalaan oksigen-asetilena, arus frekuensi tinggi atau dalam elektrolit. Suhu pemanasan 900 – 1000?C. Menyejukkan dalam air, minyak atau emulsi minyak.
Penuaan digunakan untuk menstabilkan dimensi bahagian besi tuang, mencegah meledingkan dan melegakan tekanan dalaman. Biasanya, penuaan dilakukan selepas pemprosesan mekanikal kasar. Terdapat dua jenis penuaan: semulajadi dan buatan.
Penuaan semulajadi berlaku di luar atau di dalam rumah. Produk selepas tuangan berumur 6 – 15 bulan.
Penuaan buatan dilakukan pada suhu tinggi; tempoh - beberapa jam. Semasa penuaan buatan, besi tuang dimuatkan ke dalam relau yang dipanaskan hingga 100 - 200? C, dipanaskan pada suhu 550 - 570? C pada kadar 30 - 60? C sejam, disimpan selama 3 - 5 jam dan disejukkan dengan relau pada kadar 20 - 40? C sejam kepada suhu 150 - 200? C, dan kemudian disejukkan di udara.
Rawatan kimia-terma besi tuang
Untuk meningkatkan kekerasan permukaan dan rintangan haus, besi tuang kelabu tertakluk kepada nitriding. Besi tuang mutiara kelabu yang dialoi dengan kromium, molibdenum dan aluminium paling kerap dinitrida. Suhu nitriding 550 – 580? C, masa penahanan 30 – 70 jam. Sebagai tambahan kepada nitriding, meningkatkan kekerasan permukaan dan rintangan haus besi tuang pearlit kelabu beraloi boleh dicapai dengan gas dan sianidasi cecair pada suhu 570? C. Untuk meningkatkan rintangan haba, tuangan besi tuang boleh tertakluk kepada aluminizing, dan untuk mendapatkan rintangan kakisan yang tinggi dalam asid - silikon.
Rawatan haba aloi logam bukan ferus
Aloi aluminium
Aloi aluminium tertakluk kepada tiga jenis rawatan haba: penyepuhlindapan, pengerasan dan penuaan. Jenis utama penyepuhlindapan ialah: resapan, penghabluran semula dan aloi yang diperkuatkan secara haba.
Homogenisasi digunakan untuk meratakan mikroheterogen kimia bagi butiran larutan pepejal. Untuk melakukan homogenisasi, aloi aluminium dipanaskan hingga 450 - 520? C dan dikekalkan pada suhu ini selama 4 hingga 40 jam; selepas memegang - menyejukkan dengan relau atau di udara. Akibatnya, struktur menjadi lebih homogen dan keplastikan meningkat.
Penyepuhlindapan penghabluran semula digunakan dengan lebih meluas untuk aloi berasaskan aluminium dan aluminium berbanding keluli. Ini dijelaskan oleh fakta bahawa logam seperti aluminium dan tembaga, serta banyak aloi berdasarkannya, tidak diperkuat dengan pengerasan dan peningkatan sifat mekanikal hanya boleh dicapai dengan kerja sejuk, dan operasi perantaraan semasa pemprosesan sedemikian adalah. penyepuhlindapan penghabluran semula. Suhu penyepuhlindapan penghabluran semula aloi aluminium ialah 300 – 500? C, masa penahanan ialah 0.5 – 2 jam.
dan lain-lain.................
mengenai topik: "Rawatan haba logam dan aloi"
pengenalan
Rawatan haba digunakan pada pelbagai peringkat pengeluaran bahagian mesin dan produk logam. Dalam sesetengah kes, ia boleh menjadi operasi perantaraan yang berfungsi untuk meningkatkan kebolehmesinan aloi dengan tekanan dan pemotongan; dalam yang lain, operasi akhir yang menyediakan set penunjuk yang diperlukan bagi sifat mekanikal, fizikal dan operasi produk atau separa. -produk akhir. Produk separuh siap dikenakan rawatan haba untuk memperbaiki struktur, mengurangkan kekerasan (kebolehkerjaan yang lebih baik), dan bahagian - untuk memberikan sifat tertentu yang diperlukan (kekerasan, rintangan haus, kekuatan, dan lain-lain).
Hasil daripada rawatan haba, sifat aloi boleh diubah dalam had yang luas. Kemungkinan meningkatkan sifat mekanikal dengan ketara selepas rawatan haba berbanding dengan keadaan awal memungkinkan untuk meningkatkan tegasan yang dibenarkan, mengurangkan saiz dan berat mesin dan mekanisme, dan meningkatkan kebolehpercayaan dan hayat perkhidmatan produk. Memperbaiki sifat akibat rawatan haba membolehkan penggunaan aloi komposisi yang lebih mudah, dan oleh itu lebih murah. Aloi juga memperoleh beberapa sifat baru, dan oleh itu skop penggunaannya berkembang.
Tujuan dan jenis rawatan haba
Rawatan terma (terma) merujuk kepada proses yang intipatinya adalah pemanasan dan penyejukan produk mengikut mod tertentu, mengakibatkan perubahan dalam struktur, komposisi fasa, sifat mekanikal dan fizikal bahan, tanpa mengubah komposisi kimia.
Tujuan rawatan haba logam adalah untuk mendapatkan kekerasan yang diperlukan dan meningkatkan ciri kekuatan logam dan aloi. Rawatan haba dibahagikan kepada terma, termomekanikal dan kimia-terma. Rawatan haba hanya pendedahan haba, termomekanikal adalah gabungan pendedahan haba dan ubah bentuk plastik, kimia-terma adalah gabungan pendedahan haba dan kimia. Rawatan haba, bergantung kepada keadaan struktur yang diperoleh hasil daripada penggunaannya, dibahagikan kepada penyepuhlindapan (jenis pertama dan kedua), pengerasan dan pembajaan.
Penyepuhlindapan
Penyepuhlindapan - rawatan haba terdiri daripada memanaskan logam pada suhu tertentu, menahannya dan kemudian menyejukkannya dengan sangat perlahan bersama dengan relau. Digunakan untuk memperbaiki pemotongan logam, mengurangkan kekerasan, mendapatkan struktur bijian, dan juga untuk melegakan tekanan, menghapuskan sebahagian (atau sepenuhnya) semua jenis ketidakhomogenan yang dimasukkan ke dalam logam semasa operasi sebelumnya (pemesinan, rawatan tekanan, tuangan, kimpalan), memperbaiki struktur keluli.
Penyepuhlindapan jenis pertama. Ini adalah penyepuhlindapan di mana tiada transformasi fasa berlaku, dan jika ia berlaku, ia tidak menjejaskan keputusan akhir yang dimaksudkan untuk tujuan yang dimaksudkan. Jenis penyepuhlindapan jenis pertama berikut dibezakan: homogenisasi dan penghabluran semula.
Menghomogenkan– ini adalah penyepuhlindapan dengan pendedahan yang lama pada suhu melebihi 950ºС (biasanya 1100–1200ºС) untuk menyamakan komposisi kimia.
Penghabluran semula- Ini ialah penyepuhlindapan keluli yang dikeraskan pada suhu melebihi suhu di mana penghabluran semula bermula, untuk menghapuskan pengerasan dan mendapatkan saiz butiran tertentu.
Penyepuhlindapan jenis kedua. Ini adalah penyepuhlindapan, di mana transformasi fasa menentukan tujuan yang dimaksudkan. Jenis berikut dibezakan: lengkap, tidak lengkap, resapan, isoterma, ringan, normal (normalisasi), spheroidizing (untuk perlit berbutir).
Penyepuhlindapan penuh dihasilkan dengan memanaskan keluli 30–50 °C di atas titik kritikal, menahan pada suhu ini dan perlahan-lahan menyejukkan kepada 400–500 °C pada kadar 200 °C sejam untuk keluli karbon, 100 °C sejam untuk keluli aloi rendah dan 50 °C dalam jam untuk keluli aloi tinggi. Struktur keluli selepas penyepuhlindapan adalah keseimbangan dan stabil.
Penyepuhlindapan separa dihasilkan dengan memanaskan keluli kepada salah satu suhu yang terletak dalam julat transformasi, menahan dan penyejukan perlahan. Penyepuhlindapan separa digunakan untuk mengurangkan tekanan dalaman, mengurangkan kekerasan dan meningkatkan kebolehmesinan.
Penyepuhlindapan resapan. Logam dipanaskan pada suhu 1100–1200ºС, kerana dalam kes ini proses resapan yang diperlukan untuk menyamakan komposisi kimia berlaku dengan lebih lengkap.
Penyepuhlindapan isoterma adalah seperti berikut: keluli dipanaskan dan kemudian disejukkan dengan cepat (biasanya dengan memindahkannya ke relau lain) ke suhu di bawah suhu kritikal sebanyak 50–100ºС. Terutamanya digunakan untuk keluli aloi. Berfaedah dari segi ekonomi, kerana tempoh penyepuhlindapan konvensional ialah (13 – 15) jam, dan penyepuhlindapan isoterma (4 – 6) jam
Penyepuhlindapan spheroidizing (pada perlit berbutir) terdiri daripada keluli pemanasan di atas suhu kritikal sebanyak 20 - 30 ° C, menahannya pada suhu ini dan perlahan-lahan menyejukkan.
Penyepuhlindapan terang dijalankan mengikut mod penyepuhlindapan lengkap atau tidak lengkap menggunakan atmosfera pelindung atau dalam relau dengan vakum separa. Ia digunakan untuk melindungi permukaan logam daripada pengoksidaan dan penyahkarbonan.
Normalisasi– terdiri daripada memanaskan logam pada suhu (30–50) ºС di atas titik kritikal dan penyejukan seterusnya dalam udara. Tujuan normalisasi berbeza-beza bergantung pada komposisi keluli. Daripada penyepuhlindapan, keluli karbon rendah dinormalisasi. Untuk keluli karbon sederhana, normalisasi digunakan dan bukannya pengerasan dan pembajaan tinggi. Keluli karbon tinggi tertakluk kepada normalisasi untuk menghapuskan rangkaian simentit. Normalisasi diikuti dengan pembajaan tinggi digunakan dan bukannya penyepuhlindapan untuk membetulkan struktur keluli aloi. Normalisasi, berbanding dengan penyepuhlindapan, adalah operasi yang lebih menjimatkan, kerana ia tidak memerlukan penyejukan dengan relau.
Pengerasan
Pengerasan– ini adalah pemanasan kepada suhu optimum, pegangan dan penyejukan pantas seterusnya untuk mendapatkan struktur bukan keseimbangan.
Hasil daripada pengerasan, kekuatan dan kekerasan keluli meningkat dan kemuluran keluli berkurangan. Parameter utama semasa pengerasan adalah suhu pemanasan dan kadar penyejukan. Kadar pelindapkejutan kritikal ialah kadar penyejukan yang memastikan pembentukan struktur - martensit atau martensit dan austenit tertahan.
Bergantung pada bentuk bahagian, gred keluli dan set sifat yang diperlukan, pelbagai kaedah pengerasan digunakan.
Pelindapkejutan dalam satu penyejuk. Bahagian itu dipanaskan pada suhu pengerasan dan disejukkan dalam satu penyejuk (air, minyak).
Pengerasan dalam dua persekitaran (pengerasan sekejap-sekejap)– ini adalah pengerasan di mana bahagian itu disejukkan secara berurutan dalam dua persekitaran: medium pertama ialah penyejuk (air), yang kedua ialah udara atau minyak.
Langkah pengerasan. Bahagian yang dipanaskan kepada suhu pelindapkejutan disejukkan dalam garam cair; selepas menahan masa yang diperlukan untuk menyamakan suhu ke atas keseluruhan keratan rentas, bahagian itu disejukkan di udara, yang membantu mengurangkan tegasan pelindapkejutan.
Pengerasan isoterma sama seperti yang dilangkah, ia dihasilkan dalam dua persekitaran penyejukan. Suhu medium panas (mandi garam, nitrat atau alkali) adalah berbeza: ia bergantung pada komposisi kimia keluli, tetapi sentiasa 20-100 °C di atas titik transformasi martensit untuk keluli tertentu. Penyejukan akhir kepada suhu bilik dijalankan di udara. Pengerasan isoterma digunakan secara meluas untuk bahagian yang diperbuat daripada keluli aloi tinggi. Selepas pengerasan isoterma, keluli memperoleh sifat kekuatan tinggi, iaitu gabungan keliatan dan kekuatan tinggi.
Mengeras dengan pemarah diri Ia digunakan secara meluas dalam pengeluaran alat. Proses ini terdiri daripada fakta bahawa bahagian-bahagian itu disimpan dalam medium penyejukan bukan sehingga ia disejukkan sepenuhnya, tetapi pada masa tertentu ia dikeluarkan daripadanya untuk mengekalkan sejumlah haba dalam teras bahagian, disebabkan oleh yang mana pembajaan seterusnya dijalankan.
bercuti
bercuti keluli adalah operasi rawatan haba terakhir yang membentuk struktur, dan oleh itu sifat keluli. Pembajaan terdiri daripada pemanasan keluli kepada suhu yang berbeza (bergantung pada jenis pembajaan, tetapi sentiasa di bawah titik kritikal), menahannya pada suhu ini dan menyejukkan pada kadar yang berbeza. Tujuan pembajaan adalah untuk melegakan tegasan dalaman yang timbul semasa proses pengerasan dan mendapatkan struktur yang diperlukan.
Bergantung pada suhu pemanasan bahagian yang keras, tiga jenis pembajaan dibezakan: tinggi, sederhana dan rendah.
Cuti tinggi dihasilkan pada suhu pemanasan melebihi 350–600 °C, tetapi di bawah titik kritikal; pembajaan tersebut digunakan untuk keluli struktur.
Purata cuti dihasilkan pada suhu pemanasan 350 – 500 °C; Pembajaan sedemikian digunakan secara meluas untuk keluli musim bunga dan musim bunga.
Percutian Rendah dihasilkan pada suhu 150–250 °C. Kekerasan bahagian selepas pengerasan kekal hampir tidak berubah; pembajaan rendah digunakan untuk keluli alat karbon dan aloi, yang memerlukan kekerasan tinggi dan rintangan haus.
Kawalan tempering dilakukan dengan warna-warna kotor yang muncul pada permukaan bahagian.
Penuaan
Penuaan ialah satu proses menukar sifat aloi tanpa perubahan ketara dalam struktur mikro. Dua jenis penuaan diketahui: terma dan ubah bentuk.
Penuaan terma berlaku akibat perubahan keterlarutan karbon dalam besi bergantung kepada suhu.
Sekiranya perubahan dalam kekerasan, kemuluran dan kekuatan berlaku pada suhu bilik, maka penuaan tersebut dipanggil semula jadi.
Jika proses itu berlaku pada suhu tinggi, maka penuaan dipanggil tiruan.
Penuaan ubah bentuk (mekanikal). berlaku selepas ubah bentuk plastik sejuk.
Rawatan selsema
Satu jenis rawatan haba baharu untuk meningkatkan kekerasan keluli dengan menukar austenit tertahan keluli keras kepada martensit. Ini dilakukan dengan menyejukkan keluli ke suhu titik martensit yang lebih rendah.
Kaedah pengerasan permukaan
Pengerasan permukaan ialah proses rawatan haba yang melibatkan pemanasan lapisan permukaan keluli kepada suhu melebihi kritikal dan penyejukan seterusnya untuk mendapatkan struktur martensit dalam lapisan permukaan.
Jenis berikut dibezakan: pengerasan aruhan; pengerasan dalam elektrolit, pengerasan apabila dipanaskan dengan arus frekuensi tinggi (HF), pengerasan dengan pemanasan api gas.
Pengerasan induksi adalah berdasarkan fenomena fizikal, intipatinya ialah arus elektrik frekuensi tinggi yang melalui konduktor mencipta medan elektromagnet di sekelilingnya. Arus pusar teraruh pada permukaan bahagian yang diletakkan di medan ini, menyebabkan logam itu panas ke suhu tinggi. Ini membolehkan transformasi fasa berlaku.
Bergantung kepada kaedah pemanasan, pengerasan aruhan dibahagikan kepada tiga jenis:
pemanasan serentak dan pengerasan seluruh permukaan (digunakan untuk bahagian kecil);
pemanasan berurutan dan pengerasan bahagian individu (digunakan untuk aci engkol dan bahagian yang serupa);
pemanasan berurutan berterusan dan pelindapkejutan melalui pergerakan (digunakan untuk bahagian yang panjang).
Pengerasan api gas. Proses pengerasan nyalaan gas terdiri daripada memanaskan dengan cepat permukaan bahagian dengan nyalaan asetilena-oksigen, gas-oksigen atau oksigen-minyak tanah kepada suhu pengerasan, diikuti dengan penyejukan dengan air atau emulsi.
Pelindapkejutan dalam elektrolit. Proses pengerasan dalam elektrolit adalah seperti berikut: bahagian yang akan dikeraskan diturunkan ke dalam tab elektrolit (larutan 5–10% garam terkalsin) dan arus 220–250 V dilalui. Akibatnya, bahagian dipanaskan pada suhu tinggi. Bahagian itu disejukkan sama ada dalam elektrolit yang sama (selepas mematikan arus) atau dalam tangki pelindapkejutan khas.
Rawatan termo-mekanikal
Rawatan termo-mekanikal (T.M.O.) ialah kaedah baharu untuk mengukuhkan logam dan aloi sambil mengekalkan kemuluran yang mencukupi, menggabungkan ubah bentuk plastik dan mengukuhkan rawatan haba (pengerasan dan pembajaan). Terdapat tiga kaedah utama pemprosesan termomekanikal.
Rawatan termomekanikal suhu rendah (L.T.M.O.) adalah berdasarkan pengerasan langkah, iaitu, ubah bentuk plastik keluli dilakukan pada suhu kestabilan relatif austenit, diikuti dengan pengerasan dan pembajaan.
Rawatan termomekanikal suhu tinggi (V.T.M.O) pada masa yang sama ubah bentuk plastik dilakukan pada suhu kestabilan austenit, diikuti dengan pelindapkejutan dan pembajaan.
Rawatan termomekanikal awal (P.T.M.O.) ubah bentuk dalam kes ini boleh dilakukan pada suhu N.T.M.O dan V.T.M.O atau pada suhu 20ºC. Seterusnya, rawatan haba biasa dijalankan: pengerasan dan pembajaan.
Tujuan dan jenis rawatan kimia-terma
Rawatan kimia-terma ialah proses yang merupakan gabungan kesan haba dan kimia untuk mengubah komposisi, struktur dan sifat lapisan permukaan keluli.
Tujuan rawatan kimia-terma: meningkatkan kekerasan permukaan, rintangan haus, had ketahanan, rintangan kakisan, rintangan haba (rintangan skala), rintangan asid.
Jenis rawatan kimia-terma berikut paling banyak digunakan dalam industri: penyimenan; nitrokarburisasi; nitriding; sianidasi; pemetaan resapan.
Penyimenan ialah proses ketepuan permukaan dengan karbon, dijalankan untuk tujuan pengerasan permukaan bahagian.
Bergantung pada carburizer yang digunakan, carburization terbahagi kepada tiga jenis: carburization with solid carburizer; penyimenan gas (metana, propana, gas asli).
Penyimenan gas. Bahagian dipanaskan hingga 900–950ºС dalam relau khas yang tertutup rapat, di mana penyimenan gas yang mengandungi karbon [semula jadi (semula jadi) atau tiruan] dibekalkan dalam aliran berterusan.
Proses pengkarbonan dalam karburizer pepejal adalah seperti berikut. Bahagian-bahagian, dibungkus dalam kotak bersama-sama dengan karburizer (campuran arang dengan pengaktif), dipanaskan pada suhu tertentu dan disimpan pada suhu ini untuk masa yang lama, kemudian disejukkan dan tertakluk kepada rawatan haba.
Bahagian yang diperbuat daripada keluli karbon dan aloi dengan kandungan karbon tidak lebih daripada 0.2% tertakluk kepada penyimenan oleh mana-mana kaedah yang dibincangkan di atas. Karburasi keluli aloi yang mengandungi unsur pembentuk karbida Cr, W, V memberikan hasil yang sangat baik: selain meningkatkan kekerasan permukaan dan rintangan haus, had keletihannya juga meningkat.
Nitriding ialah proses menepu lapisan permukaan pelbagai logam dan aloi, produk keluli atau bahagian dengan nitrogen apabila dipanaskan dalam persekitaran yang sesuai. Kekerasan permukaan produk, ketahanan, rintangan haus, dan rintangan kakisan meningkat.
Sianidasi – ketepuan lapisan permukaan produk dengan kedua-dua karbon dan nitrogen.
Bergantung pada medium yang digunakan, sianidasi dibezakan: dalam media pepejal; dalam media cecair; dalam persekitaran gas.
Bergantung pada suhu pemanasan, sianidasi dibahagikan kepada suhu rendah dan suhu tinggi.
Sianidasi dalam media cecair dihasilkan dalam mandian garam cair.
Sianidasi dalam media gas (nitrokarburisasi). Proses menepu permukaan bahagian secara serentak dengan karbon dan nitrogen. Untuk melakukan ini, bahagian dipanaskan dalam persekitaran yang terdiri daripada gas penyimenan dan ammonia, iaitu, nitrokarburisasi menggabungkan proses pengkarbonan gas dan nitriding.
Ketepuan resapan dengan logam dan metaloid
Terdapat dan digunakan dalam kaedah industri untuk menepu permukaan bahagian dengan pelbagai logam (aluminium, kromium, dll.) dan metaloid (silikon, boron, dll.). Tujuan ketepuan tersebut adalah untuk meningkatkan rintangan skala, rintangan kakisan , rintangan asid, kekerasan dan rintangan haus bahagian. Akibatnya, lapisan permukaan memperoleh sifat khas, yang membolehkan penjimatan unsur pengaloian.
Mengaluminkan – proses penepuan lapisan permukaan keluli dengan aluminium untuk meningkatkan rintangan haba (rintangan skala) dan ketahanan terhadap kakisan atmosfera.
Aluminisasi dilakukan dalam campuran serbuk, dalam tab mandi dengan aluminium cair, dalam persekitaran gas dan dengan menyembur aluminium cair.
Penyaduran krom – proses penepuan lapisan permukaan keluli dengan kromium untuk meningkatkan rintangan kakisan dan rintangan haba, dan apabila penyaduran krom keluli karbon tinggi - untuk meningkatkan kekerasan dan rintangan haus.
Silikonisasi – proses menepu lapisan permukaan bahagian dengan silikon untuk meningkatkan rintangan kakisan dan rintangan asid. Bahagian yang diperbuat daripada keluli karbon rendah dan sederhana, serta besi tuang mulur dan berkekuatan tinggi tertakluk kepada silikonisasi.
membosankan – proses menepu lapisan permukaan bahagian dengan boron. Tujuan membosankan adalah untuk meningkatkan kekerasan, ketahanan terhadap haus kasar dan kakisan dalam persekitaran yang agresif, rintangan haba dan rintangan haba bahagian keluli. Terdapat dua kaedah membosankan: elektrolisis cecair dan membosankan gas.
Sulfidasi – proses menepu lapisan permukaan bahagian keluli dengan sulfur untuk memperbaiki sifat tekanan melampau dan meningkatkan rintangan haus bahagian.
Sulfosianasi – proses ketepuan permukaan bahagian keluli dengan sulfur, karbon dan nitrogen. Pengaruh gabungan sulfur dan nitrogen dalam lapisan permukaan logam memberikan sifat tekanan ekstrem yang lebih tinggi dan rintangan haus berbanding tepu dengan sulfur sahaja.
Rawatan haba besi tuang
Rawatan haba besi tuang dijalankan untuk melegakan tekanan dalaman yang timbul semasa tuangan dan menyebabkan perubahan dalam saiz dan bentuk tuangan dari semasa ke semasa, mengurangkan kekerasan dan meningkatkan kebolehmesinan, dan meningkatkan sifat mekanikal. Besi tuang tertakluk kepada penyepuhlindapan, penormalan, pelindapkejutan dan pembajaan, serta beberapa jenis rawatan kimia dan haba (nitriding, aluminisasi, penyaduran krom).
Penyepuhlindapan untuk melegakan tekanan dalaman . Besi tuang tertakluk kepada penyepuhlindapan ini pada suhu berikut: besi tuang kelabu dengan grafit kepingan 500 – 570ºС; besi tuang berkekuatan tinggi dengan grafit nodular 550 – 650ºС; besi tuang aloi rendah 570 – 600ºС; besi tuang aloi tinggi 620 – 650ºС. Semasa penyepuhlindapan ini, perubahan fasa tidak berlaku, tetapi tegasan dalaman dilegakan, kelikatan meningkat, dan meledingkan dan retak semasa operasi dihapuskan.
Melembutkan penyepuhlindapan (grafitisasi penyepuhlindapan suhu rendah ). Lakukan untuk meningkatkan kebolehmesinan dan meningkatkan kemuluran. Ia dijalankan dengan pendedahan berpanjangan pada 680 – 700ºС atau penyejukan perlahan tuangan pada 760 – 700ºС. Untuk bahagian dengan konfigurasi kompleks, penyejukan adalah perlahan, dan untuk bahagian dengan bentuk mudah, penyejukan dipercepatkan.
Penyepuhlindapan grafit , akibatnya besi tuang boleh ditempa diperolehi daripada besi tuang putih.
Normalisasi digunakan untuk meningkatkan karbon tetap, meningkatkan kekerasan, kekuatan dan rintangan haus besi tuang kelabu, mudah ditempa dan berkekuatan tinggi. Apabila menormalkan, besi tuang (tuangan) dipanaskan di atas suhu julat transformasi 850 – 950ºС dan selepas dipegang, disejukkan di udara.
Pengerasan besi kelabu, mulur dan mulur dirawat untuk meningkatkan kekerasan, kekuatan dan rintangan haus. Mengikut kaedah pelaksanaan, pengerasan besi tuang boleh menjadi isipadu berterusan, isoterma dan permukaan.
Pada pengerasan berterusan isipadu Besi tuang dipanaskan pada suhu 850 – 950ºС. Kemudian ia disimpan untuk memanaskan badan dan melarutkan karbon sepenuhnya. Penyejukan dilakukan dalam air atau minyak. Selepas pengerasan, pembajaan dijalankan pada suhu 200 – 600ºС. Akibatnya, kekerasan, kekuatan dan rintangan haus besi tuang meningkat.
Pada pengerasan isoterma besi tuang dipanaskan dengan cara yang sama seperti dengan volumetrik secara berterusan ke pengerasan, disimpan selama 10 hingga 90 minit dan disejukkan dalam garam cair pada 200 - 400ºС, dan selepas dipegang, disejukkan di udara.
Pengerasan permukaan dengan pemanasan lapisan permukaan dengan nyalaan oksigen-asetilena, arus frekuensi tinggi atau dalam elektrolit. Suhu pemanasan 900 – 1000ºС. Menyejukkan dalam air, minyak atau emulsi minyak.
Penuaan digunakan untuk menstabilkan dimensi bahagian besi tuang, mencegah meleding dan melegakan tekanan dalaman. Biasanya, penuaan dilakukan selepas pemprosesan mekanikal kasar. Terdapat dua jenis penuaan: semulajadi dan buatan.
Penuaan semulajadi dijalankan pada di luar rumah atau di dalam rumah. Produk selepas tuangan berumur 6 – 15 bulan.
Penuaan buatan dijalankan pada suhu tinggi; tempoh - beberapa jam. Semasa penuaan buatan, besi tuang dimuatkan ke dalam relau yang dipanaskan hingga 100 - 200ºC, dipanaskan pada suhu 550 - 570ºC pada kadar 30 - 60ºC sejam, disimpan selama 3 - 5 jam dan disejukkan bersama dengan relau pada kadar. daripada 20 - 40ºC sejam kepada suhu 150 – 200ºС, dan kemudian disejukkan di udara.
Rawatan kimia-terma besi tuang
Untuk meningkatkan kekerasan permukaan dan rintangan haus, besi tuang kelabu tertakluk kepada nitriding. Besi tuang mutiara kelabu yang dialoi dengan kromium, molibdenum dan aluminium paling kerap dinitrida. Suhu nitriding 550 – 580ºС, masa penahanan 30 – 70 jam. Sebagai tambahan kepada nitriding, meningkatkan kekerasan permukaan dan rintangan haus besi tuang pearlitik kelabu beraloi boleh dicapai dengan gas dan sianidasi cecair pada suhu 570ºC. Untuk meningkatkan rintangan haba, tuangan besi tuang boleh tertakluk kepada aluminizing, dan untuk mendapatkan rintangan kakisan yang tinggi dalam asid - silikon.
Rawatan haba aloi logam bukan ferus
Aloi aluminium
Aloi aluminium tertakluk kepada tiga jenis rawatan haba: penyepuhlindapan, pengerasan dan penuaan. Jenis utama penyepuhlindapan ialah: resapan, penghabluran semula dan aloi yang dikuatkan secara haba.
homogenisasi digunakan untuk meratakan mikroheterogeniti kimia butiran larutan pepejal. Untuk melakukan homogenisasi, aloi aluminium dipanaskan hingga 450–520ºС dan dikekalkan pada suhu ini selama 4 hingga 40 jam; selepas memegang - menyejukkan dengan relau atau di udara. Akibatnya, struktur menjadi lebih homogen dan keplastikan meningkat.
Penyepuhlindapan penghabluran semula untuk aluminium dan aloi berasaskan aluminium ia digunakan lebih meluas daripada keluli. Ini dijelaskan oleh fakta bahawa logam seperti aluminium dan tembaga, serta banyak aloi berdasarkannya, tidak diperkuat dengan pengerasan dan peningkatan sifat mekanikal hanya boleh dicapai dengan kerja sejuk, dan operasi perantaraan semasa pemprosesan sedemikian adalah. penyepuhlindapan penghabluran semula. Suhu penyepuhlindapan penghabluran semula aloi aluminium ialah 300 – 500ºС, masa penahanan ialah 0.5 – 2 jam.
Penyepuhlindapan aloi yang dikuatkan secara terma digunakan untuk mengeluarkan sepenuhnya pengerasan, ia dijalankan pada suhu 350 - 450ºС dengan pendedahan selama 1 - 2 jam dan seterusnya penyejukan agak perlahan.
Selepas pengerasan kekuatan aloi meningkat sedikit, tetapi kemuluran tidak berubah. Selepas pengerasan, aloi aluminium tertakluk kepada penuaan , di mana penguraian larutan pepejal supertepu berlaku.
Aloi aluminium tempa
Dalam keadaan keras, duralumin adalah plastik dan mudah berubah bentuk. Selepas pengerasan dan penuaan semula jadi atau buatan, kekuatan duralumin meningkat dengan mendadak.
Aloi aluminium tuang
Untuk aloi aluminium tuang, pelbagai jenis rawatan haba digunakan bergantung kepada komposisi kimia. Untuk mengukuhkan, aloi aluminium tuang tertakluk kepada pelindapkejutan untuk mendapatkan larutan pepejal supertepu dan penuaan buatan, serta hanya pelindapkejutan tanpa penuaan untuk mendapatkan larutan pepejal yang stabil dalam keadaan dipadamkan.
Aloi magnesium
Aloi magnesium, seperti aloi aluminium, tertakluk kepada penyepuhlindapan, pengerasan dan penuaan. Untuk meratakan mikroheterogeniti kimia butiran larutan pepejal melalui resapan, jongkong aloi magnesium tertakluk kepada homogenisasi pada suhu 350 – 400ºС dengan pendedahan selama 18 – 24 jam. Aloi magnesium tempa separuh siap tertakluk kepada penyepuhlindapan penghabluran semula pada suhu ≈ 350ºС, serta pada suhu yang lebih rendah 150 – 250ºС penyepuhlindapan untuk melegakan tekanan sisa.
Aloi magnesium tertakluk kepada pengerasan, atau pengerasan Dan penuaan buatan. Pada suhu 20C, tiada perubahan berlaku dalam aloi magnesium yang mengeras, iaitu, ia tidak tertakluk kepada penuaan semula jadi.
Tembaga dan aloi tembaga
Rawatan haba tembaga. Ubah bentuk kuprum disertai dengan peningkatan kekuatannya dan penurunan kemuluran. Untuk meningkatkan kemuluran, tembaga tertakluk kepada penyepuhlindapan penghabluran semula pada 500–600ºС, akibatnya kemuluran meningkat dengan mendadak dan kekuatan berkurangan.
Rawatan haba loyang. Mereka hanya tertakluk kepada penyepuhlindapan penghabluran semula pada 600 – 700ºС (untuk menghilangkan pengerasan). Loyang disejukkan semasa penyepuhlindapan di udara atau untuk mempercepatkan penyejukan dan skala berasingan yang lebih baik dalam air. Bahagian loyang yang mempunyai tegasan sisa selepas ubah bentuk dicirikan oleh keretakan spontan dalam suasana lembap. Untuk mengelakkan ini, bahagian tembaga tertakluk kepada penyepuhlindapan suhu rendah pada 200 - 300 C, akibatnya tegasan sisa dikeluarkan, tetapi pengerasan kekal. Penyepuhlindapan suhu rendah amat diperlukan untuk loyang aluminium, yang terdedah kepada keretakan spontan.
Rawatan haba gangsa. Untuk menyamakan komposisi kimia gangsa, ia tertakluk kepada homogenisasi pada 700 – 750ºС, diikuti dengan penyejukan pantas. Untuk melegakan tekanan dalaman, tuangan disepuhlindapkan pada 550ºC. Untuk memulihkan keplastikan antara operasi kerja sejuk, ia tertakluk kepada penyepuhlindapan penghabluran semula pada 600–700ºС.
gangsa aluminium dengan kandungan aluminium 8 hingga 11%, yang mengalami penghabluran semula fasa apabila dipanaskan dan disejukkan, boleh mengalami pengerasan Hasil daripada pengerasan, kekuatan dan kekerasan meningkat, tetapi kemuluran berkurangan. Selepas mengeras sepatutnya bercuti pada 400 – 650º C bergantung pada sifat yang diperlukan. Juga tertakluk homogenisasi, dan produk separuh siap boleh ubah bentuk - penyepuhlindapan penghabluran semula pada 650 – 800ºС.
Berilium gangsa mengeras dalam air dari suhu 760 – 780ºС; dalam kes ini, fasa yang berlebihan tidak mempunyai masa untuk memisahkan, dan selepas pelindapkejutan aloi terdiri daripada larutan pepejal supersaturated dan mempunyai kekerasan dan kekuatan yang rendah dan kemuluran yang tinggi. Selepas pengerasan dijalankan bercuti(penuaan) pada 300 – 350ºС selama 2 jam. Untuk meningkatkan kestabilan larutan pepejal supertepu dan memudahkan pengerasan gangsa berilium, tambahan dialoi dengan nikel .
Aloi titanium
Aloi titanium tertakluk kepada penyepuhlindapan dan penyepuhlindapan semula dengan penghabluran semula fasa, serta pengerasan melalui rawatan haba - pengerasan dan penuaan. Untuk meningkatkan rintangan haus dan rintangan lecet, aloi titanium tertakluk kepada nitriding, pengkarburan atau pengoksidaan.
Penyepuhlindapan penghabluran semula digunakan untuk titanium dan aloi untuk menghilangkan pengerasan selepas bekerja sejuk. Suhu penyepuhlindapan penghabluran semula ialah 520 – 850ºС, bergantung kepada komposisi kimia aloi dan jenis produk separuh siap.
Penyepuhlindapan dengan penghabluran semula fasa digunakan untuk mengurangkan kekerasan, meningkatkan keplastikan, menapis bijirin, dan menghapuskan heterogeniti struktur. Penyepuhlindapan mudah, isoterma dan berganda digunakan; suhu pemanasan semasa penyepuhlindapan 750 – 950ºС bergantung kepada aloi.
Pada penyepuhlindapan isoterma selepas memegang pada suhu penyepuhlindapan, bahagian disejukkan kepada 500 - 650ºС (bergantung kepada aloi) dalam relau yang sama atau dipindahkan ke relau lain dan disimpan untuk masa tertentu, dan disejukkan di udara. Dengan penyepuhlindapan isoterma, masa penyepuhlindapan dikurangkan, dan kemuluran lebih tinggi.
Pada penyepuhlindapan berganda bahagian dipanaskan kepada suhu penyepuhlindapan, dipegang dan disejukkan di udara. Kemudian saya memanaskannya semula kepada 500 - 650ºС, tahan dan sejukkan di udara. Penyepuhlindapan berganda, berbanding dengan penyepuhlindapan isoterma, meningkatkan kekuatan tegangan dengan sedikit penurunan dalam kemuluran dan mengurangkan masa pemprosesan.
Daripada semua jenis rawatan kimia-terma aloi titanium, yang paling meluas ialah nitriding, dijalankan dalam persekitaran nitrogen atau dalam campuran nitrogen dan argon pada suhu 850 - 950 C selama 10 - 50 jam. Bahagian yang diperbuat daripada aloi titanium selepas nitriding mempunyai sifat anti geseran yang baik.
Kesimpulan
Rawatan haba adalah salah satu operasi utama, paling penting dalam kitaran pemprosesan teknologi am, pelaksanaan yang betul yang menentukan kualiti (sifat mekanikal dan fizikal-kimia) bahagian dan mekanisme mesin yang dibuat, alat dan produk lain. Proses teknologi untuk rawatan haba besi tuang kelabu dan putih dan aloi logam bukan ferus telah dibangunkan dan dirasionalkan
Arah yang menjanjikan untuk meningkatkan teknologi rawatan haba ialah pemasangan unit untuk rawatan haba di kedai mekanikal, penciptaan talian automatik yang merangkumi proses rawatan haba, serta pembangunan kaedah yang memastikan peningkatan dalam sifat kekuatan bahagian, mereka kebolehpercayaan dan ketahanan.
kesusasteraan
1. B.V. Zakharov. V.N. Berseneva "Proses dan peralatan teknologi progresif untuk rawatan haba logam" M. "Sekolah Tinggi" 1988
2. V.M. Zuev "Rawatan terma logam" M. Sekolah Tinggi 1986
3. B.A. Kuzmin "Teknologi logam dan bahan struktur" M. "Kejuruteraan Mekanikal" 1981
4. V.M. Nikiforov "Teknologi logam dan bahan struktur" M. "Sekolah Tinggi" 1968
5. A.I. Samokhotsky N.G. Parfenovskaya "Teknologi rawatan haba logam" M. Kejuruteraan Mekanikal 1976
RAWATAN HABA KOMPLEKS LOGAM
Rawatan haba (rawatan haba ) keluli, aloi Terdapat jenis berikut: penyepuhlindapan, normalisasi, pengerasan, bercuti.
- Penyepuhlindapan- rawatan haba (rawatan haba) logam, di mana logam itu dipanaskan dan kemudian perlahan-lahan disejukkan. Rawatan haba ini (iaitu penyepuhlindapan) datang dalam pelbagai jenis (jenis penyepuhlindapan bergantung pada suhu pemanasan dan kadar penyejukan logam).
- Pengerasan- rawatan haba (rawatan haba) keluli, aloi, berdasarkan penghabluran semula keluli (aloi) apabila dipanaskan pada suhu melebihi kritikal; Selepas pendedahan yang mencukupi kepada suhu kritikal untuk melengkapkan rawatan haba, penyejukan pantas berlaku. Keluli yang dikeraskan (aloi) mempunyai struktur bukan keseimbangan, jadi satu lagi jenis rawatan haba boleh digunakan - pembajaan.
- bercuti- rawatan haba (rawatan haba) keluli dan aloi, dijalankan selepas pengerasan untuk mengurangkan atau melegakan tegasan baki dalam keluli dan aloi, meningkatkan keliatan, mengurangkan kekerasan dan kerapuhan logam.
- Normalisasi- rawatan haba (rawatan haba), serupa dengan penyepuhlindapan. Perbezaan antara rawatan haba ini (penormalan dan penyepuhlindapan) ialah semasa penormalan keluli disejukkan di udara (semasa penyepuhlindapan, dalam relau).
PENELITIAN KELULI
Penyepuhlindapan adalah proses rawatan haba logam yang melibatkan pemanasan dan kemudian perlahan-lahan menyejukkan logam. Peralihan struktur daripada keadaan bukan keseimbangan kepada keadaan keseimbangan yang lebih. Penyepuhlindapan jenis pertama , jenisnya: kembali (aka rehat logam), penyepuhlindapan penghabluran semula (juga dipanggil penghabluran semula), penyepuhlindapan untuk melegakan tekanan dalaman , penyepuhlindapan penyebaran (juga dipanggil homogenisasi). Penyepuhlindapan jenis kedua – menukar struktur aloi melalui penghabluran semula berhampiran titik kritikal untuk mendapatkan struktur keseimbangan. Penyepuhlindapan jenis kedua, jenisnya: penuh , tidak lengkap , isoterma penyepuhlindapan. Penyepuhlindapan dan jenisnya berhubung dengan keluli dibincangkan di bawah.
- Kembali (rehat) keluli– pemanasan hingga 200 – 400C°, penyepuhlindapan untuk mengurangkan atau menghilangkan pengerasan. Berdasarkan keputusan penyepuhlindapan, penurunan herotan kekisi kristal dalam kristal dan pemulihan separa sifat fizikokimia keluli diperhatikan.
- Penghabluran semula penyepuhlindapan keluli (penghabluran semula) - pemanasan kepada suhu 500 – 550C°; penyepuhlindapan untuk melegakan tekanan dalaman – pemanasan pada suhu 600 – 700C°. Jenis penyepuhlindapan ini melegakan tegasan dalaman dalam logam tuangan akibat penyejukan bahagiannya yang tidak sekata, juga dalam bahan kerja yang diproses dengan tekanan (bergelek, melukis, mengecap) menggunakan suhu di bawah kritikal. Hasil daripada penyepuhlindapan penghabluran semula, kristal baru tumbuh daripada butiran yang cacat, lebih dekat kepada keseimbangan, oleh itu kekerasan keluli berkurangan, dan kemuluran dan keliatan meningkat. Untuk mengeluarkan sepenuhnya tegasan dalaman keluli, suhu sekurang-kurangnya 600C° diperlukan. Penyejukan selepas menahan pada suhu tertentu mestilah agak perlahan: disebabkan oleh penyejukan dipercepatkan logam, tekanan dalaman timbul semula.
- Penyepuhlindapan resapan keluli (homogenisasi) digunakan apabila keluli mempunyai pengasingan intrahablur. Meratakan komposisi dalam butiran austenit dicapai dengan resapan karbon dan kekotoran lain dalam keadaan pepejal, bersama dengan resapan sendiri besi. Mengikut keputusan penyepuhlindapan, keluli menjadi homogen dalam komposisi (homogen), oleh itu penyepuhlindapan resapan juga dipanggil homogenisasi. Suhu penghomogenan hendaklah cukup tinggi, tetapi pembakaran dan pencairan bijirin tidak dibenarkan. Jika kelesuan dibenarkan berlaku, oksigen di udara mengoksidakan besi, menembusi ketebalannya, dan kristalit terbentuk, dipisahkan oleh cengkerang oksida. Pembakaran terlampau tidak boleh dihapuskan, oleh itu bahan kerja yang terlalu terbakar adalah kecacatan terakhir. Penyepuhlindapan resapan keluli biasanya mengakibatkan kekasaran bijirin yang terlalu banyak, yang harus diperbetulkan dengan penyepuhlindapan penuh berikutnya (kepada butiran halus).
- Penyepuhlindapan lengkap keluli dikaitkan dengan penghabluran semula fasa, penghalusan butiran pada suhu titik AC1 Dan AC2. Tujuannya adalah untuk memperbaiki struktur keluli untuk memudahkan pemprosesan seterusnya dengan memotong, mengecap atau mengeras, serta untuk mendapatkan struktur pearlit keseimbangan berbutir halus bagi bahagian siap. Untuk penyepuhlindapan lengkap, keluli dipanaskan 30-50C° di atas suhu garisan GSK dan disejukkan perlahan-lahan. Selepas penyepuhlindapan, lebihan simentit (dalam keluli hypereutectoid) dan simentit eutektoid mempunyai bentuk plat, itulah sebabnya pearlit dipanggil lamellar
- Apabila menyepuhlindap keluli pada perlit lamellar bahan kerja dibiarkan di dalam relau sehingga disejukkan, selalunya dengan relau dipanaskan sebahagiannya dengan bahan api, supaya kadar penyejukan tidak lebih daripada 10-20C° sejam. Penyepuhlindapan juga mencapai penghalusan bijirin. Struktur berbutir kasar, sebagai contoh, keluli hypoeutectoid, diperoleh semasa pemejalan disebabkan oleh pertumbuhan bebas bijirin (jika penyejukan tuangan perlahan), serta akibat terlalu panas keluli. Struktur ini dipanggil Widmanstätten (dinamakan sempena ahli astronomi Austria A. Widmanstätten, yang menemui struktur sedemikian pada besi meteorik pada tahun 1808). Struktur ini memberikan kekuatan rendah kepada bahan kerja. Struktur ini dicirikan oleh fakta bahawa kemasukan ferit (kawasan cahaya) dan pearlit (kawasan gelap) terletak dalam bentuk plat memanjang pada sudut yang berbeza antara satu sama lain. Dalam keluli hypereutectoid, struktur Widmanstätten dicirikan oleh susunan lebihan simentit seperti coretan. Penapisan bijirin dikaitkan dengan penghabluran semula besi alfa menjadi besi gamma; Disebabkan oleh penyejukan dan peralihan terbalik besi gamma kepada besi alfa, struktur berbutir halus terpelihara. Oleh itu, salah satu hasil penyepuhlindapan pada perlit lamellar ialah struktur berbutir halus.
- Penyepuhlindapan keluli yang tidak lengkap dikaitkan dengan penghabluran semula fasa hanya pada suhu titik A C1; penyepuhlindapan separa digunakan selepas rawatan tekanan panas, apabila bahan kerja mempunyai struktur berbutir halus.
- Keluli penyepuhlindapan pada perlit berbutir Biasanya digunakan untuk keluli eutectoid dan hypereutectoid, untuk meningkatkan kemuluran dan keliatan keluli dan mengurangkan kekerasannya. Untuk mendapatkan perlit berbutir, keluli dipanaskan di atas titik AC1, kemudian disimpan untuk masa yang singkat supaya simentit tidak larut sepenuhnya dalam austenit. Keluli kemudiannya disejukkan ke suhu di bawah sedikit Ar1 , disimpan pada suhu ini selama beberapa jam. Dalam kes ini, zarah-zarah simentit yang tinggal berfungsi sebagai nukleus penghabluran untuk semua simentit yang dibebaskan, yang tumbuh sebagai kristalit bulat (globular) yang tersebar dalam ferit. Sifat-sifat pearlit berbutir berbeza dengan ketara daripada sifat-sifat pearlit lamelar dalam arah kekerasan yang lebih rendah, tetapi lamelar dan kelikatan yang lebih besar. Ini terutamanya terpakai kepada keluli hypereutectoid, di mana semua simentit (kedua-dua eutectoid dan lebihan) diperolehi dalam bentuk globul.
- Penyepuhlindapan isoterma - selepas dipanaskan dan dipegang, keluli disejukkan dengan cepat ke suhu di bawah titik A 1, kemudian disimpan pada suhu ini sehingga austenit terurai sepenuhnya menjadi pearlit, selepas itu ia disejukkan di udara. Penggunaan penyepuhlindapan isoterma dengan ketara mengurangkan masa dan juga meningkatkan produktiviti. Sebagai contoh, penyepuhlindapan biasa keluli aloi berlangsung 13-15 jam, dan penyepuhlindapan isoterma - hanya 4-7 jam.
PENGERASAN KELULI
Perbezaan dibuat antara pengerasan dengan transformasi polimorfik, untuk keluli, dan pengerasan tanpa transformasi polimorfik, untuk kebanyakan logam bukan ferus. Bahan yang dikeraskan memperoleh kekerasan yang lebih besar, tetapi menjadi rapuh, kurang mulur dan likat jika lebih banyak ulangan pemanasan dan penyejukan dilakukan. Untuk mengurangkan kerapuhan dan meningkatkan kemuluran dan keliatan, pembajaan digunakan selepas pengerasan dengan transformasi polimorfik. Selepas pengerasan tanpa transformasi polimorfik, penuaan digunakan. Semasa pembajaan, terdapat sedikit penurunan dalam kekerasan dan kekuatan bahan.
Bergantung pada suhu pemanasan, pengerasan dibahagikan kepada lengkap dan tidak lengkap. Dalam kes pengerasan lengkap, bahan dipanaskan 30 - 50 ° C di atas garisan GS untuk keluli hypoeutectoid dan eutectoid, garis PSK hypereutectoid, dalam kes ini keluli memperoleh struktur austenit dan austenit + simentit. Dalam kes pelindapkejutan yang tidak lengkap, pemanasan dilakukan di atas garis rajah PSK, yang membawa kepada pembentukan fasa yang berlebihan pada penghujung pelindapkejutan. Pengerasan separa biasanya digunakan untuk keluli alat. Pengerasan dikeluarkan dengan membaja bahan. Dalam sesetengah produk, pengerasan dilakukan sebahagiannya, contohnya, dalam pembuatan katana Jepun, hanya mata pedang yang dikeraskan.
Media pemadam
Apabila pelindapkejutan, untuk menyejukkan austenit super kepada suhu transformasi martensit, penyejukan pantas diperlukan, tetapi tidak melebihi julat suhu keseluruhan, tetapi hanya dalam 650-400 °C, iaitu, dalam julat suhu di mana austenit paling tidak stabil dan paling cepat. berubah menjadi ferit-simentit.campuran. Di atas 650 °C, kadar penjelmaan austenit adalah rendah, dan oleh itu campuran semasa pelindapkejutan boleh disejukkan dalam julat suhu ini secara perlahan-lahan, tetapi, sudah tentu, tidak begitu banyak sehingga pemendakan ferit atau perubahan austenit kepada pearlit bermula.
Mekanisme tindakan media pelindapkejutan (air, minyak, medium pelindapkejutan air-polimer (Thermat), serta penyejukan bahagian dalam larutan garam) adalah seperti berikut. Pada masa ini produk direndam dalam medium pelindapkejutan, filem wap panas lampau terbentuk di sekelilingnya; penyejukan berlaku melalui lapisan jaket stim ini, iaitu, agak perlahan. Apabila suhu permukaan mencapai nilai tertentu (ditentukan oleh komposisi cecair pelindapkejutan), di mana jaket wap pecah, cecair mula mendidih pada permukaan bahagian, dan penyejukan berlaku dengan cepat.
Peringkat pertama pendidihan yang agak perlahan dipanggil peringkat pendidihan filem, peringkat kedua penyejukan pantas ialah peringkat pendidihan nukleat. Apabila suhu permukaan logam berada di bawah takat didih cecair, cecair tidak lagi boleh mendidih dan penyejukan akan menjadi perlahan. Peringkat ini dipanggil pemindahan haba perolakan.
Kaedah pengerasan
- Pelindapkejutan dalam satu penyejuk- bahagian yang dipanaskan pada suhu tertentu direndam dalam cecair pelindapkejutan, di mana ia kekal sehingga sejuk sepenuhnya. Kaedah ini digunakan apabila mengeras bahagian mudah yang diperbuat daripada keluli karbon dan aloi.
- Pengerasan berselang-seli dalam dua persekitaran- kaedah ini digunakan apabila mengeras keluli karbon tinggi. Bahagian itu mula-mula cepat disejukkan dalam medium penyejukan cepat (contohnya air), dan kemudian dalam medium penyejukan perlahan (minyak).
- Pengerasan jet terdiri daripada menyembur bahagian dengan aliran air yang kuat dan biasanya digunakan apabila perlu untuk mengeraskan sebahagian daripada bahagian. Dengan kaedah ini, jaket stim tidak terbentuk, yang memberikan kebolehkerasan yang lebih mendalam daripada pelindapkejutan mudah di dalam air. Pengerasan sedemikian biasanya dilakukan dalam induktor dalam pemasangan HDTV.
- Langkah pengerasan- pelindapkejutan, di mana bahagian itu disejukkan dalam medium pelindapkejutan yang mempunyai suhu di atas titik martensit untuk keluli tertentu. Apabila disejukkan dan dipegang dalam persekitaran ini, bahagian yang dikeraskan mesti memperoleh suhu mandi pengerasan di semua titik keratan rentas. Ini diikuti oleh penyejukan akhir, biasanya perlahan, di mana pengerasan berlaku, iaitu, perubahan austenit kepada martensit.
- Pengerasan isoterma. Berbeza dengan pengerasan secara berperingkat, dengan pengerasan isoterma adalah perlu untuk mengekalkan keluli dalam medium pengerasan untuk sekian lama supaya transformasi isoterma austenit mempunyai masa untuk diselesaikan.
CUTI KELULI
Pembajaan keluli melembutkan kesan pengerasan, mengurangkan atau menghilangkan tegasan sisa, meningkatkan keliatan, mengurangkan kekerasan dan kerapuhan keluli. Pembajaan dijalankan dengan memanaskan bahagian yang dikeraskan kepada martensit kepada suhu di bawah kritikal. Dalam kes ini, bergantung pada suhu pemanasan, keadaan martensit, troostit atau sorbitol terbaja boleh diperolehi. Keadaan ini agak berbeza daripada keadaan pengerasan yang sepadan dalam struktur dan sifat: semasa pengerasan, simentit (dalam troostit dan sorbite) diperolehi dalam bentuk plat memanjang, seperti dalam perlit lamellar. Dan apabila marah, ia menjadi berbutir, atau bertitik, seperti dalam perlit berbutir.
Kelebihan struktur titik adalah gabungan kekuatan dan kemuluran yang lebih baik. Dengan komposisi kimia yang sama dan kekerasan yang sama, keluli dengan struktur titik mempunyai penguncupan relatif y dan kekuatan hentaman yang jauh lebih tinggi a n, peningkatan pemanjangan d dan kekuatan alah s t berbanding keluli dengan struktur plat.
Martensit dipadamkan mempunyai kekisi tetragonal yang tidak stabil, manakala martensit terbaja mempunyai kekisi alfa-besi padu berpusat yang stabil.
Percutian dibahagikan kepada rendah, sederhana dan tinggi bergantung kepada suhu pemanasan.
Untuk menentukan suhu semasa mengeluarkan produk, gunakan mencemarkan carta warna . Filem nipis oksida besi yang memberikan logam pelbagai warna yang cepat berubah, daripada kuning muda kepada kelabu. Filem sedemikian muncul jika produk keluli yang dibersihkan dari skala dipanaskan hingga 220C°; Apabila masa pemanasan meningkat atau suhu meningkat, filem oksida menebal dan warnanya berubah. Warna cemar kelihatan sama pada keluli mentah dan keras.
Pada cuti rendah (memanaskan kepada suhu 200-300C°), martensit terutamanya kekal dalam struktur keluli, yang, bagaimanapun, mengubah kekisi. Di samping itu, pemisahan karbida besi daripada larutan pepejal karbon dalam besi alfa bermula dan pengumpulan awalnya dalam kumpulan kecil. Ini memerlukan sedikit penurunan kekerasan dan peningkatan sifat plastik dan likat keluli, serta penurunan tegasan dalaman pada bahagian. Untuk pembajaan rendah, bahagian disimpan untuk masa tertentu, biasanya dalam mandi minyak atau garam. Jika untuk bahagian yang bersuhu rendah dipanaskan di udara, maka warna cemar yang muncul pada permukaan bahagian itu sering digunakan untuk mengawal suhu. Penampilan warna-warna ini dikaitkan dengan gangguan cahaya putih dalam filem oksida besi yang muncul pada permukaan bahagian apabila ia dipanaskan. Dalam julat suhu dari 220 hingga 330C°, bergantung pada ketebalan filem, warna berubah dari kuning muda kepada kelabu. Pembajaan rendah digunakan untuk memotong, mengukur alat dan gear.
Pada purata (pemanasan dalam 300-500C°) dan tinggi (500-700C°) selepas pembajaan, keluli bertukar dari keadaan martensit kepada keadaan troostit atau sorbitol, masing-masing. Semakin tinggi pembajaan, semakin rendah kekerasan keluli terbaja dan semakin besar kemuluran dan keliatannya. Dengan pembajaan tinggi, keluli menerima kombinasi terbaik sifat mekanikal, peningkatan penunjuk seperti kekuatan, kemuluran dan keliatan, oleh itu pembajaan tinggi keluli selepas pengerasan kepada martensit digunakan untuk rawatan haba penempaan acuan, spring, spring, dan pembajaan tinggi digunakan. untuk banyak bahagian yang terdedah kepada suhu tinggi. tegasan (contohnya, gandar kereta, rod penyambung enjin).
Untuk beberapa gred keluli, pembajaan dijalankan selepas penormalan. Ini merujuk kepada keluli hypoeutectoid aloi berbutir halus (terutamanya nikel), yang mempunyai keliatan tinggi dan oleh itu kebolehmesinan yang lemah dengan alat pemotong. Untuk meningkatkan kebolehmesinan, keluli dinormalisasi pada suhu tinggi (sehingga 950-970C°), akibatnya ia memperoleh struktur yang besar (menentukan kebolehmesinan yang lebih baik) dan pada masa yang sama meningkatkan kekerasan (disebabkan oleh kadar pengerasan kritikal yang rendah keluli nikel). Untuk mengurangkan kekerasan, pembajaan tinggi keluli ini dijalankan.
NORMALISASI KELULI
Normalisasi ialah sejenis rawatan haba apabila keluli dipanaskan 30 - 50C° di atas suhu kritikal atas Asz atau Ast dan, selepas menahan pada suhu ini, disejukkan dalam udara pegun. Oleh itu, normalisasi berbeza daripada penyepuhlindapan kerana produk menyejuk lebih cepat (kira-kira 2 kali).
Normalisasi adalah operasi yang lebih murah daripada penyepuhlindapan, kerana relau digunakan hanya untuk memanaskan dan menahan produk pada suhu pemanasan, dan penyejukan dilakukan di luar relau. Di samping itu, normalisasi mempercepatkan proses rawatan haba. Oleh itu, adalah berfaedah untuk menggantikan penyepuhlindapan dengan normalisasi. Walau bagaimanapun, ini tidak selalu mungkin, kerana dalam sesetengah keluli kekerasan selepas normalisasi meningkat dengan lebih ketara daripada semasa penyepuhlindapan. Keluli karbon rendah disyorkan untuk dinormalisasi, kerana ia hampir tidak mempunyai perbezaan dalam sifat selepas penyepuhlindapan dan penormalan.
Keluli yang mengandungi lebih daripada 0.4% karbon memperoleh kekerasan yang meningkat selepas penormalan. Ini mula menyepuh lebih baik. Dalam amalan, keluli sedemikian sering tertakluk kepada normalisasi dan bukannya penyepuhlindapan, dan kemudian pembajaan tinggi pada suhu 650 - 700C° untuk mengurangkan kekerasan. Normalisasi digunakan untuk mendapatkan struktur berbutir halus dalam tuangan dan penempaan, untuk menghapuskan tegasan dalaman dan pengerasan kerja, dan untuk menyediakan struktur keluli untuk pengerasan.
Bagi sesetengah produk, penormalan bukanlah permulaan, tetapi operasi rawatan haba terakhir. Dalam kes ini, selepas penormalan, produk tertakluk kepada pembajaan tinggi untuk melegakan tekanan dalaman yang terbentuk apabila produk disejukkan di udara.
Rawatan haba aloi adalah bahagian penting dalam proses pengeluaran metalurgi ferus dan bukan ferus. Hasil daripada prosedur ini, logam dapat mengubah ciri-cirinya kepada nilai yang diperlukan. Dalam artikel ini kita akan melihat jenis utama rawatan haba yang digunakan dalam industri moden.
Intipati rawatan haba
Semasa proses pengeluaran, produk separuh siap dan bahagian logam tertakluk kepada rawatan haba untuk memberikan mereka sifat yang diingini (kekuatan, ketahanan terhadap kakisan dan haus, dsb.). Rawatan haba aloi ialah satu set proses yang dicipta secara buatan di mana perubahan struktur dan fizikal-mekanikal berlaku dalam aloi di bawah pengaruh suhu tinggi, tetapi komposisi kimia bahan itu dipelihara.
Tujuan rawatan haba
Produk logam yang digunakan setiap hari dalam mana-mana sektor ekonomi negara mesti memenuhi keperluan rintangan haus yang tinggi. Logam, sebagai bahan mentah, perlu meningkatkan sifat prestasi yang diperlukan, yang boleh dicapai dengan mendedahkannya kepada suhu tinggi. Rawatan haba aloi mengubah struktur asal bahan, mengagihkan semula komponen konstituennya, dan mengubah saiz dan bentuk kristal. Semua ini membawa kepada pengurangan ketegangan dalaman logam dan dengan itu meningkatkan sifat fizikal dan mekanikalnya.
Jenis rawatan haba
Rawatan haba aloi logam datang kepada tiga proses mudah: memanaskan bahan mentah (produk separuh siap) ke suhu yang diperlukan, mengekalkannya dalam keadaan tertentu masa yang diperlukan dan penyejukan pantas. Dalam pengeluaran moden, beberapa jenis rawatan haba digunakan, berbeza dalam beberapa cara. ciri teknologi, tetapi algoritma proses secara amnya kekal sama di mana-mana sahaja.
Bergantung pada kaedah pelaksanaan, rawatan haba boleh terdiri daripada jenis berikut:
- Termal (pengerasan, pembajaan, penyepuhlindapan, penuaan, rawatan kriogenik).
- Termo-mekanikal melibatkan pemprosesan pada suhu tinggi dalam kombinasi dengan tegasan mekanikal pada aloi.
- Kimia-terma melibatkan rawatan haba logam dengan pengayaan seterusnya permukaan produk unsur kimia(karbon, nitrogen, kromium, dll.).
Penyepuhlindapan
Penyepuhlindapan ialah proses pengeluaran di mana logam dan aloi dipanaskan pada suhu tertentu, dan kemudian, bersama-sama dengan relau di mana prosedur itu berlaku, mereka menyejukkan dengan sangat perlahan secara semula jadi. Hasil daripada penyepuhlindapan, adalah mungkin untuk menghapuskan ketidakhomogenan dalam komposisi kimia bahan, melegakan tekanan dalaman, mencapai struktur butiran dan memperbaikinya seperti itu, serta mengurangkan kekerasan aloi untuk memudahkan pemprosesan selanjutnya. Terdapat dua jenis jenis pertama dan kedua.
Penyepuhlindapan jenis pertama melibatkan rawatan haba, akibatnya perubahan dalam keadaan fasa aloi tidak ketara atau tiada sama sekali. Ia juga mempunyai jenisnya sendiri: homogenisasi - suhu penyepuhlindapan ialah 1100-1200, dalam keadaan sedemikian aloi disimpan selama 8-15 jam, penyepuhlindapan semula (pada t 100-200) digunakan untuk keluli terpaku, iaitu, cacat apabila ia sudah sejuk.
Penyepuhlindapan tertib kedua membawa kepada perubahan fasa yang ketara dalam aloi. Ia juga mempunyai beberapa jenis:
- Penyepuhlindapan penuh ialah memanaskan aloi 30-50 di atas ciri suhu kritikal bahan tertentu dan penyejukan pada kadar tertentu (200 / jam - keluli karbon, 100 / jam dan 50 / jam - keluli aloi rendah dan aloi tinggi, masing-masing. ).
- Tidak lengkap - pemanasan ke titik kritikal dan penyejukan perlahan.
- Resapan - suhu penyepuhlindapan 1100-1200.
- Isoterma - pemanasan berlaku dengan cara yang sama seperti semasa penyepuhlindapan penuh, tetapi selepas ini, penyejukan pantas dilakukan pada suhu sedikit di bawah kritikal dan dibiarkan sejuk di udara.
- Dinormalkan - penyepuhlindapan lengkap diikuti dengan penyejukan logam di udara dan bukannya di dalam relau.
Pengerasan
Pengerasan adalah manipulasi dengan aloi, tujuannya adalah untuk mencapai transformasi martensit logam, yang mengurangkan kemuluran produk dan meningkatkan kekuatannya. Pengerasan, serta penyepuhlindapan, melibatkan pemanasan logam dalam relau di atas suhu kritikal kepada suhu pengerasan; perbezaannya ialah kadar penyejukan yang lebih tinggi, yang berlaku dalam mandi cecair. Bergantung pada logam dan juga bentuknya, ia digunakan jenis yang berbeza pengerasan:
- Pelindapkejutan dalam satu persekitaran, iaitu, dalam satu mandi dengan cecair (air untuk bahagian besar, minyak untuk bahagian kecil).
- Pelindapkejutan berselang-seli - penyejukan berlaku dalam dua peringkat berturut-turut: pertama dalam cecair (penyejuk yang lebih tajam) hingga suhu kira-kira 300, kemudian di udara atau dalam mandian minyak yang lain.
- Berlangkah - apabila produk mencapai suhu pengerasan, ia disejukkan untuk beberapa lama dalam garam cair, diikuti dengan penyejukan dalam udara.
- Isoterma - teknologi ini sangat serupa dengan pengerasan langkah, hanya berbeza dalam masa pendedahan produk pada suhu transformasi martensit.
- Pelindapkejutan dengan pembajaan diri berbeza daripada jenis lain kerana logam yang dipanaskan tidak disejukkan sepenuhnya, meninggalkan kawasan hangat di tengah bahagian. Hasil daripada manipulasi ini, produk memperoleh sifat peningkatan kekuatan pada permukaan dan kelikatan tinggi di tengah. Gabungan ini amat diperlukan untuk alat perkusi (tukul, pahat, dll.)
bercuti
Pembajaan adalah peringkat akhir rawatan haba aloi, menentukan struktur akhir logam. Tujuan utama pembajaan adalah untuk mengurangkan kerapuhan produk logam. Prinsipnya adalah untuk memanaskan bahagian pada suhu di bawah kritikal dan menyejukkannya. Oleh kerana mod rawatan haba dan kadar penyejukan produk logam untuk pelbagai tujuan mungkin berbeza, terdapat tiga jenis pembajaan:
- Suhu pemanasan tinggi dari 350-600 kepada nilai di bawah kritikal. Prosedur ini paling kerap digunakan untuk struktur logam.
- Sederhana - rawatan haba pada t 350-500, biasa untuk produk musim bunga dan mata air daun.
- Rendah - suhu pemanasan produk tidak lebih tinggi daripada 250, yang membolehkan anda mencapai kekuatan tinggi dan rintangan haus bahagian.
Penuaan
Penuaan adalah rawatan haba aloi yang menyebabkan penguraian logam supertepu selepas pengerasan. Hasil daripada penuaan adalah peningkatan dalam had kekerasan, kecairan dan kekuatan produk siap. Bukan sahaja besi tuang, tetapi juga aloi aluminium mudah ubah bentuk mengalami penuaan. Jika produk logam yang mengalami pengerasan disimpan pada suhu biasa, proses berlaku di dalamnya yang membawa kepada peningkatan spontan dalam kekuatan dan penurunan kemuluran. Ini dipanggil penuaan semula jadi logam. Jika manipulasi yang sama dilakukan dalam keadaan suhu tinggi, ia akan dipanggil penuaan buatan.
Rawatan cryogenic
Perubahan dalam struktur aloi, dan oleh itu sifatnya, boleh dicapai bukan sahaja tinggi, tetapi juga sangat suhu rendah. Rawatan haba aloi pada suhu di bawah sifar dipanggil kriogenik. Teknologi ini digunakan secara meluas dalam pelbagai sektor ekonomi negara sebagai pelengkap kepada rawatan haba suhu tinggi, kerana ia dapat mengurangkan dengan ketara kos pengerasan haba produk.
Pemprosesan kriogenik aloi dijalankan pada t -196 dalam pemproses kriogenik khas. Teknologi ini boleh meningkatkan hayat perkhidmatan bahagian yang dirawat dan sifat anti-karat dengan ketara, serta menghapuskan keperluan untuk rawatan berulang.
Rawatan termo-mekanikal
Kaedah baharu pemprosesan aloi menggabungkan pemprosesan logam dengan suhu tinggi dengan ubah bentuk mekanikal produk dalam keadaan plastik. Rawatan termomekanikal (TMT) boleh terdiri daripada tiga jenis mengikut kaedah pelaksanaan:
- TMT suhu rendah terdiri daripada dua peringkat: ubah bentuk plastik diikuti dengan pengerasan dan pembajaan bahagian. Perbezaan utama daripada jenis TMT yang lain ialah suhu pemanasan kepada keadaan austenit aloi.
- TMT suhu tinggi melibatkan pemanasan aloi kepada keadaan martensit dalam kombinasi dengan ubah bentuk plastik.
- Ubah bentuk awal dilakukan pada t 20 diikuti dengan pengerasan dan pembajaan logam.
Rawatan kimia-terma
Ia juga mungkin untuk menukar struktur dan sifat aloi menggunakan rawatan kimia-terma, yang menggabungkan kesan haba dan kimia pada logam. Matlamat utama prosedur ini, sebagai tambahan untuk memberikan peningkatan kekuatan, kekerasan, dan rintangan haus kepada produk, juga untuk memberikan bahagian rintangan asid dan rintangan api. Kumpulan ini termasuk jenis rawatan haba berikut:
- Penyimenan dijalankan untuk memberikan permukaan produk kekuatan tambahan. Intipati prosedur adalah untuk memenuhi logam dengan karbon. Penyimenan boleh dilakukan dalam dua cara: pengkarburan pepejal dan gas. Dalam kes pertama, bahan yang sedang diproses, bersama-sama dengan arang batu dan pengaktifnya, diletakkan di dalam relau dan dipanaskan pada suhu tertentu, diikuti dengan mengekalkannya dalam persekitaran ini dan penyejukan. Dalam kes pengkarbonan gas, produk dipanaskan dalam relau hingga 900 di bawah aliran berterusan gas yang mengandungi karbon.
- Nitriding ialah rawatan kimia-terma produk logam dengan menepu permukaannya dalam persekitaran nitrogen. Hasil daripada prosedur ini adalah peningkatan dalam kekuatan tegangan bahagian dan peningkatan dalam rintangan kakisannya.
- Sianidasi ialah ketepuan logam dengan kedua-dua nitrogen dan karbon. Medium boleh menjadi cecair (garam yang mengandungi karbon dan nitrogen cair) dan gas.
- Metalisasi resapan ialah kaedah moden memberikan rintangan haba, rintangan asid dan rintangan haus kepada produk logam. Permukaan aloi tersebut tepu dengan pelbagai logam (aluminium, kromium) dan metalloid (silikon, boron).
Ciri-ciri rawatan haba besi tuang
Aloi besi tuang tertakluk kepada rawatan haba menggunakan teknologi yang sedikit berbeza daripada aloi logam bukan ferus. Besi tuang (kelabu, kekuatan tinggi, berali) menjalani jenis rawatan haba berikut: penyepuhlindapan (pada t 500-650 -), normalisasi, pengerasan (berterusan, isoterma, permukaan), pembajaan, nitriding (besi tuang kelabu), pengaluminan (besi tuang mutiara), penyaduran krom. Akibatnya, semua prosedur ini dengan ketara meningkatkan sifat produk besi tuang akhir: ia meningkatkan hayat perkhidmatan, menghapuskan kemungkinan retak semasa penggunaan produk, dan meningkatkan kekuatan dan rintangan haba besi tuang.
Rawatan haba aloi bukan ferus
Logam dan aloi bukan ferus mempunyai sifat yang berbeza dan oleh itu diproses menggunakan kaedah yang berbeza. Oleh itu, aloi kuprum menjalani penyepuhlindapan penghabluran semula untuk menyamakan komposisi kimia. Untuk loyang, teknologi penyepuhlindapan suhu rendah (200-300) disediakan, kerana aloi ini terdedah kepada keretakan spontan dalam persekitaran lembap. Gangsa tertakluk kepada homogenisasi dan penyepuhlindapan pada suhu sehingga 550. Magnesium disepuhlindap, dikeraskan dan tertakluk kepada penuaan buatan (penuaan semula jadi tidak berlaku untuk magnesium yang mengeras). Aluminium, seperti magnesium, tertakluk kepada tiga kaedah rawatan haba: penyepuhlindapan, pengerasan dan penuaan, selepas itu aloi aluminium tempa meningkatkan kekuatannya dengan ketara. Pemprosesan aloi titanium termasuk: pengerasan, penuaan, nitriding dan pengkarbonan.
Ringkasan
Rawatan haba logam dan aloi adalah proses teknologi utama dalam metalurgi ferus dan bukan ferus. Teknologi moden mempunyai pelbagai kaedah rawatan haba yang memungkinkan untuk mencapai sifat yang dikehendaki bagi setiap jenis aloi yang diproses. Setiap logam mempunyai suhu kritikalnya sendiri, yang bermaksud bahawa rawatan haba mesti dijalankan dengan mengambil kira ciri-ciri struktur dan fizikokimia bahan tersebut. Akhirnya, ini akan membolehkan bukan sahaja untuk mencapai hasil yang diinginkan, tetapi juga untuk menyelaraskan proses pengeluaran dengan ketara.